I was interviewed for a weekend public affairs program that aired on multiple radio stations in the Denver area two weekends ago, talking about Lean in healthcare and my upcoming Healthcare Kaizen book.
Here is the audio:
Thanks for listening!
Many healthcare facilities have adopted Lean Management techniques to streamline their operations and minimize waste, bringing an unprecedented shift in healthcare delivery. Denver Health, for instance, has made significant strides in patient care and safety through lean management. Lean management principles provide practical solutions to these complex challenges and presents structured strategies for combating medical and surgical errors to reduce patient harm drastically.
Automated Transcript:
Announcer:
You're listening to Colorado today with Jill West.
Jill West:
And with me on the phone is Mark Graban, who is the author of the book Lean Hospitals: improving quality, patient safety and employee engagement. And also he has a new book coming out called Healthcare Kaizen: Engaging frontline staff in sustainable, continuous improvements. Hi, Mark. It's great to have you on the show.
Mark Graban:
Hi, Joel. Thanks for having me here.
Jill West:
So this sounds like a really interesting book. And you say in the book that studies estimate 100,000 Americans die each year due to preventable medical errors and another 100,000 die as a result of hospital-acquired infections. That's a pretty drastic number.
Mark Graban:
Yeah, I think that's really shocking to people. It's not as widely publicized as other types of accidents. The studies show medical errors would be the 8th leading cause of death in the United States. It kills more people than things like breast cancer and car accidents. I think what people working in healthcare learn, and I've seen this firsthand, is that these errors aren't caused by a lack of medical training or lack of skill or bad individuals.
Mark Graban:
These aren't medical problems. I refer to these as management problems, meaning that it's really just about systems and communication. These are things that can be fixed from a management perspective. In a lot of cases, people in hospitals know what they need to do to provide the best patient care and prevent errors, but those things just aren't happening. So the bad news is that there's far too much harm occurring to patients.
Mark Graban:
The good news is that this is actually pretty fixable. And we're seeing a lot of good news stories throughout the US and around the world from organizations that are using this lean methodology.
Jill West:
So, Mark, I guess the thing that surprises me the most about these statistics is that the cost to stay in a hospital anymore is just skyrocketing. It's outrageous and it's beyond the reach of what most people can afford. So you would think that the amount of money that is spent for healthcare in this country, that we wouldn't have problems like this?
Mark Graban:
Yeah, you're right. I mean, healthcare is more expensive in the United States than it is anywhere in the world. And unfortunately, we're not getting great quality for what we're spending. A lot of times, people would assume that we get better quality by spending more. But if you want to make a parallel to cars, you could have a very basic, inexpensive car that breaks down a lot, or you could have a luxury sedan that breaks down a lot.
Mark Graban:
In healthcare, the things that lead healthcare to be expensive are the things that lead to healthcare having poor quality. So when we see disorganization, when we see breakdowns in processes, miscommunications, bad handoffs between departments in a hospital or bad handoffs between shifts, these types of problems, it's fixable. And when we make improvements using what we call this lean management system, we find we get better quality and lower cost. For example, Denver Health in Colorado has done a lot of great work with lean methodologies over the last seven or eight years. They've saved a lot of money, and they have a lot of data that shows they've improved patient care as well.
Jill West:
When I was in the hospital when I had my son, this was 16 years ago, I remember in the middle of the night, my IV ran out, and the nurse came running in, and she seemed like she was in a real big hurry to get that out of my arm. And I didn't learn till later that that could have been something that could have killed me.
Mark Graban:
Did they admit, was this a case where it was a wrong medication or a wrong dose?
Jill West:
Oh, no. The liquid ran out of the bag.
Mark Graban:
Oh, so the fact that you weren't getting medication, so I guess air bubbles.
Jill West:
It couldn't go into your blood.
Mark Graban:
Yeah. Right. And so you think, well, why didn't somebody discover that? And a lot of times it's because the nurses were frantically running around fixing some other problem. And this is where we refer to this, as the waste in the process.
Mark Graban:
Instead of nurses being able to calmly go from patient to patient and room to room, they're running around looking for things. You think, well, why should it be so hard for a nurse to find an iv pole or to find medications? There's just a lot of. It's surprising to people, a lot of disorganization in hospitals. So the lean methodology helps us solve a lot of those systemic things that would have prevented that nurse from being there to change out your iv at the right time before it got to be something that was really threatening your safety.
Jill West:
So what are some of the other common mistakes that happen in hospitals?
Mark Graban:
Well, some of the most common errors are medication errors, either the wrong dose or the wrong medication. Surgical errors, leaving objects inside of a patient, as ridiculous as that might sound, sponges or gauze or even instruments. You have pathology errors. You have situations where patient specimens get mixed up just due to procedural problems in the laboratory, and then, as you often see on the news, the wrong patient ends up getting cancer surgery because the diagnosis was mixed up with the wrong patient. And then you have a whole class of errors that tend to occur because nurses and healthcare professionals can't be at the bedside enough with the patients because they're running around dealing with all of that waste.
Mark Graban:
So you have hospital-acquired infections, you have patients who fall, you have patients who develop bed sores, because one example of a good practice is that hospitals know when they have patients at risk for developing a bed sore, that they need to be repositioned every 2 hours or so, so that they're not just laying the same way, and that two hour repositioning just often doesn't happen because there's just so much chaos and people are overwhelmed. And again, this isn't that we've got bad nurses or poorly trained patient care techs. They're just dealing with way too many problems, and the patient suffers. And it creates a stressful workplace for the nurses because they want to be at the bedside taking care of people. They don't want to be running around fighting the same fires and jumping through the same hoops day in and day out.
