Scroll down for how to subscribe, transcript, and more
My guest for Episode #531 of the Lean Blog Interviews Podcast is Dr. Melisa Buie, a seasoned operations and engineering leader with decades of experience in high-tech manufacturing.
Melisa has held senior roles at companies like Lam Research, Applied Materials, and Coherent, where she led large-scale Lean transformations and helped drive cultural change across global operations. With a PhD in nuclear engineering and plasma physics, Melisa brings a rare combination of technical depth and people-centered leadership to her work.
In this episode, we explore Melisa's Lean journey — from her early days in Six Sigma to becoming a global Lean leader at Coherent. She shares how her perspective shifted from project-based improvement to empowering teams with daily problem-solving skills. Melisa discusses the critical role of psychological safety in building a continuous improvement culture, and how giving people “permission to improve” must be backed by leadership behavior and support. We also touch on the challenges of applying Lean principles in complex, low-volume/high-mix manufacturing environments and why principles still matter more than tools.
“We're trained very early on that failure is not okay… we don't celebrate that. And so we've got to retrain ourselves to think about these mistakes and failures in a different way.”
We also discuss Melisa's book, Problem Solving for New Engineers, which is written to bridge the gap between academic preparation and the real-world challenges engineers face in industry. She previews her upcoming book, Faceplant: Free Yourself from Failure's Funk, which tackles the emotional side of failure and how we can grow through it. Whether you're a Lean leader, a coach, or an engineer just starting out, this episode is packed with valuable insights on leadership, learning, and making improvement accessible for everyone.
Questions, Notes, and Highlights:
- How did you first get involved with Lean or Six Sigma?
- Which books influenced you early in your Lean journey?
- How did your company shift from project-based Six Sigma to a Lean culture?
- Where did the push for culture change come from–top-down or grassroots?
- What role did you play in leading Lean at Coherent?
- What does it mean to “give people permission to improve,” and why is that necessary?
- How do leaders create psychological safety to support continuous improvement?
- How did your background in nuclear engineering and plasma physics lead to a career in semiconductors and lasers?
- How do Lean principles apply in low-volume, high-mix environments?
- What inspired you to write Problem Solving for New Engineers?
- How does the book help bridge the gap between university labs and industry problem solving?
- Why is experimentation and scientific thinking often missing in workplace culture?
- How do you explain the value of iterative cycles like PDSA to new engineers?
- What is design of experiments (DOE), and how does it improve problem solving?
- When is it helpful to let people run experiments with predictable outcomes?
- How did your second book, Faceplant: Free Yourself from Failure's Funk, come about?
- Why do people fear failure in personal life but accept it in professional settings?
- How can we reframe failure as a learning opportunity rather than something to avoid?
- How do you personally deal with failure and setbacks, like learning a foreign language?
This podcast is part of the #LeanCommunicators network.
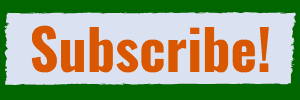
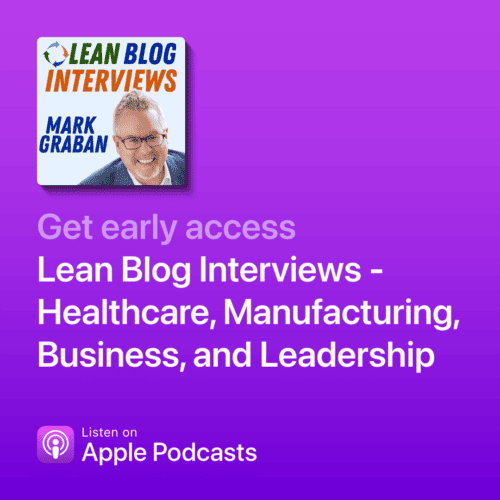
Full Video of the Episode:
Thanks for listening or watching!
This podcast is part of the Lean Communicators network — check it out!

