After a week of serious topics and sometimes pointed discussion, let's end with a funny sign… well wait, there's a serious story behind this sign too.
This is a sign from a New Zealand hospital, sent via email by a blog reader who attended the debut of my “Warning: Signs!” talk at Cindy Jimmerson's lean healthcare conference last year.
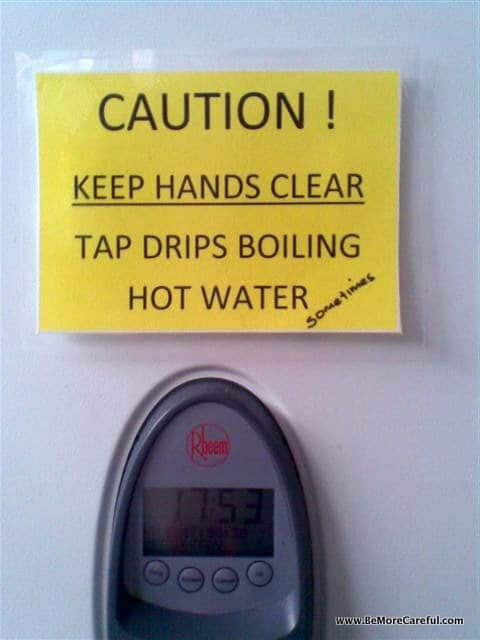
The key theme of my “Warning: Signs!” talk is that workplace signs are often a visual indicator of a case where the root cause of a problem hasn't been solved. Yes, some workplaces are necessary and/or required by law, but I'm talking about the signs that are slapped up in place of a real systemic solution. Signs are, at best, a short-term countermeasure or containment strategy.
In this case, the “target condition” might be to have a tap that does not burn people with boiling water. The “current condition” is that the tap does burn people. Well, “sometimes” (see the hand written note on the sign).
So maybe that “sometimes” makes it harder to determine why water is too hot, but you'd think that's something a plumber could fix. Sometimes, it's too hard (too bureaucratic or too slow) to get the facilities department to come fix something. Or, maybe a manager says “well, you know the water is hot…. so be careful.”
Whether it's general workplace safety or the important topic of patient safety, having careful people is a good starting point, but it's never fully sufficient for quality and safety. That's why we use error proofing and checklists – to protect “good people from having a bad day,” not because they're careless, or stupid, or whatever insult you might throw at them.
People want to quality work. People want to not get burned by a water tap! Leaders need to create systems that ensure quality and safety and systems that respond to the needs of staff and patients. They also need to make sure that people are coached and mentored on good problem-solving skills.
So, the next time you go to the gemba (the place where value adding work is done), keep your eyes peeled for signs like these and keep in mind that the sign is a symptom of problem, not a solution. To get familiar with these signs, scan through BeMoreCareful.com (click here for a random sign) — it might make you chuckle and it might make you think.
Please scroll down (or click) to post a comment. Connect with me on LinkedIn.
Let’s build a culture of continuous improvement and psychological safety—together. If you're a leader aiming for lasting change (not just more projects), I help organizations:
- Engage people at all levels in sustainable improvement
- Shift from fear of mistakes to learning from them
- Apply Lean thinking in practical, people-centered ways
Interested in coaching or a keynote talk? Let’s talk.
Join me for a Lean Healthcare Accelerator Trip to Japan! Learn More
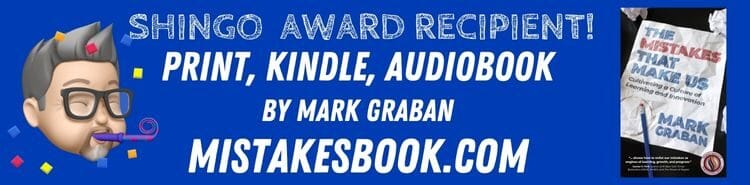