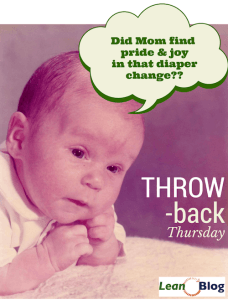
To the left is a young baby me. I don't think I was thinking about Dr. Deming as a baby, but thankfully my parents had a lot of intrinsic motivation to take care of me!
One of the many things I admire about W. Edwards Deming is how hard he worked into his 90s. He must have had “pride and joy” in his own work.
I learned from this IndustryWeek piece that Dr. Deming was teaching seminars up until two weeks before his death at age 93.
IndustryWeek was kind enough to share Dr. Deming's last interview, originally published in January 1994, on their website in three parts.
Part 1
Part 2
Part 3
A few highlights… on innovation:
IW: What then is the source of innovation?
Dr. Deming: The source of innovation is freedom. All we have–new knowledge, invention–comes from freedom. Somebody responsible only to himself has the heaviest responsibility. “You cannot plan to make a discovery,” Irving Langmuir said. Discoveries and new knowledge come from freedom. When somebody is responsible only to himself, [has] only himself to satisfy, then you'll have invention, new thought, now product, new design, new ideas.
IW: How does a company, a research manager, a manager of people create an environment where there is freedom?
Dr. Deming: Give people a chance to make use of their diverse abilities, capabilities, family life, education, hopes. Help them to accomplish their aim.
And, on performance reviews and joy in work:
IW: What is the alternative [to performance appraisals]?
Dr. Deming: The alternative is joy on the job. To have it, people must understand what their jobs are, how their work fits in, how they could contribute. Why am I doing this? Whom do I depend on? Who depends on me? Very few people have the privilege to understand those things. Management does not tell them. The boss does not tell them. He does not know what his job is. How could he know? When people understand what their jobs are, then they may take joy in their work. Otherwise, I think they cannot.
Dr. Samuel Culbert continues this fight today, if you'd like to listen to my podcast with him on “Get Rid of the Performance Review!“
And on Baldrige:
IW: What about the Malcolm Baldrige National Quality Award and companies striving for the award. Does that equate to being on a mission to improve quality?
Dr. Deming: No, nothing could be worse. The evil effect of the Baldrige guidelines on American business can never be measured. If you had the Baldrige guidelines in front of you, you would see it asks for data, figures on what cannot be measured. The effect of training, for example. You may spend $20,000 to train six people in a skill. That benefit will come in the future. We'll never be able to measure that benefit. Never. So why do we spend that money for training? Answers are guided by theory. We believe that that training will have its effect on future output. And though we cannot measure that effect, we believe that it is positive. In other words, we govern our actions, our life, by theory. That's good. Without theory, we learn nothing. Theory has temporal spread. That is, the theory that we can hold on to must fit without failure events of the past and predict events of the future.
And on business schools:
IW: Where are American business schools falling short ill design of their curriculum, the things they are teaching?
Dr. Deming: I'm afraid that what they teach is continuance of our present methods of management, which are failures. They teach how to fail, how to continue to fail.
IW: What should they be teaching?
Dr. Deming: I think the teaching ought to be on how to improve. Improvement, understanding of people, understanding of product. In other words, it would require what I call profound knowledge, of which I mean a view from the outside.
I talked last week with John Dyer, an IndustryWeek columnist who got to work with Dr. Deming a bit through GE (they are pictured together in his Twitter and LinkedIn profiles). He told stories about how some parts of GE were trying to learn from Dr. Deming during the Jack Welch era.
Recently, when researching some origins of Six Sigma, I accidentally discovered what Jack Welch wrote about Dr. Deming in his book Straight from the Gut. He (or his ghostwriter) wrote:
“In the early 1990s, we flirted with a Deming program in our aircraft engine business. I didn't buy it as a companywide initiative because I thought it was too theoretical.”
He said Deming's ideas were “too theoretical.” Hmmm… it's probably more like Jack disagreed with most of Deming's 14 points. Jack Welch loved performance appraisal, among other things.
I'm not sure what “a Deming program” is anymore than I know what “a Lean program” is sometimes.
You either adopt the new philosophy and new approach or not. GE didn't. Most organizations didn't.
What do you think? Please scroll down (or click) to post a comment. Or please share the post with your thoughts on LinkedIn – and follow me or connect with me there.
Did you like this post? Make sure you don't miss a post or podcast — Subscribe to get notified about posts via email daily or weekly.
Check out my latest book, The Mistakes That Make Us: Cultivating a Culture of Learning and Innovation:
Deming sure provided some great quotes in that interview; those you listed above and more.
“I’m not sure what ‘a Deming program’ is anymore than I know what ‘a Lean program’ is sometimes.”
This is so true. Basically organizations can be making good progress but to really I know essentially none that *have* a Deming or lean program. Toyota is sensible to consider the closest – I mean lean after all was just documenting Toyota and calling it lean instead of Toyota management or whatever.
