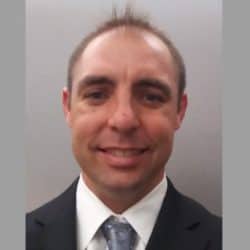
It's incredibly sad that we've lost a friend and a thoughtful, inquisitive member of the “Lean community,” Samuel Selay, when he passed away at age 34 in a kayaking accident.
Here is Sam's obituary.
This is a GoFundMe page that was set up by Sam's sister-in-law to provide financial support to the family — his wife and four children under 18. I've donated and I hope you might consider doing the same.
Another way you can help, as posted in a comment by a family friend:
“…a MealTrain has been started to assist Brittney and the kids with meals and donations while the search for Sam continues. If you wish to make a donation, you may do so here: https://mealtrain.com/glzvye“
Sam and I weren't close friends by any means. We had never met in person. But, we've talked on a phone a few times and have exchanged many emails on topics related to Lean and improvement, including his desire to find a job as a way to help improve healthcare, as he blogged about recently.
A Lean Healthcare Job Interview Process: Thoughts and Reflections
In my experience with Sam, he was a very thoughtful and philosophical guy. As a Marine, he always seemed very interested in serving others, which I appreciate and admire.
He recently wrote about Lean and Stoicism on LinkedIn. one of the 74 articles he has published there:
We shared some conversations about our shared interest in “Motivational Interviewing” – a methodology that I introduced him to. He dove right in and read one, if not two, books on the subject. We talked about doing some mutual coaching with each other to practice this approach (and to try to help each other), but we didn't get to it…
I got to know Sam as he was a contributor to our collaborative anthology eBook Practicing Lean.
To honor Sam, I'll share his entire chapter below (or you can download a PDF via Dropbox):
Chapter Nine – Samuel Selay
Bio: Samuel Selay is the Continuous Improvement Manager within his organization in the Marine Corps at Camp Pendleton. He has worked in the field of supply chain and logistics for the past 12 years. For the last six years, he has managed his organization's Continuous Process Improvement/Lean Six Sigma (LSS) Program. During this timeframe, he has facilitated/mentored 28 completed LSS projects or kaizen events. Additionally, he mapped and standardized 36 processes, conducted 90 process audits, and implemented his organization's Quality Management System, resulting in a 20% reduction in shipping defects.
Along with project leadership, he has instructed and certified 481 employees as LSS Yellow Belts and 121 employees as LSS Green Belts. He is a certified Lean Six Sigma Black Belt from the University of San Diego, a certified Logistics Technician (CLT) from the Manufacturing Skills Standards Council, and a certified ISO 9001:2008 Internal Auditor from the World Wide Quality Network. He holds a BS in Management Studies from the University of Maryland University College and an MBA in Management and Strategy from Western Governors University.
Learning Continuous Improvement: Reflections on Practicing CI in the Marine Corps
Over the last six years, I have had the great privilege and opportunity to learn and practice continuous improvement within the Marine Corps. The Marine Corps has an umbrella approach called Continuous Process Improvement, which encompasses the methodologies of Lean, Six Sigma, and Theory of Constraints. As I transition into the private sector, I have been reflecting on the valuable lessons I learned and would like to share them as a way to give back, just as my mentors taught me to pay it forward.
Cultural Roadblocks to Deploying Continuous Improvement
The road to pursuing excellence in continuous improvement within the Marine Corps has not been easy, and I had to unlearn some behaviors that were counter to what I now understand true continuous improvement to be.
The Marine Corps is, by design, a command-and-control, top-down structured organization. The resulting culture has posed challenges for continuous improvement professionals like myself. For example, in improvement teams, lower-ranking individuals are timid because they are not accustomed to voicing the true current condition, out of fear of retribution. The same is true in the classroom setting when talking about problems that hinder operational excellence.
A countermeasure I put in place was a set of Rapid Improvement Event / Project team meeting rules. These include:
1. Everyone on the team speaks professionally and with an equal voice
2. Respect all ideas and ideas, once verbalized, become the property of the team and not the individual
3. Check your rank at the door (in order for everyone to have an equal voice)
In addition, the one rule I establish before coaching a team is that I will not allow the sponsor to suggest “solutions.” I have to be very tactful when having this talk with the sponsor who is usually a senior leader and who is used to making all the big decisions.
