
I've been going back through my notes and pictures from my first trip to Japan in November… my goal is to blog about something or share a picture on a weekly basis. Read more about my guides, Kaizen Institute.
We visited two Japanese hospitals during our tour. At one of the stops, a large part of the focus was on the 5S methodology. As you would read about in the book Clinical 5S For Healthcare, the term “5S” seems to really be a description of a broader Lean approach in Japan. I've seen Masaaki Imai, from Kaizen Institute, talk about “5S” and, to me, he was talking more about “Lean.” Anyway, I'll share some pictures and notes from that visit.
Does This Come Naturally?
As I wrote about before, many aspects of “Lean” culture “don't come naturally” in Japanese business culture. People don't naturally speak up, because the culture says “don't make waves.” The organizations we visited were, to some extent, all trying to create a culture that was different than typical Japanese business culture.
5S wasn't magically happening at the hospital I am writing about today. The OR areas had cabinets that were apparently just as messy and disorganized as any American hospital I've seen before. Sure, Japan is a country where people are generally packed in very densely, so space is at a premium… but 5S was something they worked at as opposed to being something that happened automatically based on some sort of “5S gene.”
Join our future tours:

Why 5S?
The CEO of the hospital greeted us and talked about how he has learned from factories (a theme I have written about and spoken about).
He learned about 5S from Toyota and stated the goals of 5S as:
- Always have all the parts you need
- Have everything you need for your job when you need it
- Not hurting workers
- Efficiency and safety
This CEO seemed to get it.
