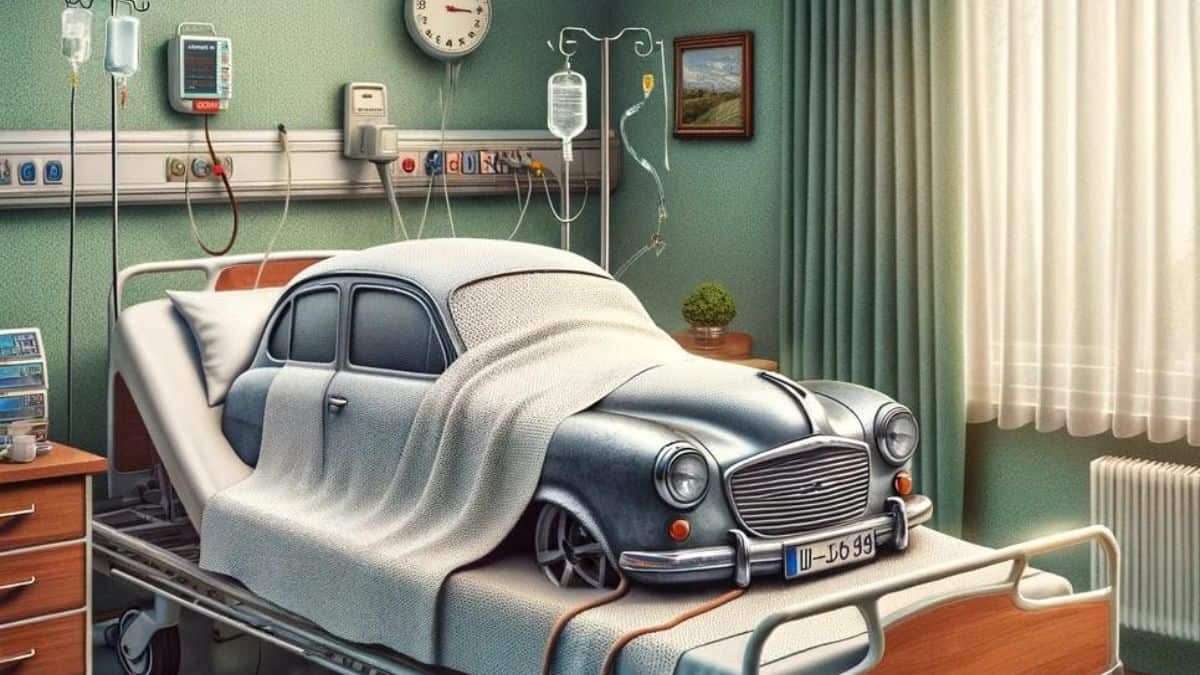
Over the past ten years, I've had many, many discussions with healthcare professionals (doctors, nurses, medical technologists, pharmacists, etc.) about applying the “Lean” methodology to improving healthcare. It's hard to ignore the fact that Lean, or the Toyota Production System, has its origins in manufacturing. It's also becoming difficult to ignore evidence from the past ten or 15 years that shows Lean can make a big difference in healthcare (although that doesn't mean that it's easy or guaranteed to work).
Many people in healthcare are open to ideas from other industries, including checklists and other safety practices from aviation. Others, however, are skeptical (if not cynical) about outside ideas or new approaches for a number of reasons. Skepticism is perfectly understandable and acceptable (if not desired). I've always found it to be more helpful to have open discussions with people about their skepticism and concerns rather than have them passive aggressively nod and shake their heads in fake agreement.
When healthcare professionals or leaders are being particularly closed minded (meaning they are not even willing to listen or learn), we often get this opposition thrown at us, in person or online:
“Patients are not cars!”
Sometimes, it's hard to not react in a way that says, in words or in body language, “Well, duh!” See, these things are not the same:

I try my best to be patient and kind when I hear that objection, even after hearing it countless times.