The reason for this rule is that it's disrespectful to tell an improvement team what to do. If the senior leader has an idea and will not budge, I tell them there is apparently no need for a cross-functional team and that he or she has no need for the team to solve the problem because the sponsor has the “solution.”
This is a large organizational cultural change that must take place.
Also, senior leaders get too focused on results. Yes, continuous improvement will yield big results via problem solving, but there is another side to the coin that is equally important. The second reason for problem solving is to facilitate learning and build capabilities within the organization via the problem solving process.
Lessons Learned from Japan
I had the honor and privilege of working and living in Japan between 2005 and 2007. My time in Japan was long before I was ever exposed to continuous improvement, but there was something different about the culture of Japan compared to the United States.
Unfortunately, while practicing CI in the Marine Corps, I was never exposed to what “Respect for People” was. It was never taught in any of the training I went through. Even going through Black Belt training through the University of San Diego didn't introduce me to what respect for people meant.
It wasn't until I disciplined myself to a journey of self-learning through reading, listening to podcasts, watching webinars, reading blogs, and applying as much as I can, that I learned what respect for people was.
Now, I have a good grasp on the concept of respect for people based on the last two years of dedicated learning. Now, I can understand what the difference was between the culture of Japan and the United States.
First, “respect for humanity” is a better translation that more clearly represents what I was exposed to for nearly two years in Japan.
Some key takeaways I can still remember are:
- An attitude that reflects a sense of pride, admiration, and esteem for others.
- Pride in the community and country. I was taught not to spit, throw trash, or litter. When going to restaurants or certain homes, you were expected to take off your shoes. If given chopsticks, you were expected to use them.
- Demeanor of joy and happiness in the workplace. While in Japan I went on several tours of factories and witnessed people on the front lines being delighted in their work.
What I have done based on these key takeaways are:
1. Create an environment which is conducive to sharing and implementing improvement ideas within all ranks of the organization. My CI team within the Marine Corps has created and implemented many great ideas based on Alan Robinson and Dean Schroeder books Ideas Are Free and The Idea-Driven Organization and Mark Graban's Lean Hospitals.
2. Make myself an equal to those who are of lesser rank when I feel it is hindering great ideas. I will put rank aside and talk person to person on a first name basis.
3. Go to the gemba, ask why work is being done the way it is, and show respect from a curiosity perspective. This allows for deep conversation about improvements.
4. Lead with respect by following a servant leadership model. The approach I take is “Follow me and we'll figure this out together.”
Practicing Continuous Improvement
When I first started practicing CI, I was a “tool head” and ended up wasting my time and my team's time by trying to use as many tools as possible. But, over time, I have learned the problem solving process, and I only develop, test, and apply countermeasures to address the root cause(s).
Next, I had to learn the hard way that being a doer, a belt, and a facilitator hindered the growth and development of the problem solving capabilities within my organization. For the last two to three years, I have been working on being a teacher, coach, and mentor. I have learned to lead with questions, and only teach when I know the other person doesn't understand the mechanics behind a tool.
Also, I also had to learn that my inability to stop and listen and ask Socratic questions hindered the output of the improvement teams I was facilitating. Additionally, I feel that I have only scratched the surface of knowledge in the field of CI. I subscribe to Malcolm Gladwell's view of 10,000 hours or 10 years to mastery. As I continue to learn and grow in the field, I find Albert Einstein to be 100 percent accurate in which he said, “The more I learn, the more I realize how much I don't know.”
Problem Solving Process
The Continuous Process Improvement journey for the majority of the USMC began in the spring of 2006. Secretary of the Navy Dr. Winter, with his industrial background, was the catalyst for transformation in the Department of the Navy using Lean Six Sigma. Given Lean Six Sigma was the approach, the scientific methodology that is utilized is Define-Measure-Analyze-Improve-Control (DMAIC).
