Listen:
In Episode 44 of the Lean Whiskey podcast, Jamie Flinchbaugh and Mark Graban get back together for this first episode of 2024.
Since we're not doing Dry January, we go right into the whiskey first by talking about old bottles, including one very old one found at auction. We then did our own comparison tasting, with Jamie trying two different age statements of Knob Creek bourbon and Mark trying two different expressions of Glen Scotia scotch from Campbeltown.
Dry January is like a New Year's Resolution that you don't intend to keep past a month. We discuss New Year's Resolutions and their reasons for failure. We relate all this to goals, hoshin kanri, SMART goals, systems, and small steps. So, if you're still working on clarifying your goals or resolutions for the year, take a listen.
Boeing's recent troubles with an Alaska Airlines 737 MAX-9 door plug falling out mid-flight was also discussed, including Boeing's resolution / commitment to add more inspectors to the process. Will more inspectors and more inspections make a difference? If not, what will make a difference? We may not know the final answer, but we break it all down for you in this discussion.
We wrap things up with a little football talk, both the NFL and College. Cheers!
Links From the Show:
- Vintage bottle sold at auction, from York, PA
- Jamie's selection: Knob Creek
- Mark's selection: Glen Scotia
- NPR on abandoned New Year's resolutions
- Jamie's 2010 blogpost on goals
- Jamie's 2021 short video on working with goals
- Boeing's own updates on the 737-9
- On Senator Cantwell's letter to the FAA
- Yup, University of Michigan wins the National Championship
- Podcast feed at LeanWhiskey.com or leanblog.org/leanwhiskey or jflinch.com/leanwhiskey
Please review us and follow or subscribe on your favorite podcast platform!
Video:
Subscribe, Rate, and Review!
Please check out the main LeanWhiskey.com page if you want to subscribe via Apple Podcasts, Google Podcasts, Stitcher, Spotify, or RSS. Please rate and review the podcast too!
Cheers! If you have any feedback or ideas for the podcast, let us know!
Find the podcast feed and past episodes at LeanWhiskey.com or at leanblog.org/leanwhiskey or at jflinch.com/leanwhiskey
Please review us and subscribe or follow us in your favorite podcast directory or platform.
Transcript of the Boeing Discussion Section:
Jamie Flinchbaugh:
Speaking of making resolutions, there's one company that probably needs a few.
Mark Graban:
Seems like they're making a few seems like they're making shouldn't happen just because of the first of the year. But at Boeing, speaking of in the news, after the January 5 incident with the Alaska Airlines plane where 737 Max nine had what they call a door plug, that was a new term for me. A door plug basically blew out at 16,000ft, and thankfully the plane landed safely. Nobody was killed. There were some injuries, I think relatively minor injuries.
Mark Graban:
But it seems like Boeing's New Year's resolution is to do more inspections. So I'm going to give a little bit of a recap of some of this aftermath that's been in the news here this week and a memo that was published by Boeing on their website. We can link to it in the show notes. Their commercial airplanes president and CEO, Stan Deal, is talking a lot about inspections. I haven't heard anything about mistake proofing or prevention, but just give quick recap. Here's their action plan.
Mark Graban:
It includes more quality inspections, planning additional inspections. At Boeing and Spirit AeroSystems , that's the separate company, formerly part of Boeing that makes the fuselage. So it's one more layer of scrutiny on top of the thousands of inspections performed today. Since 2019, we have increased the number of inspectors by 20%. And then they talk about doing more inspections at Spirit.
Mark Graban:
Not just the bolts on the door plug, but 50 other points in the build process. And nobody knows yet if Spirit built it wrong to begin with or if the company that took the door plug out to install the Wi-Fi system did not put it back in. But people say ultimately Boeing is still responsible for that. But the FAA is going to be doing audits. There's going to be outside assessment of Boeing assembly practices.
Mark Graban:
They are welcoming inspectors from the airlines. And I wonder now if the inspectors are going to be just tripping over each other, how many people can be simultaneously inspecting if those bolts have been tightened properly. What's your first reaction to some of that, Jamie?
