Scroll down for how to subscribe, transcript, and more
My guest for Episode #527 of the Lean Blog Interviews Podcast is Dave Fitzpatrick, co-founder of Zenkai Improvement Partners and a 30-year resident of Japan. Dave brings a unique perspective as a Canadian Lean practitioner who has worked extensively in both manufacturing and healthcare, guiding international leaders on immersive study experiences throughout Japan.
In this episode, Dave and I share details about a new collaboration we're leading together–the Lean Healthcare Accelerator Experience. This is a jointly developed series of immersive visits to high-performing organizations in Japan, designed specifically for healthcare executives who want to see Lean principles in action across both hospitals and manufacturing settings. We talk about why we're creating this experience, what makes it unique, and how cultural context, leadership behaviors, and intentional long-term commitments drive sustainable improvement–not because it's “just Japan,” but because of the systems and mindsets these organizations have cultivated.
Dave shares his personal Lean journey, including how he transitioned from working in aeronautics to leading study tours for visiting professionals. He reflects on the differences between Japanese and Western companies when it comes to employee engagement, psychological safety, and respect for people. We also preview the first Accelerator trip taking place in June 2025 and discuss what makes these experiences so valuable and transformational for participants.
Whether you're in healthcare or another industry, this conversation is packed with insights about creating a culture of continuous improvement–and how a visit to Japan can accelerate your learning.
Questions, Notes, and Highlights:
- Can you share your origin story–how did you first get involved with Lean, Kaizen, or the Toyota Production System?
- What initially stood out to you when you began visiting Japanese manufacturing and healthcare organizations?
- From your experience, what cultural factors give Japanese organizations an advantage–or do they?
- How do successful Japanese companies build deep employee engagement and commitment to improvement?
- What lessons can visitors take home from Japan–and why is it not just about being “Japanese”?
- What are some common misconceptions people have before visiting Japan on these study experiences?
- How does hierarchy or seniority in Japanese companies affect psychological safety and speaking up?
- What kinds of organizations will we be visiting during the Lean Healthcare Accelerator?
- What role will Reiko Kano play in these visits, and how does her expertise go beyond translation?
- What's the value of including manufacturing visits in a healthcare-focused learning experience?
- How do Japanese companies view improvement work in relation to headcount and job security?
- Why is respect for people and time such a noticeable theme in Japanese customer service and operations?
- What do you hope participants in the Lean Healthcare Accelerator take away from this experience?
This podcast is part of the #LeanCommunicators network.
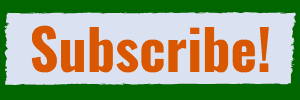
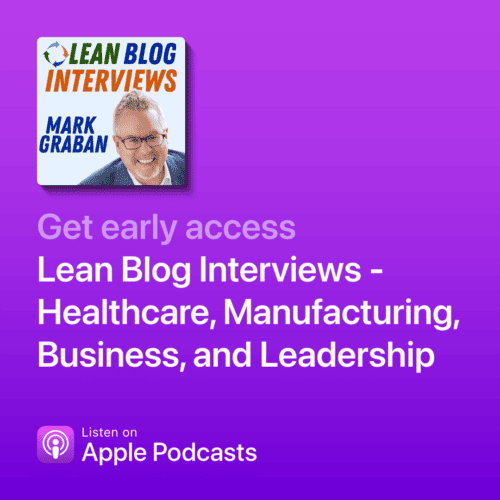
Full Video of the Episode:
Thanks for listening or watching!
This podcast is part of the Lean Communicators network — check it out!

Episode Summary
Learning Lean from the Source: Dave Fitzpatrick on the Lean Healthcare Accelerator Experience
In Episode #527 of Lean Blog Interviews, Mark Graban talks with Dave Fitzpatrick, co-founder of Zenkai Improvement Partners and a 30-year resident of Japan. Together, Mark and Dave are launching a new initiative–the Lean Healthcare Accelerator Experience–a series of immersive, executive-level visits to high-performing healthcare and manufacturing organizations in Japan.
These experiences are specifically designed for healthcare leaders who want to see how Lean principles are embedded in the daily management systems of real-world organizations. As Mark and Dave emphasize in the episode, this is not about copying tools or mimicking Japanese culture–it's about seeing what's possible when organizations commit deeply to respect for people, continuous improvement, and long-term thinking.
Why Go to Japan to Learn Lean?
Dave shares how his Lean journey began unexpectedly–while working in an aeronautics training program at a local university in Japan. Over time, his language skills and curiosity opened doors to work in the automotive sector and eventually into Lean consulting. For the past 15 years, he's led learning experiences for professionals from around the world, helping them gain firsthand insights into Japanese organizational practices.