Over the last six years, I have found people to get too wrapped up in the tools within DMAIC. Within the last year, a countermeasure I have taken and used within my organization is creating and implementing an eight-step problem solving process (very similar to the “Toyota Business Practice”), which works to help people think more holistically about problems. Additionally, the eight-step problem solving process helps people to think through DMAIC more cyclically versus the traditional linear model.
The eight steps are:
- Define and break down the problem
- Set a target condition
- Grasp the current condition
- Conduct root cause analysis
- Develop and test countermeasures
- Refine and finalize countermeasures
- Standardize best practices
- Measure process performance
I hope that everyone can take away something from my lessons learned.
As always, I appreciated Sam's thoughts and reflections… my thoughts and prayers go out to his family and friends…
Please scroll down (or click) to post a comment. Connect with me on LinkedIn.
Let’s work together to build a culture of continuous improvement and psychological safety. If you're a leader looking to create lasting change—not just projects—I help organizations:
- Engage people at all levels in sustainable improvement
- Shift from fear of mistakes to learning from them
- Apply Lean thinking in practical, people-centered ways
Interested in coaching or a keynote talk? Let’s start a conversation.
Sam’s wife is a friend of mine from high school, and I cannot thank you enough for your desire to raise awareness and show respect. I too am out of the area, but a MealTrain has been started to assist Brittney and the kids with meals and donations while the search for Sam continues. If you wish to make a donation, you may do so here: https://mealtrain.com/glzvye
Please keep Sam, Brittney, and the kids in your thoughts and prayers.
Mel – Thanks for sharing that link. I’ve made a contribution and I hope others will too.
Sam was also a guest on the Gemba Academy Podcast in 2016. I regret not having him as a guest on my podcast, as well…
https://blog.gembaacademy.com/2016/02/11/ga-097-how-to-apply-lean-to-the-military-with-samuel-selay/
Mark,
Thanks for posting this in honor of Sam. His passing is a great loss to so many people he touched throughout his time in the Marine Corps and in his LSS work. I served with Sam as I was retiring from the Marines and right before he exited as well. He was a great mentor to me even though i was his senior. I am in shock that this has happened. He will be surely missed!
RIP Sam, Semper Fidelis.
R,
Juan Contreras
From a news story:
That blog post:
https://www.linkedin.com/pulse/purpose-priorities-out-workplace-part-1-samuel-selay/
Hello,
I met Selay I believe in 2013 while in the Marines. He interviewed me for the lean six sigma team in the SMU during the improving pushes while deployments wind down. Selay and I worked together for two years. We PT together and for a long while we both car pooled. Selay and I did not have the best relationship. We argued a lot and I was always challenging him. There was even a few times during our carpool he would drop me off in random spots and let me know at the last minute.
However what I did not know is how much he actually taught me and how I owe him for my success. Selay pushed me in lead six sigma and most of our fights was over the importance’s of process improvement in the Marines. Because of him giving me the opportunity in the SMU, continuing to push and teach me I was able to transition out of the military and get into a large role using what I learned from him. I now work as a regional logistic manager for a bio pharma company.
Selay gave me what I needed to succeed and I never got to thank him. I was thinking of reaching out to him last year to talk to him about my black belt test and see how he was doing but I didn’t. I’ve donated anonymously to the go found me because I don’t believe I have the right to show my name because of our relationship. I hope he’s In heaven pushing saint Peter to improve his processes on letting people in. Rah
Scott – Thanks for your comment and for sharing your story about how Sam challenged and helped you…
Sam had a strong impact on a lot of people, even those of us (like me) who didn’t get to work with him as much as you did.
Mark
Sam Selay was a wonderful, Christian man. He lived his belief’s faithfully daily.
He is with our Lord, of this I am positive. “To be absent from the body makes you present with the bogu
IN MY 70 Years I don’t believe I have met a finer man, or family for that matter.
Our hearts go out to Brittney, Serenity, Jordan and Nolan. They also have their niece Journey which I am not sure they were able to complete their adoption but she is as much their child as the others born to them. She was only 8 when they gave her a home and all the love their family had.
Sam will be missed by many of us but not nearly as much as their hearts are aching for him. He was truly a unique young man with so much to give. I pray the earth family is always surrounded by their many loving friends and the Love of Jesus
Della