NUMMI Tour Tale #1: Why Fix the Escalator?
NUMMI Tour Tale #2: The Power of Reynolds Wrap
I think, by now, that Toyota is pretty famous for it's “5 Whys” approach for root cause problem solving. Asking why five times, in succession will likely get to the root cause of any problem. I've seen it applied to safety investigations, for example — why did the worker trip and fall? Usually, it points back to training and leadership issues, but that's another story.
One thing I noticed at NUMMI was that you can “ask” why but it's also important to “explain” why. Many of the signs and visual controls I saw included a “why” element to them. To me, this seems to illustrate the idea of having respect for your employees and your workforce. This idea is also illustrated in NUMMI Tour Tale #1: Why Fix the Escalator?
When I worked at GM, which was not as Lean as NUMMI, it was pretty common to see a box of parts tagged with a sign that said, sternly, “DO NOT USE.” Sometimes there was an important manager's name associated to illustrate who was making that pronouncement.
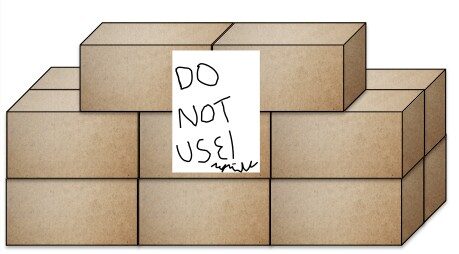
At NUMMI, a box was labeled with a sign that included the “why.” The sign said something like “using these parts would result in brake failures or problems for the customer.”
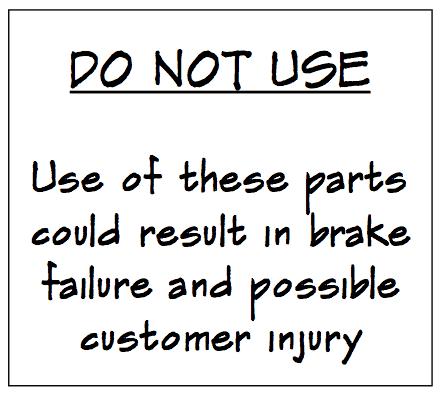
Again, another “wow” moment. For one, NUMMI put the situation in customer terms. Do not use these parts, because there would be a negative impact on the customer. It didn't say, “Do not use the parts because I say so (and you wouldn't understand the reason anyway).” Secondly, if the line was in a pinch and had no other parts, it seems less likely that someone would feel pressured into using those parts, being reminded of the customer and a potentially dangerous situation that would be created.
So, my challenge is to explain “why” as much as possible. Not just asking why, but explaining why. I hope you can take that challenge on for yourself. Why are we doing lean? Why is it necessary to standardize our workbenches? Why is it important to get these parts off MRP and onto a kanban system? I bet we would all do better by taking the time to explain why.
NUMMI Tour Tale #4: The Pull Gift Shop
Please scroll down (or click) to post a comment. Connect with me on LinkedIn.
Let’s work together to build a culture of continuous improvement and psychological safety. If you're a leader looking to create lasting change—not just projects—I help organizations:
- Engage people at all levels in sustainable improvement
- Shift from fear of mistakes to learning from them
- Apply Lean thinking in practical, people-centered ways
Interested in coaching or a keynote talk? Let’s start a conversation.
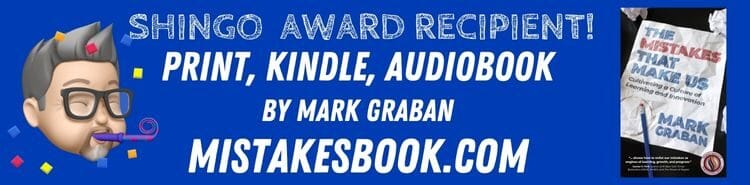
[…] the order. I wrote about a similar theme a few years ago after I toured the NUMMI plant (“NUMMI Tour Tale #3: The Power of Why“). So, my challenge is to explain “why” as much as possible. Not just asking why, but […]
[…] NUMMI Tour Tale #3: The Power of Why […]
[…] If the consultants asked each accountant where they wanted their items, that might have been one positive sign — showing the slightest bit of respect for people in that sense, perhaps. So why did employees find it degrading? Probably because the consultants didn’t explain “why”, as Toyota would tend to do. […]
[…] must “explain why” to employees if they give a directive order. I saw this when I visited the NUMMI plant and wrote about how they treated employees like adults by explaining why certain defective parts shouldn’t be […]
[…] “Why” you shouldn’t put cups up there. As I’ve blogged about before, a key point of the Toyota Production System is the power of EXPLAINING “why” to people, not just asking “why?” This point is often overlooked or not talked about. […]
[…] Go To NUMMI Tour Tale #3: The Power of Why […]