Automated Transcript (Not Guaranteed to be Defect Free)
Mark Graban:
Hi. Welcome to Lean Blog Interviews. I'm your host, Mark Graban. Our guest today is Dr. Melisa Buie. She is an experienced leader in operations, engineering, and manufacturing transformation.
She's worked in senior roles at companies including Lam Research, Applied Materials, and Coherent, where she spent over 15 years solving problems and making lasers — so that's kind of a cool thing. Before I tell you more about Melisa, thanks for joining us on the podcast. How are you?
Melisa Buie:
I am well. Thanks for having me, Mark. I appreciate being here.
Mark Graban:
Yeah. We'll probably talk more about your operations and Lean and leadership experience than the lasers, if that's all right.
Melisa Buie:
That's perfectly fine.
Mark Graban:
Okay. Melisa has a PhD in nuclear engineering and plasma physics from the University of Michigan. She taught materials science at San Jose State University for a decade. She's a Six Sigma Black Belt, has co-authored over 40 journal articles and publications, and holds six patents. I think some of the things we'll talk about today include two books.
She's the author of Problem Solving for New Engineers and the upcoming book coming out later this year called Faceplant: Free Yourself from Failure's Funk. And with Problem Solving for New Engineers, you had some co-authors, right?
Melisa Buie:
No, that was a solo — misremembering there. Yes, that was solo. Faceplant has co-authors.
Mark Graban:
Well, I just demonstrated a faceplant unintentionally — but no need to edit that out. The solo book, Problem Solving for New Engineers. Before we talk about problem solving and some of the things you've done, Melisa, I love to ask people their Lean origin story. Or maybe it was a Six Sigma origin story. I'd love to hear the when, where, why, and how you got involved with improvement.
Melisa Buie:
Yeah. So my introduction to Lean was through Six Sigma. I started out being really curious about all the statistics. As a math major, I was super excited to know we could apply that in industry. So I ended up doing a Green Belt and then a Black Belt, and did some really cool projects saving a ton of money.
But our company decided at some point that we were going to go in the direction of Lean and really invest in building a Lean culture. And I thought, “Well, I know Lean — I did that Lean Six Sigma thing.” But it turned out there were like two minutes of Lean in the whole Six Sigma thing I studied.
Mark Graban:
That's pretty typical.
Melisa Buie:
Yeah. So I started doing a lot of reading and was really, really surprised by — not necessarily the tools — but the people side of Lean, and I really fell in love with it after starting to engage more deeply.
Mark Graban:
Do you remember which books were early influences?
Melisa Buie:
A book I've read multiple times and still go back to as a reference is Katie Anderson's Learning to Lead, Leading to Learn. Not because it teaches Lean tools — it doesn't — but for the power of reflection and how brave she and Isao Yoshino were in sharing failures. That was eye-opening and very impactful to me.
Mark Graban:
I hear you talking about shifting from projects to culture — and from cost savings to a broader focus. Where was that push coming from? Was it senior leaders taking the company in that direction?
Melisa Buie:
With Six Sigma, it's very project-based. You gather a team, pick a project, go through a formal process. With Lean, you're just making things better every day. That was a big mindset shift we were trying to instill.
It wasn't, “You need weeks of training before you can do Lean.” It was: “Just make something better.” Give your team permission to improve things. Let them say, “Hey, we can do this better,” without being punished for pointing out a problem. That culture shift fascinated me.
Another book that helped was 2 Second Lean by Paul Akers. We got copies for everyone — just a couple minutes a day to make things better.
Mark Graban:
Paul was a guest on the podcast too. What was your role during this Lean awakening?
Melisa Buie:
I was at Coherent then. They're a photonics company — we made lasers. I started as Director of Operations. Our VP of Operations held a Global Operations Conference and formed an Operations Council. From that, we created a steering committee focused on Lean.
Eventually, I led that steering committee for North America and then stepped into the global leader for Lean across the company.