Jamie Flinchbaugh:
Well, the first thing is that it takes time to study systems problems and develop. I don't want there to be an answer yet. You can't put 200 people on this problem and get to the answer faster. It should be well studied, researched scientifically, observationally, and we should take our time getting to what really went on. So that's my first reaction.
Jamie Flinchbaugh:
Second is that if we can't get to the root cause, then inspection is at least a stopgap at best, but a stop gap. And so I don't think inspections are inherently bad when we know a system is failing. Right. So, you know, if. If traffic lights aren't working, sticking a police officer at the intersection isn't a bad idea.
Jamie Flinchbaugh:
Right. We know that the real system is broken, so we're going to put something in place that ensures bad outcomes. Don't.
Mark Graban:
You're making me think about the risk of trying to mistake-proof that by having some barricade that pops up from the ground when the light turns red. Society has decided not to mistake-proof running the red light because sometimes police and fire need to. But, yeah, sometimes I think if you can't or if you haven't figured out how to mistake-proof it yet, inspection like you said, is a stopgap. But inspection, especially if it's done by humans, is imperfect as well. So I wouldn't want to completely hang my hat on more inspections.
Mark Graban:
And if double inspections are good, why not triple inspections? And how many more inspections would make that not have anything fall through the cracks?
Jamie Flinchbaugh:
Well, I think you said inspectors would increase by 20%. That basically says, well, is that all inspections will get 20% more scrutiny. Are we going to triple our inspections of door plugs, mathematically decrease our inspections of other things? We don't know if this, and this goes back to root cause and systems understanding, we don't know if this is a door plug issue, a fuselage issue, or a general assembly issue or a service issue. Increasing inspectors by 20% at least ensures probably that missing planned inspections is going to be less likely.
Jamie Flinchbaugh:
Don't know if that's contributed at all. But just, hey, there's never enough resources, and at least we'll do what we plan to do. If we have more inspectors.
Mark Graban:
There's doing the inspections. But then some of the discussion from former Boeing people who are involved in legal action because they're filing suits, saying they were wrongfully fired for being whistleblowers or speaking up about quality issues. I mean, it gives me flashbacks to 1995 at General Motors, where people would do the inspections and then management would overrule the decision to stop the line because of a quality problem. “Quantity over quality” or “schedule is king” kind of mindsets. Or back at General Motors, literally telling people to not take the time to do the inspections.
Mark Graban:
Management would roll the dice with quality. And there are people who make accusations around, like, well, quality inspectors who are raising issues would get reassigned. It will bring in a contractor, we'll bring in another inspector. I mean, there's a whole layer of alleged management decisions that I wouldn't describe as a worker problem or not to rant too much, but I read a piece on the Slate online website. This guy thought he was being funny, but he said something about like, well, I fly a lot, and I always figured there's a chance I might die in a crash.
Mark Graban:
But I'm paraphrasing here, but I didn't want it to be because some idiot didn't tighten the bolts. I'm like, whoa, whoa, whoa, whoa, whoa, whoa. It's not some individual idiot. It's more complex than that.
Jamie Flinchbaugh:
Well, certainly because multiple airlines found the problem. So that, by definition, is likely not the case. I do think compared to that GM in the 80s scenario, 90s, I'm not that old. It was much more common in the 80s, right? The auto industry was heat it, beat it, and ship it.
Jamie Flinchbaugh:
That was just get through. I think it's pretty rare. I'm not saying Boeing isn't guilty of this. I'm saying it's pretty rare that companies today knowingly sacrifice quality for delivery. I think it's pretty well accepted as just an ethos of even good profitability that you will be found out with bad quality.
Jamie Flinchbaugh:
So don't cut that corner. Every one of us can have a bad moment. But I think what used to be like production was there to ship it and quality was there to hold them accountable. I think a lot of that is those days are largely over. But there's an exception to everything doesn't mean that this isn't that exception.
Jamie Flinchbaugh:
The other thing is when we start to look at causes, I want to say the vast majority, but the majority of the time, when you have a systematic problem like this, it's not even assembly, it's design. And I have not read everything on this partly by intent. We don't know squat.