The implied (or sometimes directly stated) objections to using ideas from manufacturing in healthcare include things like:
- Every patient is unique!
- You can't turn a hospital into an assembly line!
- Medicine isn't just a bunch of algorithms, it's an art
- We're not just cranking out thousands of the same widget here…
- There's too much variation in healthcare for Lean to apply
Or, sometimes, they're meaning to say something like, “Leave me alone, I'm fine with how things are,” even if the current healthcare systems in the first world don't always serve patients as well as possible (patients wait too long, costs are too high, and or too many are harmed by preventable medical errors).
When people say, “Patients aren't cars,” they might want us to back off and shut down the discussion. Do they expect us to say, “Oh, you're right… my mistake… never mind”?
When people don't know about or don't understand Lean, it's easy to see why it might not apply. Patients ARE very different than cars. A hospital IS very different than a car factory. We need to understand these differences so we can best apply these applicable and transferrable Lean principles.
Lean is not a system for building cars better. Lean works well in aerospace, even though people could rightfully say, “Airplanes are not cars!” Yes, planes are far more complex. They are produced in lower volumes. To some degree, every plane built is unique… but Lean still applies at companies like Boeing, Lockheed Martin, and others.
Lean is not a system for “cranking out thousands of widgets” that are identical. Last week, I visited a factory near Fort Worth that makes large signs for customers such as restaurants, hotels, gas stations, and hospitals. Every sign is unique, even if they share common branding and design elements. The factory produces relatively low volumes and highly customized products (see my blog post about them). But, Lean works.
Lean works in these different settings because Lean is not about the product being built and success with Lean is not dependent on having a low-variation product or service.
Lean works in healthcare (see some results here) because it's a flexible methodology, culture, and management system that's focused on:
- Developing people
- Leading people and teams
- Improving processes, leading to better quality and better flow
- Solving problems
- Redesigning how work is done
- Continuously improving
- Engaging everybody in that effort
Again, Lean is not about building cars. It's about building people, developing people, leading people. It's about people, not cars.
The next time somebody tells you, “Patients are not cars,” maybe you can respond with a kind, agreeing smile and then say, “So, let me help you understand how Lean is making a difference in healthcare.” You can share examples from health systems like ThedaCare, Virginia Mason, Franciscan St. Francis, Baylor Scott & White, and others. The applicability of Lean to healthcare might have seemed like a theory in 2005. In 2016, it's a proven reality.
We need to help people understand that Lean healthcare is about:
- Providing the best quality, most affordable care that can be accessed quickly
- Creating better workplaces for those who are caring for patients
That's hard to argue with.
Mark Graban (@MarkGraban) is a consultant, author, and speaker in the “Lean healthcare” methodology. Mark is author of the Shingo Award-winning books Lean Hospitals (the 3rd edition is being published in June) and Healthcare Kaizen. He is also the VP of improvement and innovation services for the technology company KaiNexus and he's a board member for the Louise M. Batz Patient Safety Foundation. Mark blogs most days at www.LeanBlog.org.
Please scroll down (or click) to post a comment. Connect with me on LinkedIn.
Let’s work together to build a culture of continuous improvement and psychological safety. If you're a leader looking to create lasting change—not just projects—I help organizations:
- Engage people at all levels in sustainable improvement
- Shift from fear of mistakes to learning from them
- Apply Lean thinking in practical, people-centered ways
Interested in coaching or a keynote talk? Let’s start a conversation.
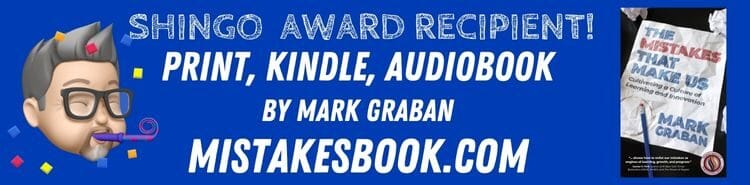