Thirty years ago, I was fresh out of college and working at General Motors. Yikes! 30 years!
It was a time of reckoning–GM was finally acknowledging it needed to catch up to Toyota. Not just in production techniques, but in how they managed.
Toyota's approach was different. Their joint venture with GM–NUMMI in Fremont, California–offered a firsthand look at a system built on principles that would later be labeled “Lean manufacturing.” But for Toyota, it was never just about tools or cost–it was about the Toyota Production System (TPS) as a holistic management philosophy.
Back then, I was introduced to the acronym SQDC: Safety, Quality, Delivery, and Cost. It was meant to reflect balanced priorities. But in practice? The focus far too often defaulted to cost.
Cost-cutting became the primary objective.
Sadly, safety, quality, and delivery were things that could (and did) suffer as a result.
That pattern still echoes in many industries today–including healthcare. I've seen hospitals embrace cost-saving initiatives while skipping over the foundations that actually make those savings sustainable:
engaged staff, a culture of safety, and high-quality care.
Toyota didn't lead with cost. Yes, cost matters. But, they focused on building capable systems and developing people. Costs were managed, of course, but they were the result of better systems–not the starting point.
Here's the irony:
When we chase cost first, we often compromise the very things that drive long-term performance.
But when we prioritize safety, quality, and delivery–when we respect people and engage them in problem solving–cost takes care of itself. Cost is an end result of doing everything else well.
I recently discussed this on THE Podcaster Nation with Rory Paquette. Here's a 60-second clip from that episode:
If you've seen this pattern–cost trumping everything else–I'd love to hear your thoughts. And if you're working in an organization that's doing SQDC well, even better.
Let's keep learning and leading forward.
Related Posts:
Please scroll down (or click) to post a comment. Connect with me on LinkedIn.
Letās build a culture of continuous improvement and psychological safetyātogether. If you're a leader aiming for lasting change (not just more projects), I help organizations:
- Engage people at all levels in sustainable improvement
- Shift from fear of mistakes to learning from them
- Apply Lean thinking in practical, people-centered ways
Interested in coaching or a keynote talk? Letās talk.
Join me for a Lean Healthcare Accelerator Trip to Japan! Learn More
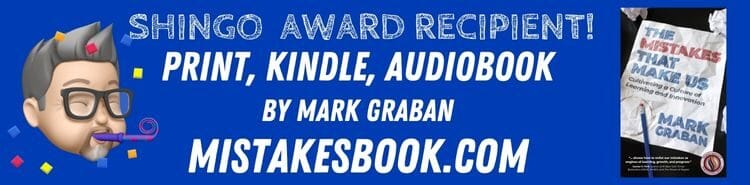