What struck Dave early on–and what he continues to emphasize in his work–is that successful Lean implementation isn't about being Japanese. “The key takeaway,” he says, “is not ‘we can do this because we're Japanese.' It's ‘we made the decision and committed to it.'” In other words, Lean is not a cultural artifact; it's a leadership choice.
What Participants Can Expect
The Lean Healthcare Accelerator is more than a study tour. It's a structured, high-engagement experience co-designed by Mark, Dave, and fellow Zenkai co-founder Reiko Kano–who brings deep Lean implementation expertise and the ability to interpret not just language, but Lean intent.
The June 2025 trip will include visits to three hospitals, a medical device manufacturer, a pharmaceutical company, and a special seminar led by a former head of quality at Toyota. But the learning doesn't stop at the Gemba. As Dave notes, “Some of the richest conversations happen between site visits–on the bus, over dinner–where people synthesize what they've seen and how it might apply back home.”
Culture, Leadership, and Respect for People
One of the episode's key themes is how Japanese companies consistently embed respect into their operations–not only for employees, but for customers and time itself. From punctual trains to service workers jogging to minimize customer wait times, Mark and Dave explore how cultural expectations reinforce operational discipline.
Still, they caution against over-romanticizing Japan. “Not all companies here get it right,” Dave says. “But the ones that do–like Toyota–focus on developing people, not reducing headcount. Improvement here isn't feared. It's valued.”
This mindset shift is crucial for Western organizations, where improvement initiatives are too often linked to layoffs or short-term cost cutting. Instead, the Japanese examples showcase what's possible when continuous improvement is tied to learning, engagement, and long-term value creation.
A New Kind of Learning Experience
For both seasoned Lean practitioners and newcomers, the Lean Healthcare Accelerator offers a rare chance to see high-functioning systems up close–and to learn how the principles of Lean transcend industry, geography, and culture.
As Mark puts it, “Lean methods and mindsets are transferable. What matters most is intentionality–creating systems and leadership behaviors that support learning and improvement at every level.”
Automated Transcript (Not Guaranteed to be Defect Free)
Mark Graban:
Hi, welcome to Lean Blog Interviews. I'm your host, Mark Graban. I'm really excited today to be talking with Dave Fitzpatrick. He's a co-founder of Zenkai Improvement Partners. We've talked a number of times over the past couple of years, and I'm excited to share that Dave and I are collaborating on a new initiative: the Lean Healthcare Accelerator Experiences.
These are immersive visits to Japan focused on Lean in healthcare. They're designed for healthcare executives who want to visit some of the best organizations in both healthcare and manufacturing. Our first trip will take place the week of June 23rd, and we're also planning one in late October. We're hoping this becomes an ongoing series of experiences.
If you'd like to learn more, look for a link in the show notes or visit japanleantrip.com. We'd love to talk with you. But for now, let me welcome Dave to the podcast. How are you?
Dave Fitzpatrick: I'm doing great, Mark. Thanks for having me here. It's a pleasure to be on and to chat with you about something I'm really excited about–these Lean experiences in Japan.
Mark Graban: And you're joining us from Japan, where you've lived for how long now?
Dave Fitzpatrick: Just over 30 years, Mark. I came here expecting to stay for a year, and here I am three decades later.
Mark Graban: Canadian by birth, right? I think I still hear a bit of that accent.
Dave Fitzpatrick: Yeah, you can take the boy out of Canada, but you can't take the Canadian out of the boy. I'm from Prince Edward Island, so it's hard to shake.
Mark Graban: Not a problem at all. So, as we usually do here on the podcast, I'd like to ask you your origin story with Lean, Kaizen, or the Toyota Production System. How did you get started?
Dave Fitzpatrick: It's not the most exciting story, to be honest. Years ago, I was working in an aeronautics department at a local university–not my background, but I was helping train people for aircraft maintenance engineer exams. That led to connections in engineering, then automotive, and eventually an opportunity to support a Lean project. That opened more doors.
Early on, I really applied myself to learning the language and cultural aspects of Japan. I wouldn't say I mastered it, but I developed a strong grasp that helped a lot. About 14 or 15 years ago, a local consulting company invited me to lead Lean initiatives and facilitate study tours. Back then, they were called tours–now we see them more as immersive experiences. That's how I got to where I am today.
Mark Graban: And this has become a really important focus for you–helping people from outside Japan learn from what Japanese organizations are doing. What stood out to you most when you started leading these visits?
Dave Fitzpatrick: All my experience learning what manufacturing is and how it's driven came from Japan. Working with people in Canada now, especially in manufacturing, I've noticed differences. In Japan, there's a culture of full team engagement that many North American companies struggle with.
People often ask, “How do we make this stick? How do we get roots to grow?” And my answer is, let's go visit companies that have figured it out. The key insight? It's not, “We can do this because we're Japanese.” It's, “We made the decision and committed to it.”
That's what surprises people. They go home realizing, “We can do this, too.”