But Toyota does plenty of things that are not what even Toyota says how things should be done. And beyond that lean has evolved away, IMO, from just being able to say anything Toyota does is by definition lean.
Lean and Deming are more about a philosophy of managing – continual improvement, respect for people, etc. than prescriptions. So you can’t really have a checklist and say that if your org can check off all these things they are lean or Deming.
The fact that the management systems can’t be reduced to a checklist is a reason for the power of them. When you reduce the ideas for management that far you get a stupid system that can’t be used for managing large systems of people.
Organizations doing the best job of being worth of claims of being true to the management systems are likely to have the widest understanding of all the ways in which they are failing to live up to that vision.
I continue to think Toyota is doing a very good job. But they also have plenty of room to improve. And they continue to be tempted by becoming more like other companies instead of recommitting to the principles of lean and Deming.
What a powerful thought. Innovation = freedom. So true, yet so few seem to be able to put this into practice as companies squeeze out every minute and fear the freedom will become facebook time/wasted.
But GE have been a very successful company so the analysis “we were right and they were wrong” will persuade no one.
The truth is that Deming’s thinking is at its strongest when it draws on theoretical ideas from probability and statistics. That’s why people think it “too theoretical”.
Against that, I’m sure that nobody in GE Capital found the Black-Scholes equation too theoretical but I doubt that Jack Welch got involved in those decisions.
We need a new synthesis. Six Sigma promised to be that but became cluttered through being too uncritically eclectic.
Deming would have been horrified that his thinking has been chiselled into tablets of stone while the world has moved on.
Anthony – Good points.
Nothing should be carved in stone, but I’m curious about what ideas from Dr. Deming aren’t applicable anymore because “the world has moved on”?
Dr. Deming used outdated gender specific language (referring to leaders and employees as “he”) but I think his principles and ideas are pretty timeless.
I’d also add that Jack Welch’s mindsets were based on theory (namely “Theory X,” that people are lazy and don’t want to work with out proper incentives).
Dear Mark, please accept my apologies for not having replied sooner. With respect, I think that when you refer to Welch’s beliefs as “Theory X” you fail to do him justice. Human thoughts and emotions are complex. People are capable of being lazy, passionate and passionate about the wrong things. And sometimes all at the same time. I know that I am. Sadly, the thread safety is closer to c++ than java.
Money, fear, appraisals and money are much more important motivators than Deming was prepared to admit. Not every effect can be explained away as regression to the mean. I can assure you that there are plenty of things that I would never do save for money or fear.
Welch made GE a success despite ignoring much of Deming’s prescription as to the management of people. In vulgar PDSA terms, some of Deming’s theories have been falsified. It would be more within the spirit of continual learning to seek to understand why that is, and amend our thinking, rather than to censure Welch.
Thanks for your comment, Anthony.
I’m not one who subscribes to “the Gospel according to Deming” in that his ideas are always right or infallible.
I’m curious though, to hear more about which of his theories you think have been disproven. How do you prove or disprove a philosophy?
The thought experiment that we can never know the answer to is whether or not Welch and GE would have been MORE successful if they had adopted Dr. Deming’s practical ideas (such as doing away with stack ranking, annual performance appraisals, etc). They might have successful in spite of what they did, not because of it.
We can never know.
Mark, I think you go too far in describing Deming’s imperfectly worked out strategy as a philosophy. Of course, you are right that we can never do the experiment. However, in Out of the Crisis, Deming described how materially shabby life was in the 1970s. He put forwards his strategy as the solution and warned that some of the alternatives would be ruinous. Deming was ignored. The deprecated alternatives were widely adopted. Life now is much better than the 1970s.
Yet much of what Deming said remains interesting, not as a platform for advocacy, but as a basis for enquiry. That is why I am more interested in why GE succeeded than in criticising them.
There might be a lot of people like me.
OK, thanks for elaborating.
Ok, so Jack Welch wasn’t the only one to think Deming wasn’t practical.
From this Inc. article, written when Deming was still alive:
I can’t resist playing devil’s advocate. I can read Deming as making a very exact practical proposal of what to do. “Base every organisational decision from the board down on a rigorous understanding of the difference between signal and noise (special and common cause)”.
Nobody has every done that and I have barely even heard it advocated outside “Out of the Crisis”.
Where it has all gone wrong is in thinking that you can get bottom-up improvement inspired by a cadre of middle management specialists, without the organisation wide/high numeracy.
Anthony – great point.
There are some of us who very actively teach special cause vs. common cause, using SPC and general variation thinking. Like Mike Stoecklein, for example. It’s still pretty rare. See his paper. And Don Wheeler’s book “Understanding Variation” — but that book has a limited audience and impact, as brilliant as it is.
Most organizations haven’t abolished the annual performance review, but it’s interesting to see that Accenture has.
Deming also said to cease reliance on inspection, stop using slogans and targets… but the world mainly hasn’t listened. I’d like to think that’s a big competitive advantage for companies that DO think and act this way.
I think I’ve sold as many copies of “Understanding Variation” as anybody.
Let’s start a meme:
#executivetimeseries