Episode #56 of the podcast is a discussion with John Shook, one of my absolute favorite people in the Lean world.
The few times I've seen John present or had the chance to chat in person, I've learned more in that amount of time than from anyone else, so I'm thrilled to have him here. John has a new book, published by the Lean Enterprise Institute, about the “A3” problem-solving process called Managing to Learn: Using the A3 Management Process to Solve Problems, Gain Agreement, Mentor, and Lead. John also has a new blog on the LEI website, which is exciting to see. In the podcast, we discuss the story behind the book and some thoughts on how to get started with A3 thinking from scratch in your organization.
Episode #56 Key Words and Links:
- About A3s (via John's blog)
- Lean Enterprise Institute
- John Shook's Lean Management Column (blog)
- Problem-solving, kaizen, A3 thinking, A3 reports
If you have feedback on the podcast, or any questions for me or my guests, you can email me at leanpodcast@gmail.com or you can call and leave a voicemail by calling the “Lean Line” at (817) 993-0630 or contact me via Skype id “mgraban.” Please give your location and your first name. Any comments (email or voicemail) might be used in follow ups to the podcast.
Listen to the podcast here
John Shook, “Managing To Learn”
This is episode number 56 of the show for January 6th, 2009. I want to wish a Happy New Year to everybody. I have a lot of exciting episodes ahead, including this episode with John Shook who is a Senior Advisor with Lean Enterprise Institute. He was one of the first Americans to work in-depth with Toyota so he has quite an expansive knowledge of the Toyota Production System.
He is the author of the book, Learning to See: Value-Stream Mapping to Add Value and Eliminate MUDA and the author of another book published by the Lean Enterprise Institute called Managing to Learn, which is about the A3 problem-solving process, A3 reports and the A3 management system. We're going to be talking about that in this episode. If you have any feedback or questions for John, you can send them to me or interact with John on his blog, which can be found at Lean.org/Shook. Hopefully, we'll be interacting with John here in future episodes. As always, thanks for reading.
—
In this episode, our guest is John Shook. John, thanks for taking time out and joining us on the show.
Thank you, Mark. It's good to be here.
It's an exciting time. Your new book, Managing to Learn, is out and available. I was wondering if you could tell us some of the stories behind the book, what the inspiration was and some of the main lessons you hope a reader would get out of the book.
I could talk about the story behind the book for probably too long. Amazingly, I feel okay about it. I'm usually pretty critical of work. You've written yourself. It always feels good to get it done. It took a while. I probably worked on this fairly steadily off and on for two years. I probably first talked with Jim Womack, the publisher, about it years ago. I was very hesitant.
It goes back to Learning to See if you remember the book that came out years ago with my co-author, Mike Rother. Even then, I was a reluctant participant. It wasn't my idea to do that book. Mike and also the publishers, Jim [Womack] and Dan Jones, wanted to do it. I was even concerned then about when you roll out a tool, it's not like there weren't already a lot of tools out there.
If you go back to looking at SPC or a lot of the old TQM stuff, it becomes something that's mandated. It becomes a check-the-box exercise and a corporate wallpaper. I was a little worried about that with value-stream mapping but that was so different. As we came up with the title of Learning to See, I agreed that it was a good idea. That was that story years ago.
Jim Womack wanted to do a book about the A3. I was even more worried because do you know how almost all the Lean tools are deceptively simple? They're simple on the surface but there's more meaning as you get into them. That's truer of the A3 than anything because the tool itself is nothing. It is a blank piece of paper that you use to tell a story. You can tell a story small or big on one sheet of paper. It was so easy then to do that.
I was very concerned about a book about it that would become another thing that people used as a check-the-box exercise. Doing storyboards or six-panel storyboards had been around for a long time. People have done that. I was concerned about that. I thought about it and decided that I would only do it if I could somehow tell the story from a couple of perspectives, both someone learning how to write an A3 or go through the A3 PDCA process but then also the other side of someone who is mentoring a learner as they were going through that process. If I could tell both of those stories, then they could maybe have some value.
The A3 was very important to all the work that I learned when I joined Toyota many years ago. It's not that I didn't see the value that it could be important but I wanted to make sure the deeper story got out there as well. You can learn to write an A3 in a day but learning to use it as a management process is something that takes longer.
