We are going through the editing and typesetting process for our upcoming book Healthcare Kaizen this week.
After not really looking at the manuscript for a few months, a particular line stood out and made me think, as it's the description of a “chicken and egg” dynamic – what comes first in Lean, TPS, and Kaizen: respect for people or continuous improvement? You can't have one without the other.
We wrote:
“We strive for continuous improvement out of our respect for people, but it is our basic respect for people that helps make continuous improvement possible.”
I hope people find that to be an interesting point or something that's helpful in their Kaizen work. It's what the “systems dynamics” field of Jay Forrester and Peter Senge would call a “positive reinforcing loop.” But how do you get it started?
Please scroll down (or click) to post a comment. Connect with me on LinkedIn.
Let’s work together to build a culture of continuous improvement and psychological safety. If you're a leader looking to create lasting change—not just projects—I help organizations:
- Engage people at all levels in sustainable improvement
- Shift from fear of mistakes to learning from them
- Apply Lean thinking in practical, people-centered ways
Interested in coaching or a keynote talk? Let’s start a conversation.
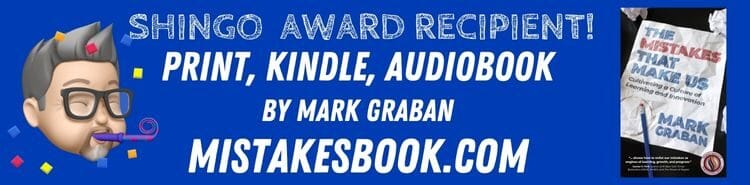
When is the book due to be released Mark?
You never know with publishing sometimes… should be May or possibly June. You can sign up for updates at http://www.hckaizen.com or I’ll post updates here on the blog.
RP enables CI. We have enormous empirical evidence that CI does not enable RP (e.g. the ubiquity of Fake Lean / LAME). It is more common to see CI disabling RP in management’s drive for immediate cost reduction.
Get it started by telling and demonstrating to people – especially employees and suppliers – that Lean management will not cause them harm.
You can certainly start on the road to CI without people respect. But, just like lowering inventory exposes sloppy inventory management so does focusing on continuous improvement expose all the real deficits in leadership. At that juncture the leader either gets it and changes (humility and learning) or sets up a delegation model. The problem with delegation is that as the delegates move ahead the leader gets further behind. This increasingly generates contempt and resentment as it becomes obvious to all except the corner office what (who) the constraint to CI is. This problem is not unique to healthcare as many “lean” manufacturing organizations relegate lean to the shop floor with superficial benefit.
The optimal relationship – the sweet spot of super performance, comes from the emergence of the people blended with continuous improvement. Of course this means kaizen must have its hansei (reflection), management must have its leadership, work must have its spirit to optimize performance. To miss this is to miss it all IMHO.