tl;dr: In this post, Mark argues against the conventional punitive approach to mistakes in organizations, advocating for a culture that prioritizes learning and improvement. Using case studies and real-world examples, he outlines how such a shift in perspective can lead to better outcomes, higher employee engagement, and continuous improvement.
I saw a LinkedIn comment from a former manager of mine — the director I reported to when I worked at Honeywell almost 20 years ago. Mike Santarelli was a great guy to work for, an earnest and experienced Lean practitioner who cared about and looked out for his team. He had come to Honeywell from a Danaher company, which was a great place for people learn and practice Lean (and likely still is).
Mike commented on an insightful post by David Marquet, a former U.S. Navy nuclear submarine commander and author of the fantastic book Turn the Ship Around!
The “deciders” are the ones who design a factory, the supply chain, the staffing levels, and the organizational chart. The deciders choose the leaders to hire and promote. The deciders greatly influence the culture.
The doers get “held accountable” by the deciders in a way that mainly serves to deflect attention from the “leaders,” as I posted last week:
Mike told a story in a comment to Marquet's post:
“Years ago, there was an operator fired for grabbing and then using a bottle of the wrong chemical. This created scrap and the Plant Manager flew into a rage.
The jug they picked was identical to the correct one, stored next to the correct one, made and packaged by the same manufacturer, and 95% the same label. When I made the case for the operator, that the system had set her up to fail, I was publicly chastised.
To the poster's point, the decision to store the chemicals in this way was the true error. I'd like to add that if you assume people are programmed to make errors, and stop looking for fault, you will find great improvement possibilities.”
This happens so often in healthcare, where the wrong medication with an almost completely identical label gets used — and the patient is harmed or killed. The “doer” — the person giving the medication — gets blamed and punished more often than the “decider” who chose the medication vendor or allowed the mistake-prone packaging design to exist.
Mistakes with the wrong chemical happen a lot in manufacturing — including at Toyota. As I replied to Mike:
“Thanks for sharing that story. How unfortunate. Firing people doesn't prevent the mistake from being repeated.
I was able to share some Toyota stories in my book, The Mistakes That Make Us: Cultivating a Culture of Learning and Innovation. One from 1960s Japan and one from 1980s Kentucky, where leaders in both cases made clear that the “wrong chemical” mistakes (one in a paint shop, one in a molding area) were systemic in nature. They chose learning and improvement over punishment — and they're better off for it.”
You can hear those stories directly from the source in these two episodes of the “My Favorite Mistake” podcast:
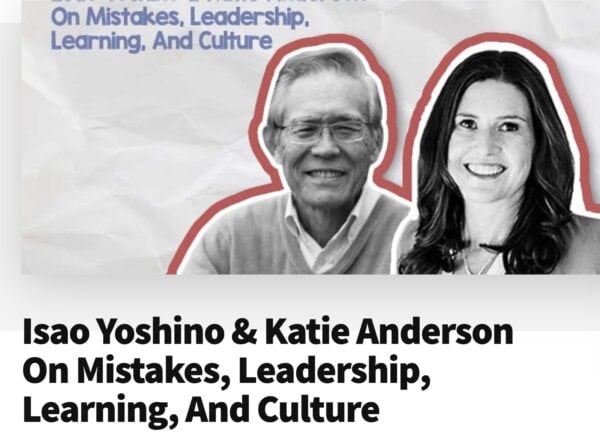
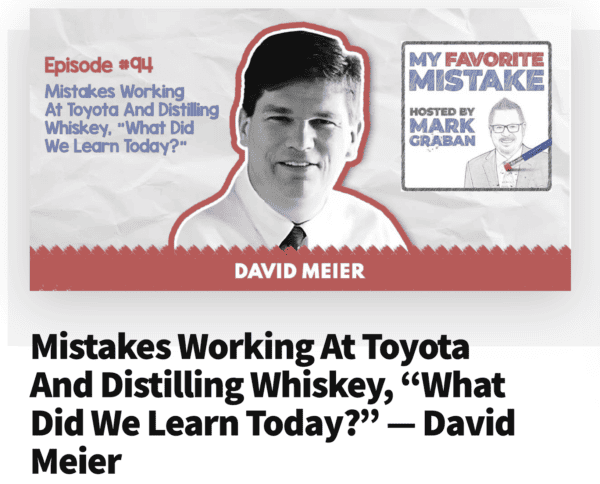
Here is part of Yoshino's story, as told in my book:
“When Yoshino joined Toyota fresh out of university in 1966, his four-month orientation included multiple weeks in a factory's paint shop. Part of Yoshino's job was to add paint and solvent to a machine that mixed them and feed the paint sprayers every two to three hours.