Mark Graban: That was a big takeaway for me as well when I first visited in 2012. People in the U.S. often say, “Lean would be easy if we were Japanese.” But that's an unfair and inaccurate statement.
It doesn't give enough credit to the intentional culture companies like Toyota create. They work hard to engage people and create an environment where it's safe to speak up. That's not automatic–it's designed.
In some Japanese hospitals I've visited, they've been doing TQM-style quality circle projects consistently for 25+ years. But even they realize one or two projects a year isn't enough. They expand to kaizen-style improvement for more ongoing engagement.
What are your thoughts on how hierarchy and seniority in Japanese organizations affect psychological safety?
Dave Fitzpatrick: That's a great question. Not all Japanese companies do this well. In some, the hierarchy stifles autonomy and engagement. Those companies struggle with retention.
But others–Toyota being a prime example–foster skill development and give people the chance to show what they can do. Managers invest in discovering people's aptitudes and finding the right roles for them. There's a deep respect for people.
Importantly, improvement here is never tied to headcount reduction. It's about finding new value, and bonuses are often tied to that value creation. There's no fear behind improvement, and that's a big cultural difference.
Mark Graban: Right, in the U.S., improvement is often tied to cost cutting or layoffs, which creates fear and disengagement. That completely misses the point.
Another theme I've noticed is respect for time–something you see in daily life and operations. What are your thoughts on that?
Dave Fitzpatrick: Absolutely. I'm a punctual person, and Japan is a great fit for that. People show up early. Trains and buses are on time. That respect for others' time shows up everywhere–in customer service, in how companies deliver on promises.
In supply chains, especially for automotive companies like Toyota or Honda, there's 100% compliance with delivery commitments. The systems and standard work behind that are impressive.
Mark Graban: Even in hospitality–checking into a hotel, you'll see staff jog to make a photocopy of your passport. Not because the guest is in a rush, but out of respect not to waste your time.
Dave Fitzpatrick: Exactly. Have you ever rented a car here and gone to a gas station?
Mark Graban: No, I haven't.
Dave Fitzpatrick: When you do, you'll see attendants bowing and even stopping traffic to help customers exit quickly. It's that pit stop mindset–get the customer back on the road. It's not just about efficiency, it's about respect.
Mark Graban: That ties into one of the goals of these Lean Healthcare Accelerator experiences–to give people a deeper understanding of these cultural and operational nuances. Whether someone has visited Japan before or not, there's always more to learn.
Dave Fitzpatrick: Yes, and now is a great time to come. The World Expo is in Osaka, so if you can come a few days early or stay after, it's worth it.
Mark Graban: Absolutely. Let's also talk a bit about what's planned for the June Accelerator. We'll visit three hospitals, a medical device manufacturer, a pharmaceutical company, and more.
Dave Fitzpatrick: Right–and we'll also have a quality seminar with the former head of quality at Toyota. That's going to be a real highlight.
Mark Graban: And I'm excited that Reiko Kano, your co-founder at Zenkai, will be part of the experience. I met her on my first Japan trip in 2012. She's more than a translator–she interprets Lean content, ensuring accurate understanding across cultures.
Dave Fitzpatrick: She's truly unique. Her depth of experience adds huge value. Plus, it's the learning between visits–on the bus, at dinner–where the real richness comes out.
Mark Graban: Exactly. My role is to help connect the dots, especially for those in healthcare. I speak the language of hospitals and factories, even if I don't speak Japanese.
Dave Fitzpatrick: And it's so valuable to see how these principles apply across industries. Lean is not just for factories or hospitals–it's universal. The common theme is focusing on what customers expect from us.
Mark Graban: That's a perfect note to end on. Thanks again for joining us, Dave. I'm looking forward to the experiences we'll be leading together.
Dave Fitzpatrick: Thank you, Mark. I'm excited too. Looking forward to it!
Please scroll down (or click) to post a comment. Connect with me on LinkedIn.
Let’s build a culture of continuous improvement and psychological safety—together. If you're a leader aiming for lasting change (not just more projects), I help organizations:
- Engage people at all levels in sustainable improvement
- Shift from fear of mistakes to learning from them
- Apply Lean thinking in practical, people-centered ways
Interested in coaching or a keynote talk? Let’s talk.
Join me for a Lean Healthcare Accelerator Trip to Japan! Learn More
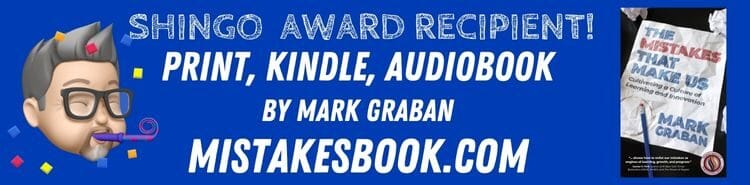