He said, “Good 5S means we can run the hospital well and it's good for the patients.”
The “5S chairman” said one of the biggest benefits of 5S was breaking down the silos between departments – the siloed organizations are a big problem in Japan as they are elsewhere.
5S often gets labeled as a “workplace organization” system. Workplace organization is a method for achieving the aims of 5S. The goal is providing the best care. Reducing waste and making problems visible (through 5S) saves time that can be better re-dedicated to the patients. If a “workplace organization” program is just a top-down mandate where we're forcing people to comply… that's not 5S and it's not Lean.
You're not going to break down silos if you're just using “5S” to put tape around objects on desks.
CEO Participation and Leadership
The CEO here took the lead and cleaned up his own office first. Did that improve efficiency and safety for him? Maybe. The real organizational benefits of 5S aren't in the CEO's office (although he could save time by not having to search for things), but he led by example. That's different than forcing others to do 5S. He also participated directly in 5S “gemba” (workplace) walks and 5S audits, which is somewhat unusual except for CEOs in the “most Lean” of U.S. hospitals.
From a picture he shared – including the CEO (front left) doing the audit.
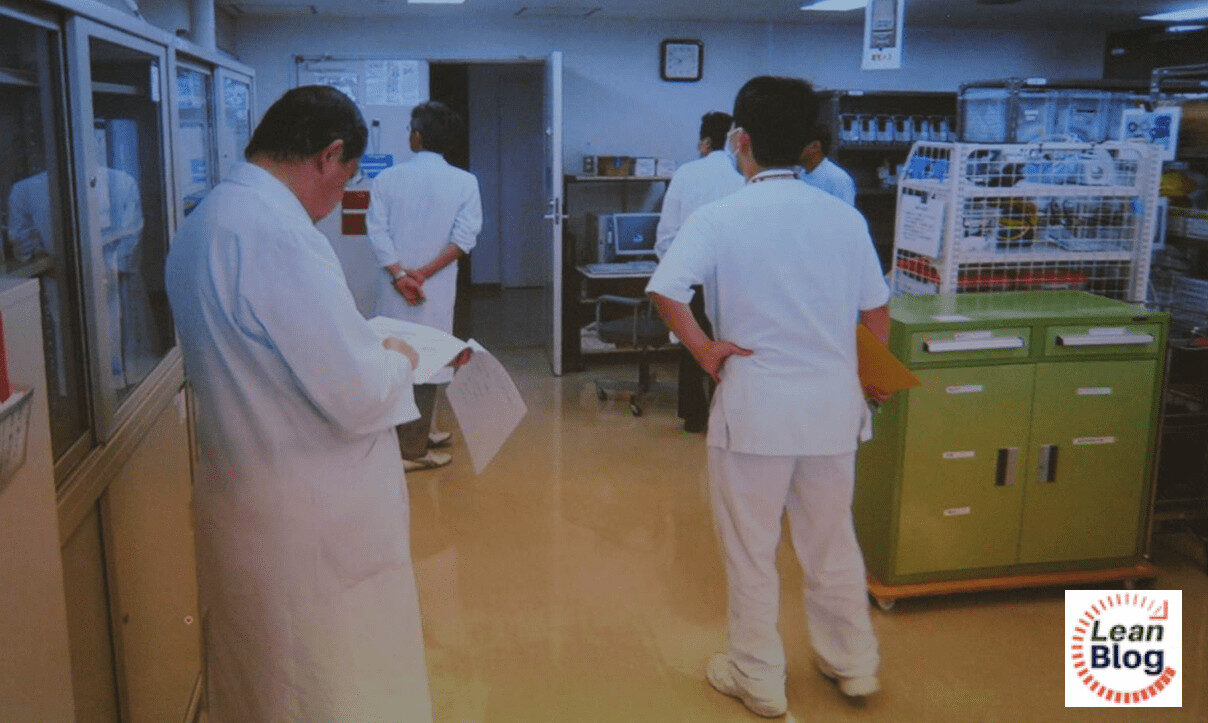
5S Helping Nurses AND Patients
The team of nurses we saw in the workplace (an inpatient unit) seemed very engaged in quality improvement, in general.
They showed us how they applied 5S to their desk drawers in the shared nurse's station:
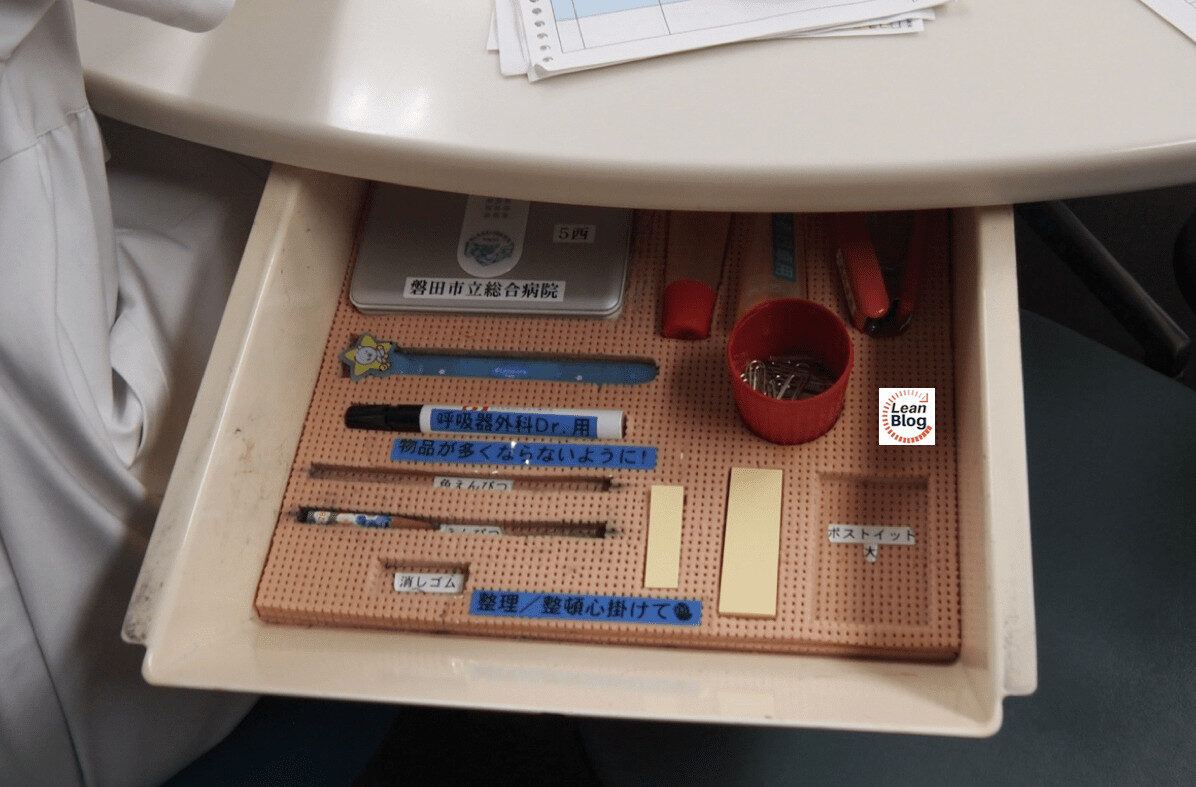
You can see the foam cutouts. I don't read Japanese, so I can't tell exactly what is missing… but you can see SOMETHING is missing (a pen and a certain size of post-it note?).
