Going through some old files, I found an article that I wrote back in late 2005. I wrote it for somebody within our J&J Lean Healthcare circles, trying to help draw parallels to the idea that a hospital lab couldn't just copy a “Lean layout” without also changing the way they work. I never published it here on the blog, for some reason.
I'll publish it as I wrote it… you know that “American Motors” is clearly GM from my experience there. It shows how unclever I was at hiding the company, ha ha.
Do you seen any parallels to healthcare in 2015? Do organizations get in trouble by copying a particular physical layout, say for an emergency department or a clinic, only to find that they don't get the same results because they don't have the same Lean management system or Lean processes.
The following case study is based on a real situation.
Manufacturing companies often benchmark their competitors and look for things that better-performing companies are doing that can be copied or adapted. In the mid 90s, an automaker, let's call them American Motor, discovered a large productivity and quality gap between them and a Toyota plant that made a similar product – a modern, large V8 engine.
In studying the Toyota plant, the AM executives discovered that Toyota used different production equipment and a different layout for machining engine blocks, a key component in the engine. Traditional AM engine block production lines had individual machines that weren't connected. Workers would load heavy aluminum blocks into a machine and would then unload them onto a pallet that held 18 engine blocks each. When this batch of 18 engine blocks was complete, it would be moved, via fork truck, to the next operation.

This batch production system had many downfalls. One was the large amounts of WIP (work in process) that could accumulate between machines. If one machine broke down, workers would keep other machines busy, accumulating WIP in an effort to “keep costs down” (from an accounting perspective) by producing more, although it also increased inventory costs (which wasn't emphasized as much in the plant's metrics). This batch system also led to expensive quality problems, as it could take a long time before the next operation detected a defect created at the last operation. With the large batches and pallets of inventory, an upstream machine could have been making scrap for eight hours before it was detected.
Realizing that they needed to move away from the batch system, AM did their best to copy the layout of the Toyota engine block line. AM bought the same machining equipment and the same conveyor automation that Toyota had purchased. AM had the equipment installed in the same “S-shaped” layout that was supposed to increase operator efficiency and communication, as workers could more easily move between machines and work together to solve problems. With the automation, the amount of WIP was capped at five engine blocks between any two machines. With 15 sequential machines in the process flow, if any one machine went down, the other machines would quickly be forced to shut down because they would be out of parts, or because there was no room for blocks to move forward to the next machine.
Although expectations were high, once AM had this lean line up and running, they ran into some problems, and they weren't reaching the quality and productivity benchmark targets of their competitor. One complaint from the people running the line was that machines broke down too often, forcing the entire line to a complete halt. The AM solution was to fall back on old habits – finding ways to keep other machines running by using hoists to pull engine blocks off of the conveyors and stacking them onto pallets. AM supervisors told their workers to do what they had always done, even with the new equipment. This introduced new safety and ergonomic concerns, as the lean line wasn't designed for easy operator access, as parts were meant to stay on conveyors.

After running the new line for a year, AM conducted another benchmark study against the Toyota plant. AM management was stunned to find that their line ran at only 35% efficiency, meaning that if their planned goal was 90 blocks per hour, they were producing only about 31 block per hour, on average. The Toyota line, however, was averaging over 65% efficiency, meaning they were producing almost 60 blocks per hour, almost double the AM output. Quality was also much better at the Toyota plant, with far fewer than half the scrap and defect rate of the AM line.
The AM managers were puzzled, how could they be producing only half of what Toyota did, when they had spent all that money on the same equipment, the same automation, and the same layout? Not only was AM's performance worse than Toyota, but their productivity was worse than it was with their old batch layout.
What AM failed to adopt was the management system and the lean practices that were in place at Toyota to support their new engine block line that had “lean equipment” and a “lean layout.” Because AM did not use such lean tools as Total Preventive Maintenance, the equipment broke down much more often than the Toyota machinery, even though it came from the same vendor. Because of the downtime and the lack of buffers (remember when one machine was down, the entire lean line quickly went down), the AM lean line produced less than the old line with all of the pallets of engine blocks. Sure, inventory was lower with the AM lean line, but they were having trouble keeping up with customer demand, which caused a great deal of trouble for management.
