I stumbled across a piece Richard Feynman spoke some time ago about “Cargo Cult Science” and couldn't help but extend the analogy to “Cargo Cult Lean”, or as Mark's named it, “LAME: Lean as Mistakenly Executed.” First off, what is a cargo cult? From Feynman:
“In the South Seas there is a cargo cult of people. During the war they saw airplanes with lots of good materials, and they want the same thing to happen now. So they've arranged to make things like runways, to put fires along the sides of the runways, to make a wooden hut for a man to sit in, with two wooden pieces on his head like headphones and bars of bamboo sticking out like antennas – he's the controller – and they wait for the airplanes to land. They're doing everything right. The form is perfect. It looks exactly the way it looked before. But it doesn't work. No airplanes land…they follow all the apparent precepts and forms of scientific investigation, but they're missing something essential, because the planes don't land.” But it doesn't work.”
Sound familiar? We tried Quality Circles, we've tried Just In Time. We've disassembled our traditional inspection-based quality control (but often fail to put in place systemic error proofing). We've kanban-ed and level-loaded. Some have even gone to the gemba once or twice, you know, when the high priced Japanese consultant was in town. We've done everything that is necessary to be lean, but what we have done is not sufficient. Feynman elaborates with his analogy to the scientific community:
“Now it behooves me, of course, to tell you what they're missing. But it would be just about as difficult to explain to the South Sea islanders how they have to arrange things so that they get some wealth in their system. It is not something simple like telling them how to improve the shapes of the earphones. But there is one feature I notice that is generally missing in cargo cult science. That is the idea that we all hope you have learned in studying science in school – we never say explicitly what this is, but just hope that you catch on by all the examples of scientific investigation. It is interesting, therefore, to bring it out now and speak of it explicitly.”
Feynman goes on to write about rigorous scientific method and the critical importance of scientific integrity. I will write, you guessed it, about the importance of respect for people in the lean enterprise. Respect for people, eliminating what Norm Bodek has called the “eighth waste”, is that element of lean that we're expected to pick up along the way, but rarely understand or appreciate for its importance. We rarely talk about it explicitly in the workplace.
In my work, we have started to scratch the surface of a Training Within Industry initiative. We reached a perfect storm situation when two safety near-misses resulted in scrapping parts and damaging machines. In both cases, the operators had only short time on the job. Proper basic training, we realized, can prevent injuries, reduce our scrap rates, and reduce our machine downtime. So why, then, is it such an uphill battle to get time allocated to detailed basic training? The training is directly linked to some of our facility's most basic challenges and the most basic expression of Respect for People. And for that matter, why is Respect for People so consistently the missing link in lean efforts?
Let's face it, the LAME Cargo Cult approach is much easier. As we started doing Job Breakdown Instructions, I realized that our quality planning was far from standardized. With a dominant “mixed model” in our shop, standard approaches would allow an operator trained in one operation on one part number to learn the dozens of others that they need to know quickly. Unfortunately, that standardization would require hours upon hours of rewriting operation sheets and recoding and debugging NC programs. It's much easier to drain the inventory and blame the “bad operator” when a machine crashes and a delivery date is missed. Cargo Cult LAME says that we did all the right things, but we didn't get the right results.
Still, eyes are opening. Cynics abound, recognizing the cult for what it is. And a few people, lean realists, are starting to ask:
- if we wanted to train people correctly, and
- if we wanted to respect them for their capabilities and what they bring to the table,
…how exactly would we go about doing it? It's up to those of us not seduced by the false promise to keep preaching, keep teaching, and continue to do better at it every day.
Subscribe via RSS | Lean Blog Main Page | Podcast | Twitter @MarkGraban
Please scroll down (or click) to post a comment. Connect with me on LinkedIn.
Let’s work together to build a culture of continuous improvement and psychological safety. If you're a leader looking to create lasting change—not just projects—I help organizations:
- Engage people at all levels in sustainable improvement
- Shift from fear of mistakes to learning from them
- Apply Lean thinking in practical, people-centered ways
Interested in coaching or a keynote talk? Let’s start a conversation.
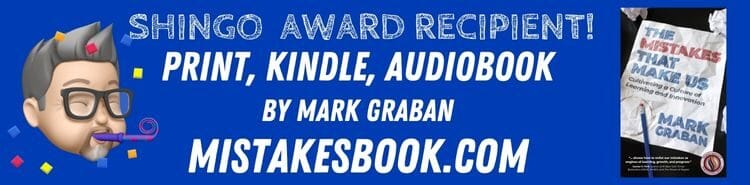
Your post resonates with my work situation precisely. Now if only I could find a way to get this into the inboxes of upper management here. I know… “Keep preaching.”
Thanks!