It has been a while since I've collaborated with artist Ed Butler on a “Doofus and Leanie” cartoon (Ed was also the artist for Wii Lean and the satirical “Lean Sensei” app. The recent reactions of GM (layoffs) and Toyota (no layoffs) to the production shutdowns caused by parts shortages caused by the Japan earthquake and tsunami couldn't be any more polar opposites of each other. Hence the following cartoon.

Cartoons can be accessed via www.doofusandleanie.com, which forwards to its own blog with its own RSS feed if you want to follow them specifically. As always, click for a larger view.
Text by Mark Graban, Artwork by Ed Butler:
HELL BOUND www.hellboundcomics.com
ILLUSTRATION ww.edbutlerillustration.wordpress.com
Please scroll down (or click) to post a comment. Connect with me on LinkedIn.
Let’s work together to build a culture of continuous improvement and psychological safety. If you're a leader looking to create lasting change—not just projects—I help organizations:
- Engage people at all levels in sustainable improvement
- Shift from fear of mistakes to learning from them
- Apply Lean thinking in practical, people-centered ways
Interested in coaching or a keynote talk? Let’s start a conversation.
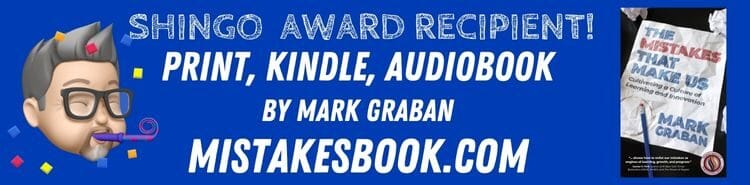
[…] Liker could point out that Lean is not about layoffs and that Toyota invests in people (as you can illustrated in my latest Doofus and Leanie cartoon). And, yes, even healthcare is getting into the Lean […]
Great article about Toyota utilizing people during the plant shutdowns:
http://www.industryweek.com/articles/staying_true_to_the_toyota_way_during_the_recession_24322.aspx?ShowAll=1
“Mr. Cho told me, ‘Always remember that management should work for team members, instead of team members working for management. We should always show respect for every individual, and we need to make sound decisions locally because no one knows what’s best for your team members in your own culture better than you,'” James recalled. “And I’ve never forgotten that, and I’ve patterned my management style to demonstrate my belief in that simple truth.”
and more practically:
And during production lulls, Toyota kept employees busy by offering additional training, devoting time to continuous-improvement projects and providing them paid time off to volunteer in the community, James said.
“We also used the downtime for environmental, OSHA and diversity training as well as improving problem-solving skills and standardized work,” James said.
Another example from Wales:
http://www.bbc.co.uk/news/uk-wales-north-east-wales-13264211
The company has said the remaining non production time will be “utilised for continuous improvement and training activities”.