Thanks as always to Ryan McCormack for this… there's always so much good reading, listening, and viewing shared here by him! Subscribe to get these directly from Ryan via email.
Insights about improvement, innovation, and leadership…
Operational Excellence, Improvement, and Innovation
Improvement is not an event
Many organizations reduce their improvement or innovation efforts to a series of splashy 3 or 5-day events or workshops. Don't get me wrong, a well-executed kaizen event is a great accelerator of improvement and learning. But improving is as much about an event as getting healthy is about a few days of working out. Seth Godin reminds us that there is a big difference between an event and a journey. Don't let the theatre of events and vanity metrics distract you from your journey and long-term goals. The results and fanfare of events are fleeting – build improvement as a system not a collection of events.
Great design is a team sport
The design of the workplace has significant effects on the customer experience, the employee experience, outcomes, performance, and organizational culture. Superior design is achieved with input from, collaboration, and experimentation from all relevant stakeholders – not just engineers and architects. The Ottawa Hospital is developing a new 641-bed campus and is including patients and family members, doctors, nurses, and infection control specialists in the design of patient rooms, discovering some important design considerations that they may have otherwise missed without high degrees of collaboration.
Collaborative design has long been part of the continuous improvement and innovation tradition. One of the most powerful, but often underutilized improvement methods in the traditional lean toolkit is the Production, Preparation, Process method or 3P, which is practiced in the design phase of products or processes (Check out Gemba Academy for a primer on 3P). 3P was imported by many North American manufacturers in the 1980s and 1990s along with other kaizen methods and principles. Around the same time, the construction industry more widely embraced collaborative design methods such as Integrated Design Process (IDP) and lean construction. In the 2000s and 2010s, lean healthcare pioneers at Virginia Mason leveraged 3P to develop better standards for patient rooms and the “on stage / off stage” clinic design while hospitals in the UK used 3P to reduce costly assumptions in hospital design.
In the 2020s, we are witnessing rapid advancements in technology that enable collaborative design processes. Traditional 3P and IDP methods rely on clunky analog 3-D mock-ups to test ideas, limiting the possible speed and number of iterations. Advancements in rapid prototyping and AI technology-led generative design make it easier and faster to simulate designs, allowing for many more iterations and even more engagement from participants. Physical mock-ups may already be becoming a thing of the past as the acceleration of digital twins threatens to make the physical prototype obsolete. The tools and technology to collaborate and experiment with design continue to improve.
No respect
There's a lot of talk about principles in contemporary organizational management circles (see the success of the book Principles by Ray Dalio). There's no shortage of frameworks that contain improvement principles, including many versions of principles and pillars of Toyota's vaunted production system. Regardless of the (ironic) variation in descriptions of Toyota principles, they all contain a version of Respect for People – yet there is not a lot written about it. Why? David Rizzardo argues that Respect for People is overlooked due to its “soft-skills” connotation and repositions it as a set of five interrelated employee rights in The Lean Principle That Deserves More Respect.
Creating a Culture of Improvement
It's (still) the systems
We are wired to attribute problems to individuals. Blame the person for the error. Tell the stressed-out employee to toughen up. Hold them accountable. But these individual interventions are unhelpful and ineffective when the underlying cause is chronic and systemic. It's more effective to improve your systems rather than try to fix your people.Â
Not only is blaming individuals for systemic causes ineffective, but it also impedes learning and quality. Organizations and leaders should embrace mistakes to build a learning culture.
We can't simply incent, train, or tell our way to a culture of safety and improvement, nor can we consistently rely on the goodwill of individual performers to achieve the best results. For example, in healthcare settings, where quality can be a matter of life and death, there is clear evidence that psychological safety, employee well-being, and sufficient time to improve are preconditions to the success of any safety or quality endeavours. Ask yourself whether you've done the work to create these conditions before putting up the poster, holding the seminar, or reminding your teams to deliver quality.
I'm the type of leader who likes to roam around
Tom Peters has long championed Management By Wandering Around (MBWA) as a practice that enables excellence through random walks around the workplace. Tim McMahon argues the true benefits of getting out on the floor don't come simply from flying by but rather from intentional listening and learning in Management By Wandering Around Isn't A Thing. They both agree whether you're wandering or intentionally learning: get out there and go to the source
“I'm fine”
Managers: your high performers may not be fine. Support your high performers by asking this question twice.Â
Re-organization
We spend a lot of time in organizations as students, customers, or employees. What's the best way to structure an organization? Legendary management professor Henry Mintzberg is back with a new book Understanding Organizations…Finally: Structure in Sevens is to be released in February. I pre-ordered my copy.
Coaching – Developing Self & Others
“The problem's not the problem. It's how you think about the problem”
Solving the toughest problems usually requires different perspectives. Our minds are conditioned to use “either/or” thinking when evaluating options, but it's useful to define the dilemma and expand the options to include “both/and” conditions. Check out Coaching for Leaders: How to Solve the Toughest Problems with Wendy Smith.
So tired of change
It's exhausting when every day is completely different. Our brains rely on routines and patterns to preserve cognitive capacity, but when everything is always changing, our brains are overloaded. How to Manage Change Fatigue.Â
You don't need to be a manager to lead
It's fashionable to say that everyone can be a leader or that title does not dictate behaviour. But how do people recognize your leadership capabilities when you are an individual contributor? Here are 9 Ways to Demonstrate That You're a Leader When You're an Individual Contributor. Similarly, we often associate levels of influence with title and positional power, but don't underestimate your influence at work.
Follow Ryan & Subscribe:
LinkedIn:Â https://www.linkedin.com/in/rjmccormack/
Subscribe to receive these via email
Please scroll down (or click) to post a comment. Connect with me on LinkedIn.
Let’s work together to build a culture of continuous improvement and psychological safety. If you're a leader looking to create lasting change—not just projects—I help organizations:
- Engage people at all levels in sustainable improvement
- Shift from fear of mistakes to learning from them
- Apply Lean thinking in practical, people-centered ways
Interested in coaching or a keynote talk? Let’s start a conversation.
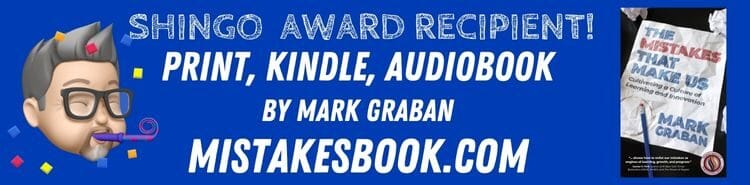