Today's post is being hosted by the Lean Enterprise Institute and their “Lean Post” blog… click on the headline below or the image to read:
“Standardization is a Countermeasure, Never the Goal“
It's a post that encourages people to “ask why” when thinking about standardized work, 5S, and other Lean practices.
Instead of thinking “what tool should we implement?” the question should be “what problem are we trying to solve?”
The same tool or tactic (putting tape around a stapler) might be really helpful in one environment because it prevents a problem (such as at a nurse's station) and it might be silly and antagonizing in another situation (an individual office worker's desk).

Some other recent Lean Post articles that I particularly liked include:
- Doing Lean Versus Becoming Lean (Jim Luckman)
- Are We “Doing Lean” All Wrong? (Brent Wahba)
- Problem Solving Fast and Slow (Ben Root)
- Test Your PDCA Thinking By Reading Your A3 Backwards (Tracey Richardson)
- Put Your Strategy on a Diet (Pascal Dennis)
Please scroll down (or click) to post a comment. Connect with me on LinkedIn.
Let’s work together to build a culture of continuous improvement and psychological safety. If you're a leader looking to create lasting change—not just projects—I help organizations:
- Engage people at all levels in sustainable improvement
- Shift from fear of mistakes to learning from them
- Apply Lean thinking in practical, people-centered ways
Interested in coaching or a keynote talk? Let’s start a conversation.
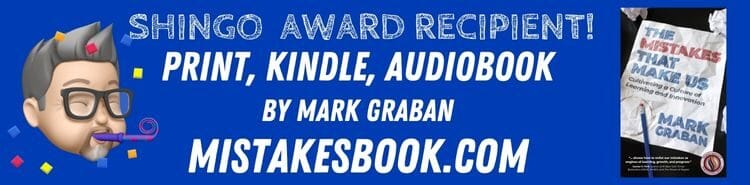
Definitely agree. My former organization emphasizes standardization as the first step in continuous improvement when it should be understanding the problem. The organization is mindlessly running around developing standards and wondering why the new standards are often ineffective.
Recently someone asked me “Where do we start with Lean?” My answer was, “Where you see the problems and that will determine which “tools” you use.” They had already had an “expert” consultant who seemed to follow a checklist of the tools which had to be implemented to make the company “lean”. Although I believe the intentions were good, and some improvements were obtained, there was not a transformation of the culture into a problem solving, continuous improvement environment. Hopefully the correct approach will result in engaged employees and tap into their ideas for taking care of the issues they face every day.