Mark Graban:
I think the experts are saying for now, it's not a design flaw. It's at some point an assembly defect or a reassembly defect, because there are some people saying, if you look at the value stream, Spirit AeroSystems , formerly Boeing, assembles the fuselage, which includes the door plug on planes that have the door plug instead of another emergency exit, because they don't have enough seats on the plane to require the emergency exit. It's shipped by rail to Boeing. Now, some have said they take the door plug out to give another access point to do the interior assembly, which sounded credible. You got to put in seats and.
Jamie Flinchbaugh:
All this other stuff.
Mark Graban:
And more access points would probably streamline and speed up assembly in a good way, assuming the door plug is then reinstalled back to original specifications. But then there's the dimension of a different third party vendor that supposedly takes the completed plane and installs the thing everybody wants, which is wi-fi, that that company takes the door plug out to do their wiring and installation. So it could be a possibility. Well, I mean, even if Spirit had assembled it and tightened it incorrectly, the door plug wouldn't fly out when it's traveling by rail, probably. And then there's that other company involved, and then Boeing is supposed to do the final sign off.
Mark Graban:
So it's complicated by different companies being in that value stream.
Jamie Flinchbaugh:
Right. But even from a. So we talk about product design and process. Right? So you kind of go, did somebody make lots and lots of mistakes over many aircraft?
Jamie Flinchbaugh:
Or was there a product design or a process design problem? Right. If there was a process design failure where we're taking out a plug, putting it back in, there's no spec for how to do that. That's a process design problem. Right.
Jamie Flinchbaugh:
Again, looking at how are we doing assembly versus how are we designing the process, that's where this is worth taking the time to get to root cause, because something that's happened to this many units is very rarely just random mistakes.
Mark Graban:
Yeah. I don't know if we know how many planes have been affected. They've grounded them and they're inspecting them, I think for good reason, because on the plane in question, with the Alaska Airlines flight, they did inspect the right side of the plane door plug, and that had been done properly. Right. So this one plane, that one door plug, could be a one-off freak occurrence, or it could be indicative of a common problem.
Jamie Flinchbaugh:
Right. But that's where other airlines, like, I believe united, have found other loose faults on the same door.
Mark Graban:
Oh, okay.
Jamie Flinchbaugh:
Thank you. So that's the fact, that's the data that suggests there's a pattern. Right. So it's not random variation in December.
Mark Graban:
Right. But then while we have. I'll frame it as an unreliable process that's not generating perfect product. I'd rather have the inspections than not. But then it raises a question of, is this a broader standard work issue?
Mark Graban:
Is this a bolt issue? Those are not the only bolts on a plane. Spirit AeroSystems has gotten in a lot of trouble for all kinds of manufacturing defects. It actually got a CEO fired last year. It just makes me wonder, back to the question of somebody that would blame an idiot worker, say, well, what about the standardized work?
Mark Graban:
What about the training? What about the supervision? What about the inspection process? What about the culture? I mean, there's so many other factors where some people, I think, would oversimplify and say, well, that person needs to just do their job.
Jamie Flinchbaugh:
Right.
Mark Graban:
Well, tightening a bolt is not hard, but if you're under pressure to speed up your work and you're not being listened to, and that suddenly gets more complicated.
Jamie Flinchbaugh:
Yeah. And that's, I think, super important around the difference between one-off problems and patterns of problems, and then also the effectiveness of inspections. If a mistake can happen anywhere in the process, the only way to inspect inequality is to inspect every step in the process, which is a one-for-one ratio. So we do have an instance where this exists, is in software. There's a concept called extreme programming, where I'll save all the details, but one person is coding while another person is inspecting real time.
Mark Graban:
Or like Menlo innovations, Rich Sheridan, they call it paired programming, which I think is part of the process. Right.
Jamie Flinchbaugh:
Yeah. So they didn't invent any of that. But you're getting, basically one person is on the keystrokes and the other person is there checking the code, looking for errors real time. Now, writing code, you're not following standard work. Right.
Jamie Flinchbaugh:
You're creating. So it's very likely. So it's a combination of very likely to have errors and harder to catch them afterwards. So let's invest two people for every one person's worth of work. By no means are we investing that much in inspection.