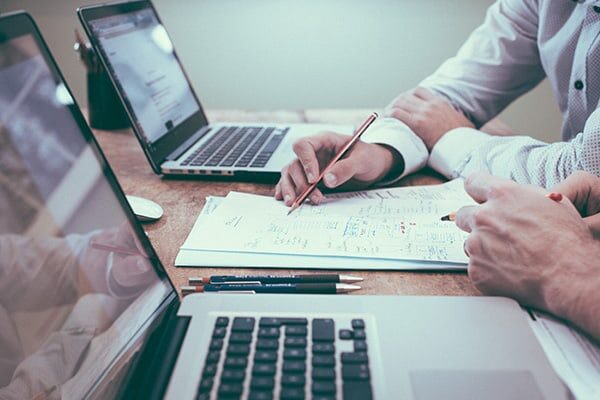
Through some little trial and error, we came up with this idea. I said, “What if we told two parallel stories? It is two columns side by side.” We were worried that readers wouldn't be able to deal with that so there were counter proposals. A lot of people said, “Maybe it should be sequential.” You tell the learner's story and then at the end of the chapter, you tell the other person's story or something.
I wanted it to be more dynamic than that. We did a wrapped prototype of one chapter to see how it worked. We sent it around. I don't think Margie received that early draft but it was very early to see if it would work doing it that way. I liked the idea. I was comfortable with it and with the idea that it could capture what the title says, which what we're doing is managing to learn. There's a double meaning there. As managers, we are trying to manage a learning process.
The other thing is we all as individuals are trying every day to manage to learn as we stumble through the work issues that face us every day. If it could do that and tell the story from two perspectives, a learner or a mentee and a mentor or boss, then I thought it could have some value. That's the story behind the book.
Through that liberal use of some sidebars to tell some of the conceptual pieces and show one person creating an A3 from beginning to end, we decided to use a non-manufacturing process. Sometimes, I still wonder if that was the best thing to do but many people still see Lean as purely a factory floor thing. It seemed to be an opportunity to go outside of that. A lot of the work in companies does take place with people working on projects, planning projects and getting bigger things together to move an organization forward than what takes place in the planning. Although the gemba is where we want to focus things.
I'm hoping that people can see then that it is an overall process. We coined the term the A3 management process. It was to emphasize that it's not just a piece of paper but there's a process there that can enable you to do a lot of things. That's assuming that you want to do those lots of things, which means solving problems but also gaining agreement in the organization, mentoring people and leading people.
If you want to manage in the way that I saw as an effective way of managing at Toyota, then the A3 can be an enabler. There is no guarantee it is a success but it can be an enabler. That was some of the inspiration. LEI wanted an A3 book. I only wanted to do it if I could present it in a way that would embody the broader management context. It manages to do both. I hope so. We'll have to let the readers know how it succeeds.
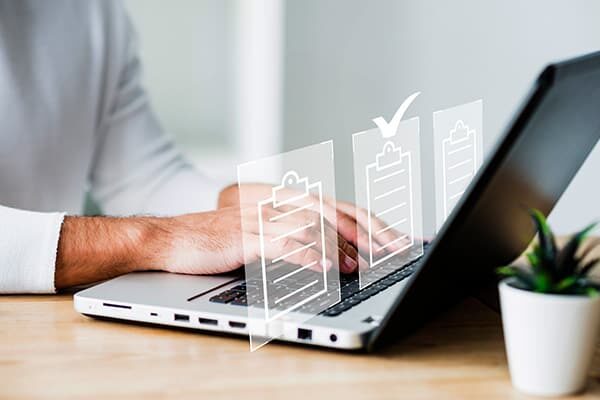
As the one reader sitting here, the two-column format certainly lends a very rich story to try to get in the head of both sides of the student and teacher. It took a little getting used to, the flipping back and forth. I tend to read a couple of pages and then go back and make it semi-sequential myself. It is a unique method. I can't imagine the challenge of trying to get complex concepts where typically, as the story says somebody is coaching you. It's very interactive. A book is, decidedly, non-interactive linear. I could see the challenge in that.
I appreciate that you appreciate the challenge. I will give myself a good grade for effort anyway for execution. You and others will have to have to give the grade. It is complex to tell the two stories running parallel side by side. I've never seen another book like it. I expected more people to complain about the difficulty of reading it but it hasn't come up much. I like the dynamism of it.
When you go to the plant floor or walk down the hallway at work, sometimes two people speak to you at once. Life doesn't come at you in a linear fashion, which a book is, by nature, linear. What we've done in this case is try to show a little bit more of that dynamic nature. You do have a choice here to read the left column first or the right column first. That is like when two people yell at you at the same time. You have to choose, “Am I going to talk to you first or you first?” People are finding what you did, which is that you read a couple of pages and find a way to read it that's comfortable to you.
Life doesn't come at you in a linear fashion. Share on XI do find the formal A3 methodology and thinking process fascinating. I can't claim to be an expert on the A3 methodology as it's laid out. I've never worked in an organization like Toyota that directly uses that. As someone with some experience with Lean, I certainly recognize a lot of the thought process, the elements and the concepts behind the A3 document.