Please don't misinterpret this blog post as me saying “You must do this with your drawers if you are doing Lean.” Please don't just copy.
Always start by asking, “Is there a problem with our current state? What is the problem?” Why is a certain method being used?
Is this desk drawer, in and of itself, going to save lives? Maybe not… but it's just one example of their “kaizen” improvements. It's great when employees take the INITIATIVE to do stuff like this. It's not cool when they are FORCED to do this by the boss. Big difference.
This picture of a cart shows 5S that might save even more time for nurses if they are in and out of this cart all the time:
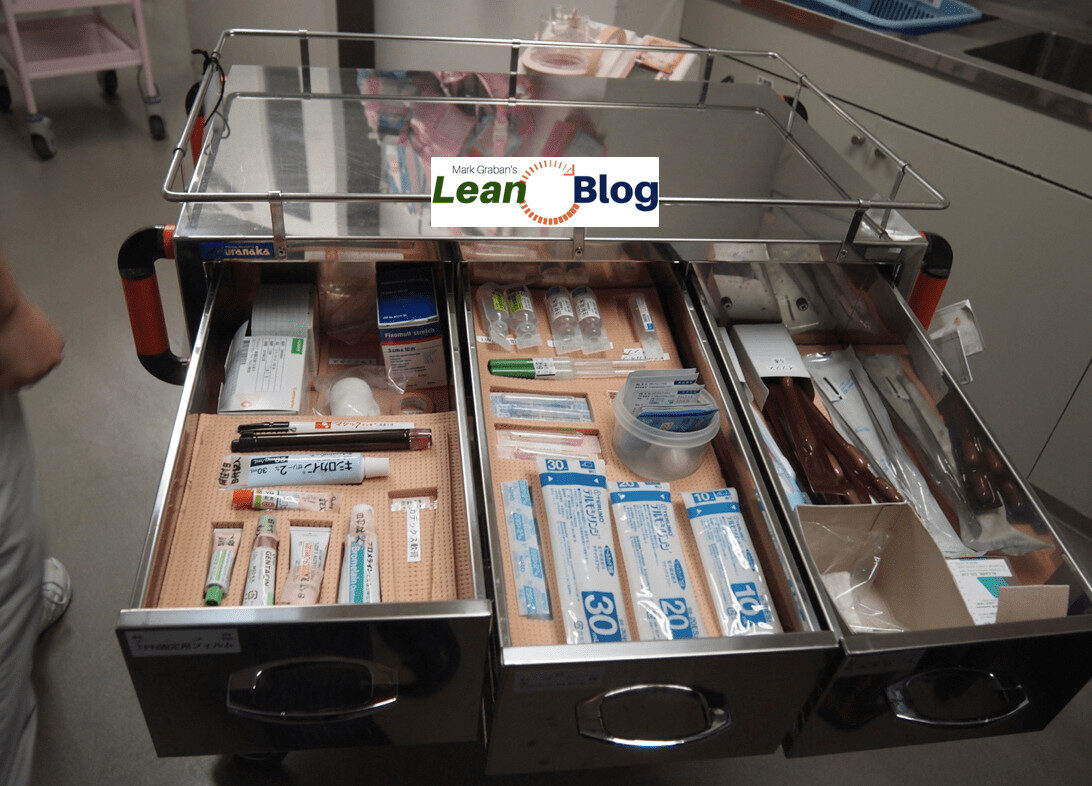
And there is this crash cart, below, where they are trying to make sure medications are never missing when they are needed. This was staged, by the way, to show one missing. It wasn't actually missing or putting anyone at risk.