Jamie Flinchbaugh:
And so the only way inspection works is if we either know what to. Right. We know where the risks are and so we're putting our resources where the risks are, or we're looking at the system itself, which is really what the FAA should be doing, not actually inspecting aircraft, but looking at the system. And neither of those are inherently successful unless we know the root cause. So I'm not going to complain about more inspectors, but it doesn't mean we've contained the problem.
Mark Graban:
Right. And I'm not going to complain about it, but I will hope and trust that Boeing is also, as much as they've tried to embrace lean, which is all secondhand or thirdhand knowledge to me, I hope they're going to dig more into mistake-proofing. And I think the talk of inspections might be as much about optics and PR as it is quality, because I think people don't understand, you and I and people listening to this are going to understand these nuances of, like, well, sure, inspection versus better mistake proofing. And the general public is not clued into that.
Jamie Flinchbaugh:
No. And to be honest, because this wasn't a fatal accident, we're not going to be talking about this in a year. So just the news cycle isn't that patient.
Mark Graban:
It's fortunate that this happened at 16,000ft and not 36,000ft, some say.
Jamie Flinchbaugh:
Yeah, absolutely. And nobody was sitting at that particular.
Mark Graban:
Spot or the middle seat, which. And that was a pretty full flight, but not those two seats, which is always.
Jamie Flinchbaugh:
That's probably the row I would target, so probably what would happen to me.
Mark Graban:
But I don't think it was an exit row with your extra leg room for your bad knees.
Jamie Flinchbaugh:
No, but that's where upgrades come into play.
Mark Graban:
Yeah.
Jamie Flinchbaugh:
And this isn't making me want to return to my old days of flying every week, but, yeah, everybody wants to know, what are you doing? And you can't just say, we're problem-solving. Right.
Mark Graban:
Sure.
Jamie Flinchbaugh:
They want to know that you're doing something now. Protect the public. Which is interesting, because the flights are grounded, so adding inspectors isn't likely to say, lift. The flights being grounded for 737 nine. Right.
Jamie Flinchbaugh:
In a lot of ways, it's a containment of a problem that's already contained.
Mark Graban:
Yeah, in a way. But, yeah, there's the existing planes and the future production. And this is Boeings. The seven three seven in general is their highest volume product by far. The order numbers on the nine max aren't as high.
Mark Graban:
I don't think American Airlines, who I fly, has many of the seven three seven max. But after the previous problems and the two crashes, and I know I'm not alone and I'm going to start paying attention to, okay, what's the equipment? Where I thought, like, all right, well, the previous problem had been put to bed. But one other thing I was going to bring up, though, to the idea of inspection. As much as lean Dogma says inspection is waste, it's part of the waste of defects.
Mark Graban:
I've seen organizations get in trouble by taking that to heart and saying, okay, we'll get rid of our inspections. But because they don't have a capable process, that's mistake-proofed. Defects get to the customer like, well, that's worse. That's a worse waste than spending more on inspections. And sort of case in point, even though I'm with you to say inspections, a stop-gap or a short-term countermeasure, this surprises people sometimes when I say, well, look, I've been to Toyota plants in Japan and San Antonio and Kentucky, and what they all have is a big area with lots of bright lights and lots of people called final inspection.
Mark Graban:
For all the talk about building in quality and mistake proofing and judoka, they still have final inspection, because I think rather than falling on dogma, they're being practical and saying, look, we're still not producing perfect quality. Therefore, final inspection is a less harmful waste than letting defects get to the.
Jamie Flinchbaugh:
Yeah, absolutely. And I actually helped JD Power build their consulting practice to go into automotive manufacturing plants and look at how do you control quality? And I have a model called the four loops of quality, which looks at different layers of doing that. But this is also what's wrong with misunderstanding the idea of the seven types of waste, which is you identify the waste and then you identify the cause of the waste. Yeah, but you can't eliminate the waste without eliminating the cause.
Jamie Flinchbaugh:
So inspection is not one of the seven types of waste, by the way. But it might be wasteful. It's certainly not value added, but it might be necessary. Unless you've eliminated every defect. Right.
Mark Graban:
That's my point. It might be necessary.
Jamie Flinchbaugh:
Might be necessary, right.
Mark Graban:
Yeah.