One question I was going to ask for my learning and I would assume some of the readers is what tips do you have to make sure that it is not a document or a corporate wallpaper? I've been in some training classes where the form is so deceptively simple but sometimes, it seems to almost get presented or put together superficially. What tips do you have for people to make sure that they're incorporating the Lean thinking Toyota management thought process into the document instead of filling out a check-the-box type format?
The first thing is to take you to your last statement there and revisit the purpose of what we're doing here. If you're using the A3 because you want to manage in a way that embodies those principles that we're aware of, everyone would love to be the best Lean leader or Lean manager we could ever be. We would all love to be like Taiichi Ohno or someone whose leadership I've had a chance to witness over the years, Mr. Cho, the Chairman of Toyota. We can't be that so easily.
If that's what we want to aspire to be, a way that we're developing people, getting people to solve problems and moving the organization forward, we're taking the organization in a direction we want. If we use the A3 as a way to help us achieve that, then we can keep our eye on that purpose. We can hopefully prevent the tendency to focus on it as a tool itself.
You said how you can make sure that doesn't happen. I don't know if there's a way to make sure it doesn't happen. With the way we structured the book, certainly, it doesn't represent the notion that the point is filling in the blanks or the boxes. The other thing is I put it in a little small chapter toward the end there that we called Getting Started and that it takes 2 to A3.
That tried to give some hints about how to use it as a process. If you build in the discipline in the beginning that the focus isn't someone writing a good A3, although that's a key piece of it, we can begin teaching ourselves in the beginning that there are different roles involved in the A3 as a process. That's why I'm calling it a process. When I work with an organization to bring in the A3 to add to their suite of Lean tools or management tools, we always practice three different roles.
The first is the writer or the author. That's how you write an A3. If you want to decide that there are 6 boxes or maybe 7 in the A3 that's in the book, then that's fine. You go through a thinking process of defining the problem and what you're talking about. You're defining what's important about that from the company standpoint. What's the business context? What are the current conditions? Go to the gemba and see what's happening and then decide, “That's how things are happening. What are our goals? How do we want things to look?” Analyze the gap between the way things are and the way we want them to be.
It then goes at the discipline of eliciting a set of ideas, countermeasures and proposals. You're not jumping to one solution. One of the things Lean is not is jumping to a conclusion or solution. Once we've gone through all that, then we put it in our plan in a real timeline so we can see what we expect to happen by when along with our follow-up ideas.
One of the things Lean is not is jumping to a conclusion or a solution. Share on XThe first thing is to learn how to construct an A3 that tells that story. Whether you do that in 5 boxes or 7 boxes, it can be flexible. Many companies find it convenient, especially in the beginning, to make a standard template. I'm always skeptical of standard templates for something like that only because that tends to lean toward that tendency to see it as a fill-in-the-box exercise if you do that.
The second thing then as part of training or learning is in addition to learning to write an A3 as the author, the next thing is you have to present it. You use it to tell a story. We'll practice this. We'll roleplay this where you take your A3 and present it to someone. The third role, which is so very important, is the other side. As someone is presenting an A3 to you, how do you respond? There are different ways that someone can respond. A lot of times, the traditional leadership management responses to disagree to say, “That's not right. Here's what's right,” and to give someone the answer. We can use this format as a way to stop ourselves from doing that.
It is to ask some questions to ensure, first of all, that I understand the A3 that's being presented to me. Second of all, it is to say, “The person who's presenting this A3 to me, does he or she understand his or her problem?” If they have understood the problem, that leads us down a path of, “Let's examine the root cause and the can of possible proposals.” Often, they haven't identified the root cause. The A3 becomes a platform then that I can use to help that person see that they haven't gone to the gemba and haven't asked why 5 times, 10 times or however many times they need to to get to the root cause.
In the very beginning of training that I would do for the A3, I include those three roles in the beginning. We don't just practice writing them but we practice also using them as a communication tool and practice the other side, which is responding. It always takes at least 2 to A3. It sounds catchy, I suppose but it is true.
Managing to Learn does a good job of representing that back-and-forth process which seems familiar to other Lean methods like Hoshin Kanri and this back-and-forth learning and problem-solving style. One thing that jumps out and you see this in the book at the left-hand column character is having to go back and rework an A3, being challenged, going back, erasing and working on it again. I've heard people say sometimes, “It took me 10 tries or 10 attempts at an A3.” It makes me think, “Do people have patience for that?” What kind of feedback do you get from people about the back-and-forth nature of the process?