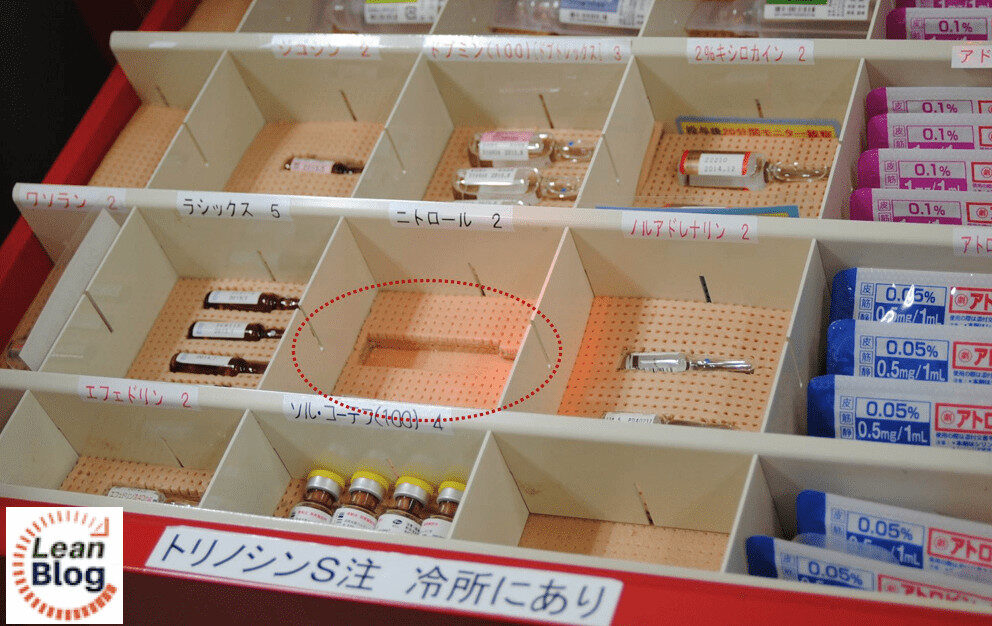
And here is some 5S organization of power strips:
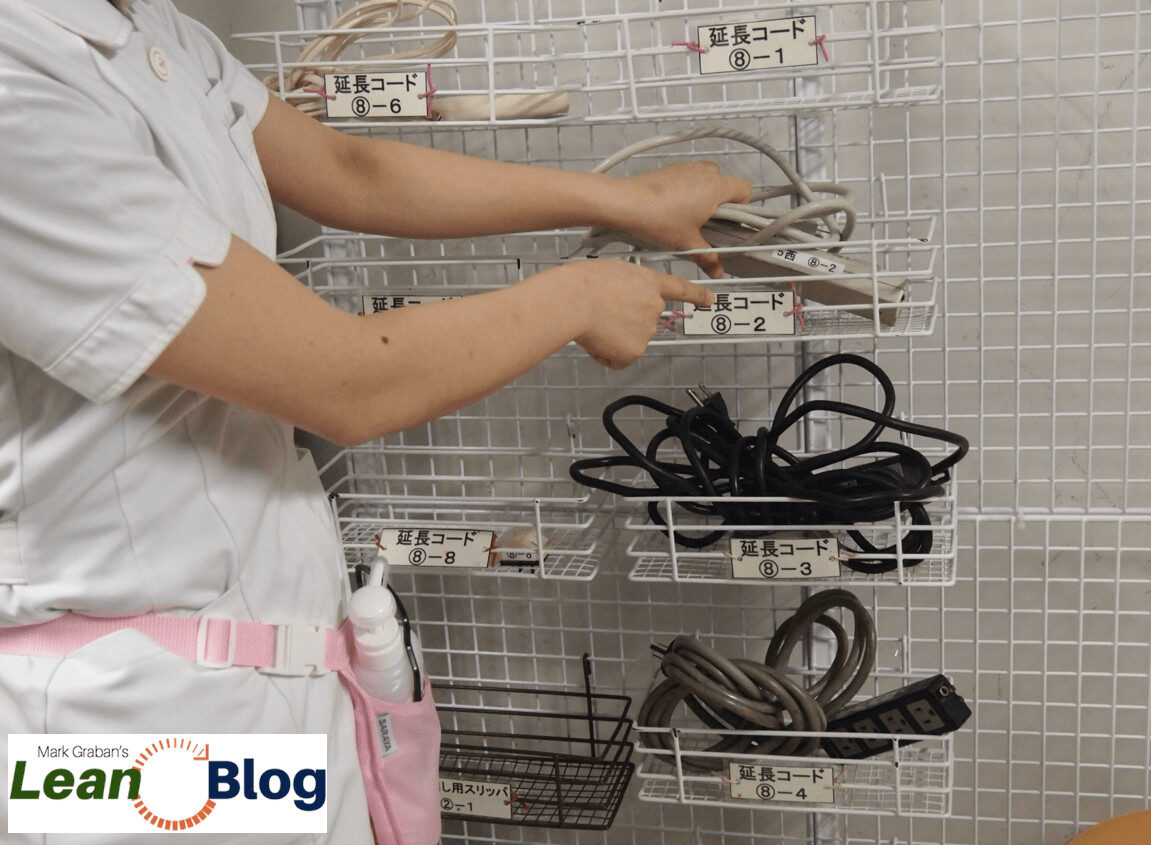
But on to the coolest thing… you might ask, “What is her pink bag?” You saw a small picture of part of one at the top of the post…
It's a bag that the nurses where to, of course, make sure the most frequently needed small supplies are always available, like tape and hand gel.
A picture of one bag along with the way they were hung in an organized way. I'm not sure why some bags are blue. I should have asked.
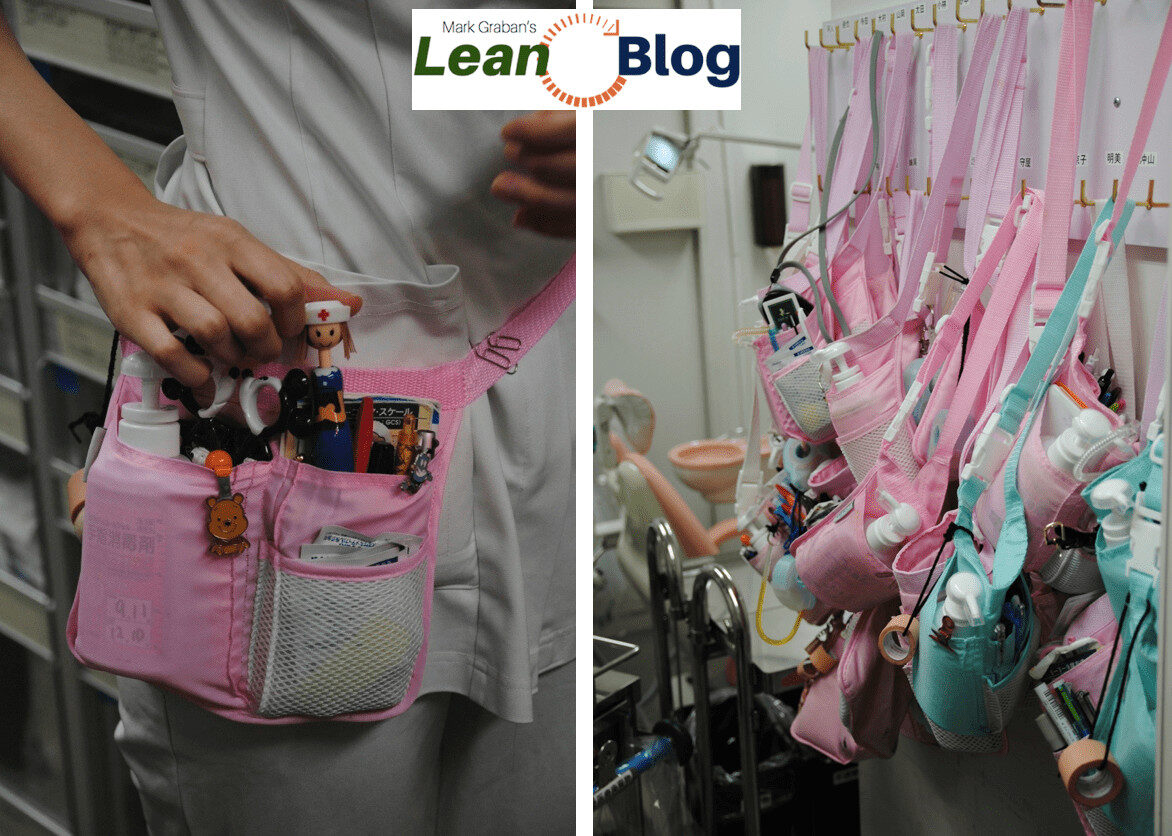
That's at least a little bit about what I saw at the one hospital. I'll definitely write more about the other themes and topics from the visits, but that's it for today.

Please scroll down (or click) to post a comment. Connect with me on LinkedIn.