Jamie Flinchbaugh:
Inventory is the same thing that have zero inventory until they improve their setup time or their uptime or their lead times or their yields or whatever it might be. Until they improve that, they can't reduce their inventory. So you see the type of waste, and then you go, what's the cause of that waste? And then you go, eliminate the cause. You don't just take out the waste.
Jamie Flinchbaugh:
The waste is a lens to find underlying problems. And that's all it is. And so, yeah, inspection is wasteful, but it's still necessary. It's still important. Until you can prove to yourself, let alone the FAA or the customers or anybody else, until you prove to yourself that you can do something absolutely defect free, especially when it's right.
Jamie Flinchbaugh:
And I argue, if you have customers, then whatever your work is, is important. I don't care if you're a marketing agency or you're selling gum or toothpicks or. It doesn't matter. Whatever it is, the customer cares. So until you can prove to yourself you can deliver to the customer without a defect, some inspection is always going to be necessary.
Jamie Flinchbaugh:
Yeah.
Mark Graban:
And I'll give Boeing credit. I haven't heard any talk around. Well, we fired the person who was responsible. I haven't heard any scapegoating. I mean, Dave Calhoun, the CEO, I think, in fairly plain language, admitted Boeing's made mistakes.
Jamie Flinchbaugh:
Know as much as an accident does, where half the time with an accident. Obviously, there's legal concerns with an accident, and nobody wants to claim culpability. This one's a little easier because damage isn't there and still going to be lawsuits. There already are lawsuits. Right?
Mark Graban:
There are for physical and emotional trauma.
Jamie Flinchbaugh:
Right. I don't know if that's warranted. I'm not going to even go there. But, yeah, they basically said, we need to figure this out. And I think they seem to be genuinely taking it on the chin where they acknowledge that this is unacceptable.
Jamie Flinchbaugh:
Their PR instincts may be also kicking in, but I don't think it's disingenuous. I do think it's genuine, but I'm also not sure they have the solution. Not sure they're there yet. Boeing has been doing lean for as long as almost any company in North America. But have they been doing it well?
Jamie Flinchbaugh:
And I don't have a lot of indicators to suggest they are. I think they spent a lot of time on cell design, they spent a lot of time on efficiency. They relied on external consultants forever. I'm not sure they ever truly owned it. And that flip from getting help to we own this, we get this, we're going to drive this, this is part of our DNA.
Jamie Flinchbaugh:
As long as they've been on this journey, I'm not sure they ever got there.
Mark Graban:
Well, I mean, there's a difference between implementing lean tools and doing things on the shop floor and really having more of a broad, lean culture that other companies are working. What a bunch of Kaizen events, a bunch of lean tools. They famously set up a moving assembly line for airplanes because I've heard it secondhand or third hand that a consultant pushed them to do that, as opposed to pulsing the plane, like moving it at a certain frequency, like continuously, very slowly moving assembly line, which I've heard this is in the realm of rumor, that the line only moved continuously when certain executives came to visit. Otherwise they ran it exactly like the old pulsed line. Superficial lean.
Mark Graban:
And to me, lean is not about moving assembly lines. It's more about culture and leadership and management style. And some companies don't get into that.
Jamie Flinchbaugh:
And fundamentally, I'll go back to this point, but for product this complicated, you can't be lean in manufacturing only. You have to get design there. And I don't know if they've ever really made any efforts there. There's very little that I've heard about sort of, I'll say lean product development or just bringing lean into the design culture. Heard lots about their manufacturing, their cells.
Jamie Flinchbaugh:
I once led an american machine tool builders group on a tour at Boeing, asked by the association to do that because Boeing wasn't buying their equipment, they were making their own. And so I did that as a favor to the association, but a lot of their lean efforts has been on manufacturing, and you can only go so far in manufacturing with a product that's complex. The fact is, and this is the same news we had when we were doing consulting in automotive plants with JD Power, which is, yeah, we can help you manufacture better, but if you're to improve quality, let's talk about design.
Mark Graban:
Yeah, the time will tell. I'm going to be flying on Friday. I don't know if it's going to be a Boeing 737 or Airbus A320 or 321, but you fly enough and you can't help but think about, like, well, I could die. Odds are really low, right?