Jill West:
And isn't there a lot of paperwork to be done as well because of the insurance companies?
Mark Graban:
Well, there's a lot of paperwork. There's a lot of charting. Some of it is for the sake of getting paid. Some of it is just to try to have good communication between nurses that are taking care of patients on different shifts between nurses and doctors. There's some instances where electronic medical records free up.
Mark Graban:
I guess the promise is that computer systems will free up some of that time. But some of these computer systems are difficult to use, and we may replace one type of error. We don't have medication errors because of bad handwriting, but we may have medication errors because somebody clicked the wrong box on a screen. So, yeah, paperwork, administrative tasks, those are the types of things that we would like to try to try to streamline so that nurses can spend more time at the bedside. It's incredibly difficult.
Mark Graban:
I have the utmost respect for healthcare professionals of the years and years of education that they have. And the process is meant to wean out people who aren't willing to work hard, people who aren't smart. People in healthcare are very smart. They're hardworking, they're incredibly caring. And that's why these errors can really only be explained as being system problems as opposed to being people problems.
Mark Graban:
There's some temptation when an error occurs to punish the individual who is involved to suspend them or fire them, or there have been some cases around the country where nurses or pharmacists have actually been convicted and imprisoned because of an error. And people in the patient safety profession. The patient safety movement would argue that it's incredibly unfair and counterproductive to blame individuals for system problems. Because when we blame individuals, that drives people to hide mistakes and cover up problems, and when we aren't open and honest about near misses or mistakes that occurred, it's really hard to learn from those mistakes and to make improvements that would help protect patients in the future.
Jill West:
In the two books that you've written and also you have a blog, it's called leanblog.org. What are some of the recommendations that you haven't already discussed that you're looking at to solve some of these problems?
Mark Graban:
Sure. There's a number of things that can help address these problems of poor quality and high cost. I think for one, the leadership involvement that's required really makes a big difference. And so, for example, when we look at things like preventable infections and other types of errors, instead of the old mindset of saying, well, these types of problems are inevitable or they're just bound to happen. Leadership has to set a really high bar and say that the goal is zero patient harm.
Mark Graban:
We have to think that that's even possible to be able to inspire people to work together to improving systems and processes that can actually prevent errors. So there's a big culture change that's required. There's a lot of involved leadership, shifting the culture from one of blaming and punishing individuals to one that's focused on improving systems and processes. And I think with that, one of the other things that really works well is involving healthcare professionals in improving their own work. So the lean improvement methodology isn't about me or somebody else coming in as an outside expert and saying, well, here's the ten things you need to do.
Mark Graban:
It's about teaching healthcare professionals and the people who work in support systems like materials management and housekeeping, teaching them how to analyze their own work, to figure out how they can reduce waste, how they can make improvements that are going to free up time and help provide the best patient care. So it takes a lot of leadership at all levels, from the CEO of the hospital all the way down to frontline managers. It's really a different way of thinking, a different way of managing. It's not a quick fix, but it's a methodology that leads to some really great results. When hospitals have dedicated this to themselves, after a couple of years, they start to see some really big improvements in terms of quality and patient safety and cost increasing capacity so that patients don't wait as long.
Mark Graban:
In the emergency department, for example. Those are the types of improvements that we see in, quote unquote, lean hospitals.
Jill West:
Okay. And if people would like to get more information, they can go to your blog, which is leanblog.org. Or also tell me the name of the upcoming book that you have.
Mark Graban:
Right. So the book is called Healthcare Kaizen. And Kaizen is a Japanese word that means change for the better, or it's usually used in the context of continuous improvement. So that's what we're doing in healthcare, is that we're engaging healthcare professionals and figuring out how to make improvements every day, every week, every month. And people can learn more, hchaizen.com, which stands for healthcarekaizen.com, or they can find the book in the typical online bookstores.
Jill West:
All right. Well, thank you so much, Mark. We really appreciate you taking the time to talk to us today.
Mark Graban:
Well, thank you, Jill.
Announcer:
Colorado Today with Jill West is a weekly public affairs presentation of Intercom Denver Radio, LLC. Comments on today's program are welcome. Call us at 303-967-2708 if you'd like a copy of today's show, please contact us. Our website is intercomdenver.com. Our address is 4700 South Syracuse Street, Suite 1050, Denver, Colorado 80237.
Announcer:
Thanks for listening to Colorado today.
Please scroll down (or click) to post a comment. Connect with me on LinkedIn.
Let’s work together to build a culture of continuous improvement and psychological safety. If you're a leader looking to create lasting change—not just projects—I help organizations:
- Engage people at all levels in sustainable improvement
- Shift from fear of mistakes to learning from them
- Apply Lean thinking in practical, people-centered ways
Interested in coaching or a keynote talk? Let’s start a conversation.
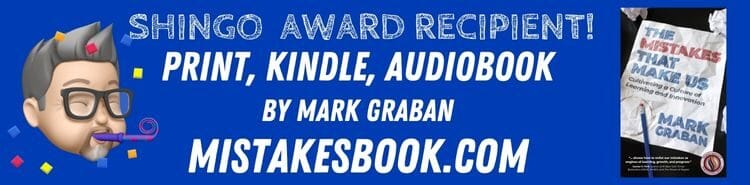