It's hard to believe, but it's been almost 17 years since the first edition of Lean Hospitals was published–an effort that eventually received the Shingo Research and Professional Publication Award and has since reached tens of thousands of healthcare professionals around the world.
When I wrote that first edition, Lean in healthcare was still new territory. Many leaders were still asking, “Will Lean work in healthcare?” Today, the better question is “How can we make it work–and sustain it?”
To mark the occasion, I've been reflecting on some of the key ideas from the book–concepts that continue to resonate with readers, leaders, and improvement professionals.
“Lean is not a quick fix or a project. It's a way of thinking, a way of managing, and a culture of continuous improvement.”
Too often, organizations treat Lean like a flavor-of-the-month toolkit–something to roll out, evaluate, and eventually shelve. But Lean is more than a set of tools. It's a way of looking at work, people, and problems with humility and curiosity. This message still holds up, and I expanded on it in Healthcare Kaizen (another Shingo Award recipient), where Joe Swartz and I focused on how daily improvement–not just episodic events–can transform culture and results.
Hear Mark read this post — subscribe to Lean Blog Audio
“Lean helps leaders see and understand that it is not the individuals who are broken, but the system itself.”
This mindset shift–blame the process, not the person–is still one of the most vital (and often most difficult) parts of Lean transformation. I explore this further in The Mistakes That Make Us (Shingo Award #3), where I write about creating psychologically safe environments where mistakes are treated as learning opportunities rather than personal failures. When we stop blaming people and start improving systems, everyone benefits–including the patient.
“Lean doesn't mean doing more with less. It means doing the right things with the right resources, without waste.”
This one has always been important to clarify, especially in healthcare settings where the word “lean” is often misinterpreted as “cutting to the bone.” True Lean provides support–not strain–for people doing the work. Lean gives time back to clinicians and staff by removing barriers, waste, and frustration. It's not about squeezing more out of fewer people; it's about letting good people succeed in better systems.
“A Lean health system respects and supports staff–it doesn't overburden, blame, or ignore them.”
This goes to the heart of Respect for People, one of the two foundational pillars of the Toyota Way. In my experiences–whether at the bedside, in the lab, or in an executive boardroom–this principle is often forgotten when Lean is applied in a superficial or top-down manner. Respect isn't just about being nice; it's about listening, engaging, and designing systems that allow people to thrive. That's something I continue to write and speak about in all of my work.
“The goal isn't perfection. The goal is to get a little better every day, together.”
This idea connects directly to the spirit of kaizen. It's about progress, not perfection. We don't need dramatic, one-time changes to make meaningful improvement–we need consistency, reflection, and learning. That mindset is what powers organizations with vibrant improvement cultures. It's also what helps individuals grow through their own “mistakes that make us.”
And a quote I think is even more urgent today:
“Lean helps us stop blaming people for systemic errors and start fixing the systems that set them up to fail.”
This might be the quote I feel most strongly about today. Whether we're looking at sentinel events in hospitals or everyday miscommunications, the tendency to search for who is to blame instead of what went wrong is deeply ingrained–and dangerous. Lean thinking helps shift the focus to root causes and system design. In both Lean Hospitals and The Mistakes That Make Us, I've tried to show how this shift isn't just more effective–it's more human.