Mark Graban:
A lot of companies use the SQDC framework — Safety, Quality, Delivery, Cost. Did that help broaden the focus from just cost savings?
Melisa Buie:
Yes. We already had a strong safety culture, and leadership was very committed to keeping our people safe. That foundation made Lean easier to adopt. Even though cost was important, it wasn't the only thing. We had delivery, customer focus — and all of that was already part of our culture.
Mark Graban:
So with that foundation, Lean likely resonated better. And giving people permission to improve — how did you help open that up?
Melisa Buie:
We engaged with every employee — not formal training, but conversations. We talked about the importance of what we did and the impact we had in the world. That helped people connect to purpose and feel empowered to make things better.
Mark Graban:
Your academic background is fascinating — PhD in nuclear engineering and plasma physics. Was that the path into semiconductors?
Melisa Buie:
It started with a big goal. In the '80s, we were worried about the energy crisis. Fusion was the clean, safe energy of the future, and we all wanted to be part of it. Fusion is taught in nuclear engineering departments, so that's what I studied.
But fusion was always “25 years away.” When I started, it was 25 years away. When I finished, it was still 25 years away. It still is. But I loved being part of solving a big problem.
Mark Graban:
And then semiconductors were booming. Lam and Applied Materials make the tools that companies like Intel use, right?
Melisa Buie:
Yes. Lam Research and Applied Materials are equipment suppliers to companies like Intel, Micron, Samsung, and TSMC.
Mark Graban:
So fusion led to plasma, which led to semiconductors?
Melisa Buie:
Exactly. I was studying plasma anyway, and the industry was just adopting tabletop plasma reactors to make more uniform computer chips. I got a manufacturing scholarship from IBM for my PhD and pivoted into semiconductor manufacturing.
Mark Graban:
Intel has focused on Lean and Six Sigma over the years. Did you encounter resistance to applying Lean in high-tech environments where people say, “We're not Toyota — we're different”?
Melisa Buie:
Yes, that's common. In both the semiconductor and laser industries, we were doing low-volume, high-mix, highly customized work — very expensive equipment. But the core Lean principles still apply. You may need to adapt the tools, but the mindset and cultural elements translate really well.
Mark Graban:
Right. Problem solving is universal. Whether it's semiconductors or healthcare, smart people can figure out how to apply it to their context.
Melisa Buie:
Absolutely. I've learned from food manufacturing, chemical industries — the tools may vary, but the principles are broadly applicable.
Mark Graban:
Let's talk about your book Problem Solving for New Engineers. How did it come about?
Melisa Buie:
It came out of my experience teaching at San Jose State while also hiring many new engineers in my industry roles. I realized that in academia, students weren't being prepared for real-world problem solving. University labs are very prescriptive — follow steps, get expected results.
But in the real world, you don't always know what to look for. You need to make observations, test hypotheses, and figure things out. I wanted to bridge that gap and provide a tool that helps new engineers apply their subject-matter knowledge in a structured way.
Mark Graban:
That's such an important gap. In the workplace, leaders often crave certainty — they want solutions, not experiments. How do you help new engineers navigate that?
Melisa Buie:
Many engineers are trained to change one factor at a time because they're afraid to confound results. But we don't teach design of experiments (DOE) early enough — how to work with variation, how to model process spaces.
Once I learned DOE — and I didn't learn it until I was in industry, after my PhD — it opened a whole new world. I looked back at my PhD work and thought, “Oh no, all those one-factor experiments!” But that's where we all start.
Mark Graban:
Somebody in the Kata community once said, “If you know the outcome, it's not really an experiment.” What do you think about that?
Melisa Buie:
I agree — but I also think that even if the outcome is known to someone else, if it's new to you, it's still a meaningful discovery. There's huge value in learning through your own experiment — even if it's to validate something others already understand.
Mark Graban:
Right. Like if someone runs an experiment to cut batch size in half, and we know it'll reduce lead time — but they experience it firsthand, they own that insight.