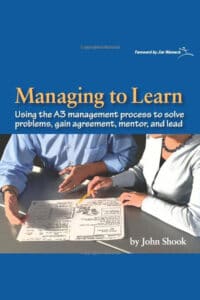
Only if you decide you want to manage this way, are you going to be able to do that? If you've decided, “I'm in an organization where people are jumping to conclusions and solutions all the time. We have hammers running all over the place looking for nails. We have a lot of activity going on by maybe a lot of well-intentioned people but we're working on the wrong things. No matter what we do, it doesn't seem to take the organization forward,” and you think that those problems are in place, then what that means is we need to learn how to go through a more rigorous thinking process.
We need to understand truly what's happening at the gemba. We need to understand why it's happening to the root cause and then we can be able to understand how all the different countermeasures and great ideas we have might or might not match up and link against the real problems of the day, the real things that we want to fix. If you recognize that, then you appreciate the fact that the A3 makes you slow down. The fact that you have those boxes there, it becomes uneasy.
It occurs in the example in the book where in the first instance, the learner adjuncts to a conclusion or a solution and feels fairly proud of it, I suppose. The mentor goes back and says, “We're going to stop and go through this step-by-step.” Having the A3 as a process to help you do that can enable us together to go through the process. It can help build in that discipline of patience.
We'd all like to be able to know the root cause immediately and know what would be the best solution to move forward against that root cause right away. What we're going to do is not make assumptions and not managed by a wishlist but ensure that we understand the situation and move through things in a disciplined fashion. If that's what you want to do, that can happen. It isn't a cultural change though, in many cases. It's not something that you can do effectively by yourself. You can start by yourself but then you want to start to use this and start engaging others. We're all going through this standard thinking process together.
Do not make assumptions and do not manage by a wishlist, but ensure that you understand the situation and move through things in a disciplined fashion. Share on XIt seems like it would be challenging to start from scratch with a process like this maybe on the one level because it requires this mentor back and forth. If you're an individual who doesn't have a good mentor to help you with the process and it takes two, it seems like you might end up with superficial A3 or not accomplish as much.
The second challenge might be if somebody is working in a big, large corporation that sounds like the opposite of what you described. A lot of organizations aren't very patient by nature. They want to jump to solutions. The boss has all the answers type of organization. This may be too advanced of a methodology for somebody who's maybe early in a Lean journey. Is that fair to say or am I being too sentimental?
I don't know that I would say it exactly that way. It can be a tool that you can bring in from the very beginning. You don't have to. I'm a believer that you can start from many places in many different ways along the Lean journey. Eventually though, what we want is an organization where people are having dialogues, where they're getting engaged and where leaders are developing their people. This can be a tool that they can enable that.
This is often in the beginning stages. It is used as a pretty simple, straightforward problem-solving tool. You're not going to get anywhere in any Lean initiative unless you are learning to problem-solve. Lean problem-solving is at the core of what we're doing. Bringing in any Lean tool in the absence of bringing along with it a focus on what is a problem and how we solve it is going to fail. This can be one.
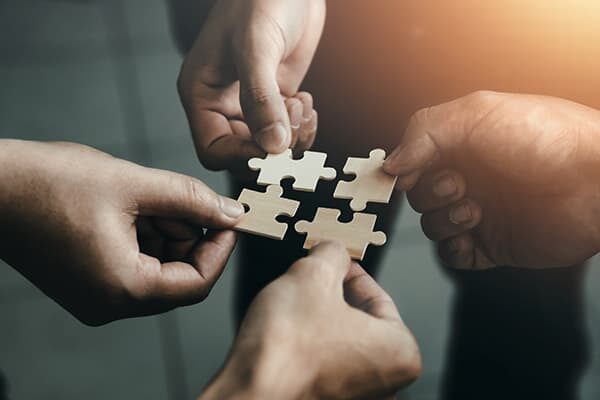
In the early stages, rather than complicated organizational change sources of proposal A3s, they can be centered around problem-solving and more simple problems. You are bringing into play the Lean problem-solving tools that are the essence of standardized working Kaizen. That's what standardized working Kaizen is. It's a way to see how things are and from that, determine problems and how to make improvements. It can come in from the very beginning.
The other thing I like about it from a flexibility standpoint is no matter if you're the CEO, manager or area manager on the plant floor or in engineering, you can start to use this for yourself. The individual, writing an A3 and going through the discipline of going through the questions and the thinking steps, will become a stronger problem-solver even if they do this on their own.