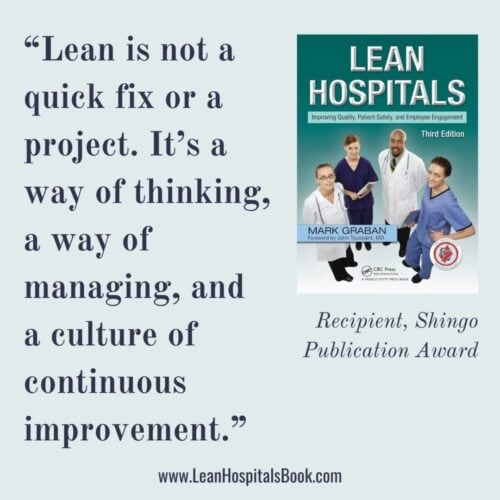

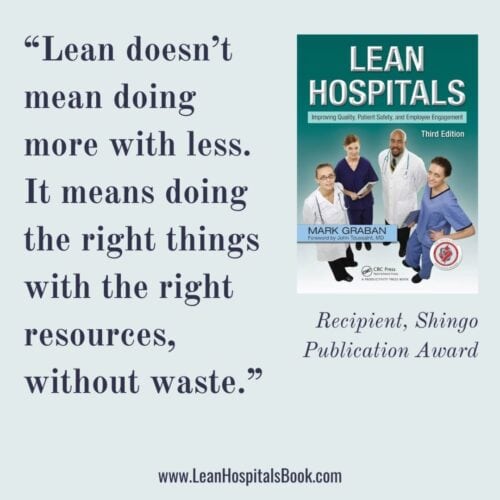
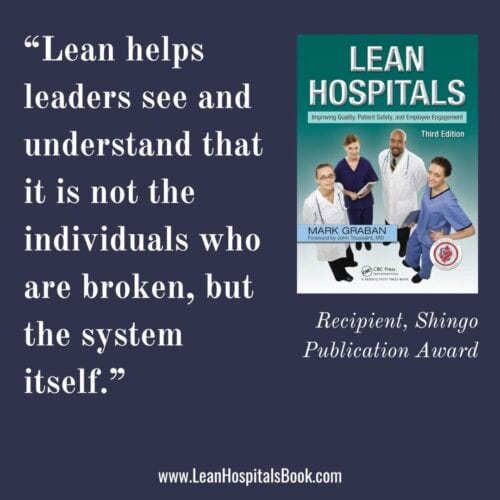
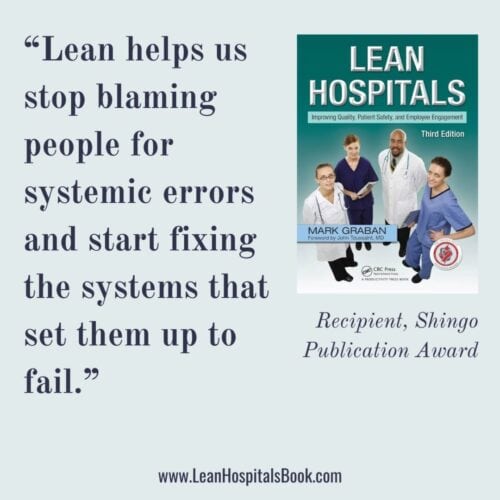
Seventeen years later, I'm still learning. Still refining how I think and teach these concepts. Still seeing the incredible impact that Lean–when applied thoughtfully and respectfully–can have in healthcare.
Thank you to everyone who has read, shared, critiqued, or taught from Lean Hospitals (now in its third edition and translated into eight languages). I'd love to hear what quote or concept from the book has stuck with you–or what lessons have helped you the most in your journey.
Let's keep learning and improving, together.
Please scroll down (or click) to post a comment. Connect with me on LinkedIn.
Let’s build a culture of continuous improvement and psychological safety—together. If you're a leader aiming for lasting change (not just more projects), I help organizations:
- Engage people at all levels in sustainable improvement
- Shift from fear of mistakes to learning from them
- Apply Lean thinking in practical, people-centered ways
Interested in coaching or a keynote talk? Let’s talk.
Join me for a Lean Healthcare Accelerator Trip to Japan! Learn More
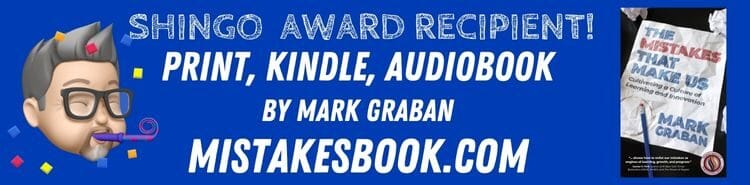
Hi Mark. Fantastic bibliography you’re creating, and all pointing, it seems, to the very human tendency to undervalue, and fail to utilize, the capabilities of each other. We’ve spoken at length about psychological safety in the workplace, but haven’t dealt too much with the lack of a strategy to see and know a teammate’s skills or capabilities. How we bridge that communication gap may open doors we haven’t knocked on yet.
Comments are closed.