During his first week, assembly workers saw a major problem. The paint wasn't sticking properly to vehicle body panels, meaning at least 100 cars had to be repainted. Yoshino learned this when a group entered the paint shop, shouting about the problem. He remembers feeling sick and thinking, “I must have done something wrong.“ Yoshino's managers asked him to show them the process by which he poured the cans into the tank.
They discovered that Yoshino had poured an incorrect solvent into the tank. As a young employee, he was surprised by the way the organization responded. It was immediately obvious that the cans looked identical, and it was easy to mix them up. The correct solvent didn't have a defined storage location. It was a systemic problem.
Beyond not blaming Yoshino for the mistake, his managers thanked him for making it, explaining that the problem was management's mistake for not setting up a newcomer to be successful.
They would work together to improve the process immediately so that Yoshino (and other employees) couldn't add the wrong solvent.
Yoshino recalls talking to other new employees in the orientation program, who worked in a different department. They had all made similar mistakes and encountered the same non-blaming problem-solving reaction. That points to a consistent culture.
Yoshino said, “You cannot get anything out of blaming somebody,”
a management lesson that became the foundation for the leader he wanted to become.”
The deciders apologized to the doers. The deciders took responsibility.
The same thing happened with Meier's story — half a world away and two decades later.
“Toyota also noticed that the drum containing the wrong material was the same color and size as the one they normally used, containing the catalyst. Knowing that human inspection (visually verifying the chemical) would never be 100% reliable (because we are all human and make mistakes), Toyota asked the manufacturer to change the color of the correct chemical's drum, so that it was different from the one that was mistakenly used–an example of mistake-proofing.”
…
As with Yoshino's story, leaders focused on learning and improving their processes. David didn't feel blamed for either of the mistakes related to the chemical or the problem-solving. He remembers how TMMK president Fujio Cho, who later became Toyota's chairman, always asked,
“What did we learn today?”
as he did the day of David's story.
What did we learn today? Hopefully, this blog post helps you realize that punishment is not necessary when mistakes and “human error” occur.
Once a mistake has happened, it's happened.
If the reaction is punishment, that just teaches people that they need to get better at hiding mistakes. That's especially true when people unfairly get blamed for mistakes that are caused by systemic factors. The system is the deciders' responsibility.
Toyota seems to have been more successful because of its approach to mistakes, not despite it. Companies that punish mistakes instead of addressing systemic will end up repeating those mistakes, as I blogged about here:
Please scroll down (or click) to post a comment. Connect with me on LinkedIn.
Let’s work together to build a culture of continuous improvement and psychological safety. If you're a leader looking to create lasting change—not just projects—I help organizations:
- Engage people at all levels in sustainable improvement
- Shift from fear of mistakes to learning from them
- Apply Lean thinking in practical, people-centered ways
Interested in coaching or a keynote talk? Let’s start a conversation.
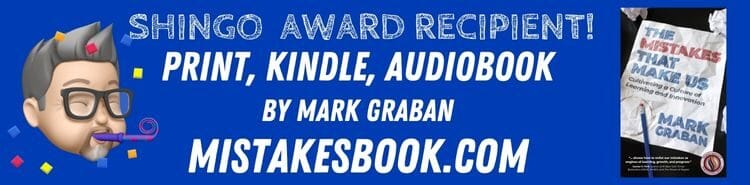