Jamie Flinchbaugh:
The odds are very low. And fact that this happened, it's national news. And yet how many people died in car accidents today? It's not going to make the news that this did.
Mark Graban:
The drive to the airport is more dangerous.
Jamie Flinchbaugh:
Yeah, no question. Right. So when it comes to airline safety, we're still far from what we experience in automotive safety, airport healthcare safety or healthcare safety. There we go. But, yeah, I've always paid attention to the aircraft, mostly because it would tell me a lot about my seat and I like room, things like that.
Jamie Flinchbaugh:
But also, being an ex Delta, well, I guess still current, I just don't fly very much. But Delta and northwest, loyal customer, watching out for those DC nine flights was a big part of my life for.
Mark Graban:
A while to avoid those.
Jamie Flinchbaugh:
Oh, yeah. I've always hated the DC nine flights.
Mark Graban:
Yeah. But they always say, I mean, takeoff and landing are the most dangerous parts of a flight. So taking a nonstop flight reduces your risk of. I think I learned this from Arnie Barnett from MIT, our professor, statistics professor and aviation expert. Taking a nonstop flight, as opposed to a connection, cuts your risk in half.
Mark Graban:
Right. One time up, one time down. I just never occurred to me that you could be sitting there and have just part of the fuselage blow out. And it happened once, I think, at a Hawaiian Airlines flight a long time ago. It happens very rarely, but I don't think about that.
Mark Graban:
It's more of like, as we're taking off. And I still have the scars of growing up in Detroit. When the northwest Airlines flight crashed on takeoff because the flaps were set incorrectly, the plane couldn't get enough lift and it hit a light pole and it crashed and killed everybody on board but a very young infant who miraculously survived. But I think of things like that. I cringe on takeoff sometimes, like, are we getting enough lift?
Mark Graban:
But then once you get off the ground, you're like, oh, well, we're great as long as there's not a plane on the Runway when we land. That's the Japan Honda airport incident. That is now not in the news so much because of the Boeing incident.
Jamie Flinchbaugh:
Right.
Mark Graban:
Different human factors, different systemic factors.
Jamie Flinchbaugh:
But it's still a safe way to fly. A safe way to travel. It may be a frustrating way to travel these days, which is really why I avoid it, but it is still a very safe way to travel.
Mark Graban:
Well, if you weren't driving the Kentucky and back, we wouldn't get chances to hang out in person.
Jamie Flinchbaugh:
That's true. That's good, too. And those flights were always connection, so I had more chances to, not as many chances as I have at driving through the West Virginia mountains. All right. Well, we haven't solved it today, but neither have they.
Jamie Flinchbaugh:
But we can trust for now that they will take their time, get it right and make this problem go away. But there certainly seems to be some other underlying issues that are going to take a little more time. Yeah.
Mark Graban:
Well, I'll note we recorded this on Tuesday the 16th, and we'll probably release it, as we tend to do on a Friday, probably the 19th. So things changed in between. We apologize for being a couple of days out of date.
Jamie Flinchbaugh:
Sure. And while we're picking aircraft, let's remember that Spirit AeroSystems also supplies Airbus. So plenty of risk all around. Plenty of safety all around. Yeah.
Please scroll down (or click) to post a comment. Connect with me on LinkedIn.
Let’s work together to build a culture of continuous improvement and psychological safety. If you're a leader looking to create lasting change—not just projects—I help organizations:
- Engage people at all levels in sustainable improvement
- Shift from fear of mistakes to learning from them
- Apply Lean thinking in practical, people-centered ways
Interested in coaching or a keynote talk? Let’s start a conversation.
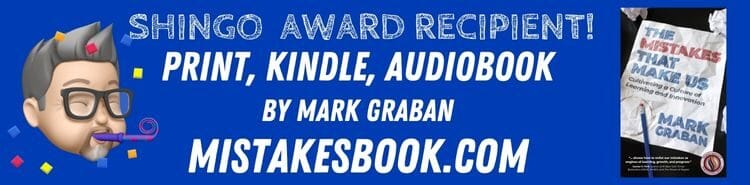