Let’s work together to build a culture of continuous improvement and psychological safety. If you're a leader looking to create lasting change—not just projects—I help organizations:
- Engage people at all levels in sustainable improvement
- Shift from fear of mistakes to learning from them
- Apply Lean thinking in practical, people-centered ways
Interested in coaching or a keynote talk? Let’s start a conversation.
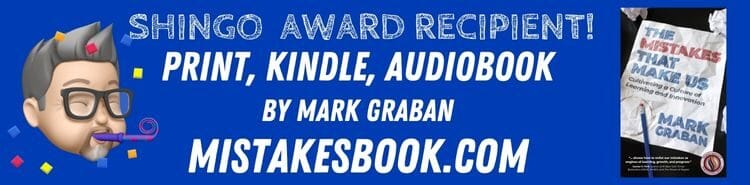
Some great photos and great ideas, Mark. Thanks for posting.
Great information!
[…] Going to Gemba and seeing 5S at a Japanese hospital This is a great read about how one hospital in Japan truly embraces lean and the 5S principles. Always start by asking “Is there a problem with our current state? What is the problem?” […]
Dear Mark,
I was wondering if you plan for another Lean healthcare trip to Japan in 2014. I am based in Malaysia. I look forward to receiving your feedback
Many Thanks,
Maria
Hi Maria – no plans at this moment, but I hope to again in the future.
Hi Mark,
I bet dollars to donuts that the blue bags are for male nurses. My wife is Japanese and I can tell you…pink is for girls and blue is for boys. Simple non?
Cheers,
Craig
Ah, great point. That makes sense. I don’t recall seeing any male nurses, at least during the shift I was there. The ratio of pink to blue bags suggests the nurses would be predominantly female. Thanks.
I’m working with Kaizen Institute to do another Lean Healthcare study trip to Japan, the week of November 17. 2014.
Contact me if you’re interested in learning more.
[…] Japan Trip: Going to Gemba and Seeing 5S at a Japanese Hospital […]
[…] Poka-yoke, visual management, SMED and 5S […]
[…] placement when not in use and an easy indicator to team members when it is in use. Here’s a good article on 5S by Mark Graban of the Lean […]