Melisa Buie:
Exactly. One example I love: I visited a Lean company that used U-shaped cells. One day, they were short a person. A frontline group leader redesigned the cell for the day and ran an experiment to hit their target. No PhD, no engineering degree — but she had permission and knew how to experiment. That's real empowerment.
Mark Graban:
That's such a powerful example. And leadership was willing to accept the risk that it might not work?
Melisa Buie:
Right. They knew being short-staffed already meant risk. Running an experiment gave them a shot at hitting their goal. That's what Lean culture looks like in action.
Mark Graban:
You mentioned DOE — which I admit I'm rusty on. Is it fair to say DOE is a smart way to test multiple variables at once?
Melisa Buie:
Yes! DOE helps you identify which factors impact your response variable and whether there are interactions. It helps you model your process space instead of just guessing. You can do more with fewer trials — and it's an incredibly powerful tool when used well.
Mark Graban:
Let's talk about your upcoming book Faceplant: Free Yourself from Failure's Funk. How did that one come to life?
Melisa Buie:
It started from a personal observation. In labs, I was comfortable with failure — I knew I'd learn and adjust. But in personal life? Total fear of failure. I asked, “Why do I feel safe failing professionally but not personally?”
So I started a big experiment — journaling, reading about failure (including your book and Amy Edmondson's), and then inviting colleagues into the discussion. At first, they said, “Why would we want to talk about failure?” But soon we were all sharing deep, emotional stories. That's when I knew there was something powerful to explore.
Mark Graban:
It reminds me of Edmondson's concept of intelligent failure. We want to be thoughtful, not reckless — but we also want to fail small and learn.
Melisa Buie:
Exactly. Start with small experiments, be curious about the outcomes, and don't assume the worst if things don't work out. It doesn't mean you've failed as a person. We can recover, reflect, and grow.
Mark Graban:
Was there a personal example of failure that stuck with you?
Melisa Buie:
Yes — trying to learn Spanish as an adult. I proudly showed a written assignment to a native speaker friend, and she said, “This is like something a first grader wrote.” I was mortified. I stopped studying Spanish for years because I was so embarrassed. I totally shut down.
Mark Graban:
You brought that funk on yourself!
Melisa Buie:
I did. And that's the danger — when we internalize failure as shame, instead of treating it as part of the learning journey.
Mark Graban:
The surest way to never fail is to never try something new.
Melisa Buie:
Right.
Mark Graban:
Well, I'm really looking forward to Faceplant. And I hope you'll come back on My Favorite Mistake to talk about one of your own faceplants — maybe the Spanish one!
Melisa Buie:
I'd be happy to. Absolutely.
Mark Graban:
Thanks so much for joining us and sharing your story. Again, our guest today was Dr. Melisa Buie. Her book Problem Solving for New Engineers is available now, and Faceplant: Free Yourself from Failure's Funk is coming soon — likely in November.
Melisa Buie:
Thanks again, Mark!
Please scroll down (or click) to post a comment. Connect with me on LinkedIn.
Let’s build a culture of continuous improvement and psychological safety—together. If you're a leader aiming for lasting change (not just more projects), I help organizations:
- Engage people at all levels in sustainable improvement
- Shift from fear of mistakes to learning from them
- Apply Lean thinking in practical, people-centered ways
Interested in coaching or a keynote talk? Let’s talk.
Join me for a Lean Healthcare Accelerator Trip to Japan! Learn More
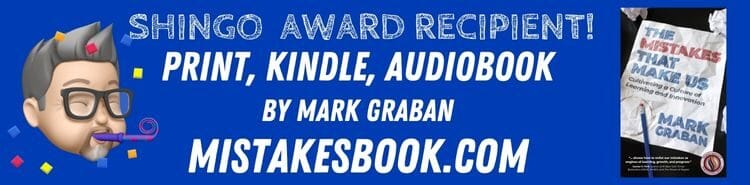