Our last KaiNexus webinar took a deep dive into problem solving — you can check out the recording on the KaiNexus website or through YouTube.
The next webinar, being held on June 5, will take a step back to look at things from a Continuous Improvement leader's perspective. That leader is Chris Burnham, a Continuous Improvement Program Manager at Wright Medical, in Memphis.
His webinar is titled:
Solutions for Sustaining an Improvement Program
Below is our podcast episode where we chat about his background and his webinar. A transcript will be added soon.
Chris is a podcasting pro, as he was the creator of The Lean Leadership Podcast, which is still available online even though he has stopped creating new episodes.
Click here to register for the webinar.
Book Giveaway! Measures of Success
As part of my ongoing partnership with KaiNexus, I'm happy that we are joining up to give away three paperback copies of my book Measures of Success: React Less, Lead Better, Improve More.
KaiNexus is the only cloud-based SaaS platform that supports continuous improvement in Lean organizations.
Entering this contest will subscribe you to occasional email updates about this book and KaiNexus. You can unsubscribe at any time.
Click here to enter — the contest ends this Friday, May 24.
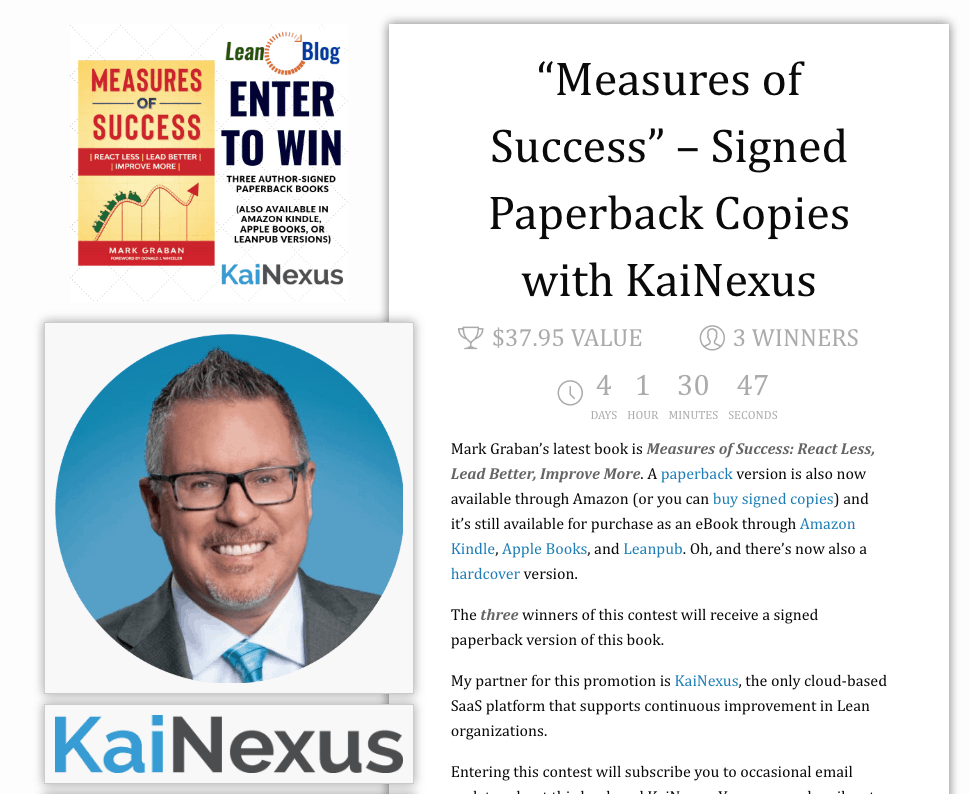
Podcast Transcript
[music]
Mark Graban: Hi, this is Mark Graban from KaiNexus. Today we are doing a preview of our next webinar. It's going to be presented on Wednesday, June 5th, by Chris Burnham. The title is Solutions for Sustaining an Improvement Program.
To register for that, you can go to www.kainexus.com/webinars. You can register. You can sign up to get email notifications about future webinars. We're really looking forward to this one.
We've got Chris Burnham with us today to give a bit of a preview. Chris, how are you?
Chris Burnham: I'm very well, Mark. How are you today?
Mark: I'm doing great. Thanks again for doing the webinar. To just help tee things up, in your own words, if you could introduce yourself to the listeners.
Chris: My name is Chris Burnham. I have around 17 years of continuous improvement experience. In that experience, I've worked in a variety of industries, both private companies, large public companies. There's one common theme that seems to be at each of my stops in my career.
That's learning how just not to do the continuous improvement work that we practice every day, but also looking to simplify the different roles that we have to play as continuous improvement leaders, the different people that we have to interact with and understand what their needs are to able to serve the people that we try to serve.
There's also some common pitfalls, the mistakes that frustrate improvement leaders. I've had them in my own organization with people that I've coached with. I've suffered through them myself.
I'm hoping to give listeners the benefit of my experience, of some of my successes, and also some of my failures in this endeavor to be able to be a very effective leader doing continuous improvement work.
Mark: We'll delve into that a little bit more. Can you tell listeners a little bit about your background in terms of education and what types of industries that you've worked in?