Another concept that AM did not adopt was proper lean supervision and a continuous improvement, or “kaizen”, mentality. While Toyota team leaders made sure standard work was followed and helped drive root cause problem solving, the AM supervisors did their job the way they always did, even though they were also now called “team coordinators.” The AM supervisors beat up on maintenance and yelled at them to fix machines faster. The maintenance teams were constantly fixing the same problems because proper standard work was not in place for the operators (which led to mistakes that caused downtime) and because root causes that would have prevented future downtime were not addressed. When a machine broke down at Toyota, the focus was on getting the machine running and figuring out how to prevent it in the future. When a machine broke down at AM, the yelling ensued and fingers pointed. Nobody wanted to volunteer information that could have been useful for fixing the root cause problems.
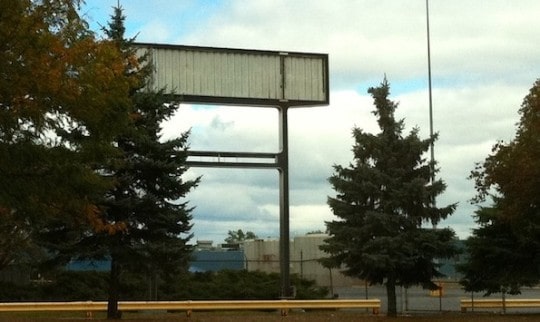
In addition to not working as a team when a problem occurred, the production workers weren't working as a team to run multiple machines during the day. At a Toyota plant, one worker would move and keep multiple machines running, as almost everything was automated, including the conveyors between machines. At AM, supervisors and workers stayed in old habits of “one man, one machine” where, even with the automation, workers would stand and watch a machine “just in case” it broke down or had a problem. This hurt the AM plant's labor productivity, a major metric for their management.
Often times, when the AM lean line was actually fully running, they would run out of their raw material, the castings that came from the AM foundry in Indiana. Because AM did not address their ordering practices by implementing kanban, they were still placing large batch orders through an unreliable MRP system. Even though demand for engine blocks was very stable, the orders given to the supplier varied wildly, which made it hard for the supplier to keep up. The Toyota plant did not have to worry about raw material availability because they had a better system in place than AM.
The lesson that AM eventually learned was that it wasn't enough to simply buy the same equipment that Toyota had. AM had to learn about the management practices of the Toyota Production System and had to embrace a new way of managing the plant day to day. This meant adopting a new approach to supervision and leadership, as well as teaching a broader set of lean tools, and adopting a mindset of continuous improvement. To do so required the leadership of a Plant Manager who had been trained by Toyota and understood the holistic system that had to be put in place. Within two years of new leadership and a true lean system, the AM closed the productivity and quality gap with Toyota, moving up from being the worst engine plant in the U.S. to being in the top quartile. This was all with the same lean equipment that had been in place and with the same hourly workers. It was a new management system, the Toyota Production System, that led to dramatic improvements for the plant and for AM.
Please scroll down (or click) to post a comment. Connect with me on LinkedIn.
Let’s work together to build a culture of continuous improvement and psychological safety. If you're a leader looking to create lasting change—not just projects—I help organizations:
- Engage people at all levels in sustainable improvement
- Shift from fear of mistakes to learning from them
- Apply Lean thinking in practical, people-centered ways
Interested in coaching or a keynote talk? Let’s start a conversation.
Hi Mark.
Totally agree. Recently heard a discussion in the radio about productivity and wages in México. Here we´re debating whether or not increase minimal wage. One complain or analysis many “experts” agree with is that México isn´t as productive as other countries. That as a barrier to increase minimal wages. I agree. They also agree and recommnend to invest in technology cause, to their eyes technology is the way to increase or improve productivity. This post clearly shows that isn´t enough. Sometimes, creates more problems, cause we do not understand the problem we want to solve. This post made sense to me. Hope some “experts” would read good quality stuff to expand their minds and realize that technology is only a tool that works, when correctly applied to solve a problem, guided by the right principles.
With an increased minimal wage or higher wage levels, don’t manufacturers then have more of an incentive to use automation or technology to eliminate some jobs?