Sometimes, when I sit down and write one, I'll always be surprised at how forcing myself to go through the discipline of working on an A3, I'll recognize connections between things I thought I should do and how they connect or don't connect versus the real situation or problem. As an individual, there's a lot that can be gained and as an organization as well. You can start to use it even in the earlier stages of a Lean journey. The use of it is simpler but that's true of any Lean tool. When we begin, we try to use them in a simple fashion and then learn about them as we go along. We learn that we can use them in different more complex situations.
That dials back some of my cynicism. That's a good message. It sounds like you're saying that like anything, start small.
You mentioned two words, problem-solving and in the same sentence, you mentioned Hoshin Kanri as well. The thing is if you have a broad or want to start a broad corporate-wide Hoshin Kanri initiative, you need A3 as part of that. Also, when you go down to the very front lines of problem-solving, which you have to have and it's usually an important place to start, the A3 can structure that as well. It allows you to structure and tell your problem-solving stories around a standard story template. What it needs you to do then is to hook them up. Hook your frontline problem-solving activities that are structured around PDCA with your broader Hoshin Kanri activities as well.
If you're working at more of a broader company transformation level, it can be part of that. Also, it can be something at the front lines that one person or a small group of people can do as well. That's the thing about Hoshin Kanri. You can't do that so easily with a small group. That means you're talking about how the company develops strategies and works through them. With the A3 though, you can do it starting at any level.
I would love to dig into this more. Maybe we can do a follow-up conversation after more people have had a chance to read your book. I've talked to others who have either started reading or completed reading it. Maybe if there are questions, people can contact us and we can do a follow-up discussion. There is one other way and I don't know how interactive this has been so far. I've noticed you started doing a column or it's being done in the construct of a blog on the LEI website. I was wondering how that's going so far. Has it been interactive? Is it the John Shook newsletter that's coming out weekly?
Yeah. As I started getting toward the end of the book, Managing to Learn, I don't know how many pages it ended up being but I wanted to keep it fairly concise and focused. There were a lot of other things I realized I had to say. There were notes, scraps of paper all over the desk and a lot of unused things. I started thinking more that I wouldn't mind an alternative means of getting those ideas out there but also hopefully getting a dialogue started about this. I do think management and leadership are so key to what we're talking about.
If you look at so many Lean initiatives that have not succeeded the way that they could, you have to look at leadership management issues as being central to that. There's a dialogue that needs to be taking place out there. With blogging, you've done a great job, as a few others have, of bringing blogging into the Lean dialogue. I was a little scared of it. I haven't read that many blogs. It is a corner in the LEI website. We're calling it John's Lean Management Column. It's somewhere in between a traditional magazine column and a blog.
If you look at so many Lean initiatives that have not succeeded the way that they could, you have to look at leadership management issues as being central to that. Share on XWe didn't solicited a whole lot of feedback for the first couple of times. Talking with you and reading your blog, I'm getting a little more comfortable with the idea. It's a great new venue for exchanging ideas and getting ideas out there. It's exciting. I'm slowly getting used to the idea and dipping my toe in the water but it has been fun. We've done a few. I'm planning on putting one column out there and we'll see how people respond.
People reading this can go to www.Lean.org/Shook and find the columns there. That's a nice addition to the Lean web world. Words like this are rolling off your tongue, words like the blogosphere. I don't even like saying that. Welcome to the blogosphere. Thank you more so for your continued sharing of your learning back to Toyota days and everything you've been doing since. I learn a lot from it and I know others do too. Thank you for that.
Thanks, Mark. I look forward to your ongoing handholding as I get used to the blogosphere and everything. I appreciate that. Thank you.
Important Links
- Lean Enterprise Institute
- Learning to See: Value-Stream Mapping
- Managing to Learn
- Lean.org/Shook
- Managing to Learn: Using the A3 Management Process to Solve Problems, Gain Agreement, Mentor, and Lead – Amazon
- About A3s (via John's blog)
Please scroll down (or click) to post a comment. Connect with me on LinkedIn.
Let’s work together to build a culture of continuous improvement and psychological safety. If you're a leader looking to create lasting change—not just projects—I help organizations:
- Engage people at all levels in sustainable improvement
- Shift from fear of mistakes to learning from them
- Apply Lean thinking in practical, people-centered ways
Interested in coaching or a keynote talk? Let’s start a conversation.
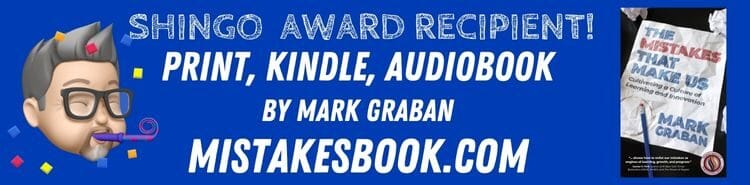