Chris: Absolutely. I have my undergraduate degree in criminal justice from Western Carolina University. People always ask me, “Why do you have a law enforcement degree and you do this?” I use those skills that I learned there every day now in my current job.
Gather your own data and facts, learn to deal and to converse and to interact with people at lots of different levels within the organization and lots of different walks of life. Always have a predisposition to not accepting things as the way that you first receive them and really delving into those.
From there, I've worked in manufacturing. I've worked in food and beverage. I've worked in warehouse fulfillment. Now I work for a large medical device company.
Mark: That is a really unique career path. I think I've probably used this idea at a KaiNexus user conference. When I give talks about Lean leadership, I sometimes try to use the analogy of shifting from cop to coach.
Instead of a leader policing procedures and looking to write people up, if you will, to be more of a coach and try to help identify barriers and helping people instead of just writing a ticket. Am I just torturing that analogy?
Chris: No, not at all. One of my favorite books is “Radical Candor” by Kim Scott. In that book she talks about if you don't do the work of generating a relationship with the people that you work with, where they feel like you care personally on a very high level, it makes it very difficult for you to challenge directly on the process.
That just rings true with me because it goes back to what people said in the past. If people don't think that you care about them, they really don't care what you know about them.
You have to be very succinct in how you approach working through that, so that you can separate the work from the worker and be able to coach them and you get their buy-in for the improvement in the next step.
Mark: Good, I'm glad that analogy doesn't cause any heartburn. I didn't think it would. I think it's a different aspect of first-responders. I have a friend of mine from high school who's a firefighter and an EMT in Nevada.
We've talked before and chatted about how it's unfair when we talk about organizations “firefighting.” Firefighters aren't just running around putting out the same fire every day.
They're working with the community to be a coach to help prevent fires through education. I think we can do that with Lean.
Chris: Mark, I had a mentor of mine that once told me in organizations where it seems like you are in a perpetual firefighting mode, usually your best firefighters are also your worst arsonists.
They're the ones that are setting the fires that they go put out and then they say, “Hey, look at me. I saved us. I put out this fire.” So that analogy rings true as well.
Mark: Bringing things back to the webinar, again, this is going to be presented by Chris on June 5th. The title is Solutions for Sustaining an Improvement Program.
Maybe the last thing we can cover here, Chris, obviously you're going to talk about challenges that you've seen. You're also going to talk about some countermeasures, right?
Chris: Absolutely. There are some simple countermeasures that really change the way that you think a little bit about how you approach improvement and change the way that you think about how you interact with the people that you work with.
One of the things similar to this — as you were talking about going from cop to coach — if all you seek is compliance, compliance is all you will ever get.
What we're really trying to do from an improvement standpoint is unlock innovation and unlock experimentation, and thinking, and challenging the status quo.
That's one of the pitfalls that folks can fall into because compliance is a natural defensive method. If you feel like if you get everybody to comply then problems won't creep in, well, not necessarily. You're definitely not going to be able to find the adjacent possible with the next step that you take.
Mark: I've said this before in talks kind of building on that cop-to-coach idea. I don't think the pathway to world-class organizations — whether it's through the Shingo framework, or others, or we need more highly-compliant organizations — that's a path to mediocrity, right?
Chris: To be clear, in regulated industries compliance is very important. It's there for a reason. There's lots of other places within process improvement where if you're just getting somebody to follow a rule and not really challenge why that rule exists, or why it's there, then you're not really doing innovation work. You're not really doing improvement work.
Mark: That's a better way of putting it. Compliance can be important but it might also not be enough.
Chris: Absolutely.
Mark: There's going to be a lot of great insights that you're going to share in the webinar, I'm sure. For the listeners, Chris has experience in a lot of different settings. He's got a lot of great stories. I've always enjoyed talking to Chris, so I'm looking forward to the webinar.
Again, Wednesday, June 5th. Chris, I'll give you the last word. Is there anything else you'd like to share with the listeners here?
Chris: I'm grateful for the opportunity. I think the great thing about continuous improvement is that sense of community and that sense of camaraderie that we develop because it's a unique thing that we do.
I'm really grateful for KaiNexus giving me the opportunity to share with the community.
Mark: We're grateful that you're going to be able to do that. Again, our guest today and our presenter for June 5th, Chris Burnham. Chris, we'll talk to you soon.
Chris: Thanks, Mark.
Please scroll down (or click) to post a comment. Connect with me on LinkedIn.
Let’s work together to build a culture of continuous improvement and psychological safety. If you're a leader looking to create lasting change—not just projects—I help organizations:
- Engage people at all levels in sustainable improvement
- Shift from fear of mistakes to learning from them
- Apply Lean thinking in practical, people-centered ways
Interested in coaching or a keynote talk? Let’s start a conversation.
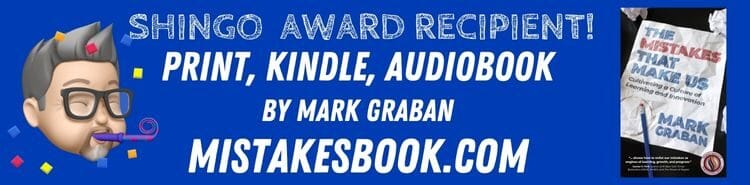