In my recent podcast with Ritsuo Shingo, one topic was the history of the acronym “SMED” — it stands for “Single-Minute Exchange of Die,” referring to how long it takes to do a “die change” on a machine like a stamping press. The “die” is the “tooling” that presses together to stamp the metal. This can also apply to the die in an injection molding machine, etc.
The concept and methodology can also apply to healthcare — such as improving the way we turn an operating room between patients as just one example.
The “single minute” part of that phrase has often been confusing to people. Does this mean the die change has to be done in one minute or 60 seconds?
Shingo-san talks about this in the episode, as you can read in this excerpt of the transcript (you can read the full transcript on the episode page).
tl;dr: “Single-minute” means a “single digit number of minutes.” That could mean “9 minutes or less” but it also just means “do it significantly faster than before.” And the idea comes from golf handicaps… even though the phrase might not be ideal, it's too late to change it?
Partial Transcript
Mark: One question I had going back to earlier. You said SMED was your father's concept, but the English words and the acronym SMED, that was your creation when you translated the book. Is that correct?
Ritsuo: Exactly speaking, I didn't create at all. [laughs] I was wondering what is the Single Minutes Exchange of Die? It's written in Japanese.
Mark: How do you say it? How do you say in Japanese?
Ritsuo: Single dandori. Dandori means the change of tool. I asked my father, why you called it single? It is in Japanese, Shinguru dandori. Shinguru dandori.
He explained to me, he learned how to play golf after 60 years old. He learned for amateur player, a single player, a single handicap is great, less than 10. He likes it.
Let's take that name to the quick change. Physically it doesn't mean within 10 seconds. No. What he meant was make it quicker. Quick change of die. Quick. To show the quickness, he liked to use single handicap.
After listening to his explanation, OK, if so we make it, I translate it, Single Minute Exchange of Die. That is SMED. I propose Single Minute Exchange of Die. He agreed. That's how we try to use SMED. Some American people told me it is not a good English as a grammar. It should be single-digit something.
Mark: Single-digit, yes.
Ritsuo: I answered, “Oh, too late already.” [laughs] I translate it Single Minute Exchange of Die. Single-digit? Can we say SDED? No, no, wait. SMED.
Mark: No. [laughs]
Ritsuo: Actually, Ken Snyder, director of the Shingo Institute called me, “Oh, Shingo some, there was something wrong.” I told him, “Too late. Too late.” Already everybody in the world is using the term SMED. It's just a name. At that time when I translated SMED, I didn't know whether the people in the world use it or not.
When I was in China, even in China, they use the term SMED. They understand the meaning itself, they don't understand what to do. The meaning SMED, wherever you go, Europe, US, Mexico, everybody understand SMED. I didn't translate. I just proposed and discussed with my father, and he agreed that this is SMED.
Mark: I was fortunate to have good teachers, who taught me the idea of single minute meant maybe nine minutes or five minutes. [laughs] Often people hear single minute they think one minute, and it doesn't strictly mean that. Maybe that's a misunderstanding.
Ritsuo: No, no. That 10 minutes, 20 minutes, very quickly. The processing is important. Concept is important. How to reduce the changeover time to become a quick changeover, that is important. As a result, sometime it could be 10 minutes, sometime it could be 20 minutes. It's OK. From three hours, four hours, to ten minutes. It makes a big, big difference.
Mark: Yes.
Ritsuo: At Toyota Motor, the changeover time of the stamping press mold used to be four hours. Mr. Ohno requested the TPS people to reduce in half, two hours. They couldn't do that.
That's why they requested my father to do that, to help them. He did it. Then again, Mr. T Ohno was informed that they reduce it two hours, but in half. Mr. T Ohno requested them again, “TPS people, please reduce it to half an hour or 20 minutes.” They couldn't do that.
How come they couldn't reduce from four hours to two hours? How come they could reduce to two hours to a half an hour or 20 minutes? They couldn't. My father was requested to help again. At that time, he mentioned to me he wrote the concept-thinking thought, like a flash into his brain.
He mentioned, and he wrote all concept. That is what we called the Single Minute Exchange of Dies, SMED, system. That's how he made it. That is SMED.
Mark: The one part of the story that was new to me from reading your book was the golf origins. I did not think of it like a golf handicap, but I do want to say congratulations. I'm sure the Japanese people are happy about Hideki Matsuyama winning the Masters yesterday.
Embed from Getty ImagesRitsuo: [laughs] I was watching. It's great.
Mark: Great accomplishment.
Reducing your setup times from ten hours to ten minutes might feel like a great accomplishment, too! Even though you probably won't get a green jacket as a reward…
Please scroll down (or click) to post a comment. Connect with me on LinkedIn.
Let’s work together to build a culture of continuous improvement and psychological safety. If you're a leader looking to create lasting change—not just projects—I help organizations:
- Engage people at all levels in sustainable improvement
- Shift from fear of mistakes to learning from them
- Apply Lean thinking in practical, people-centered ways
Interested in coaching or a keynote talk? Let’s start a conversation.
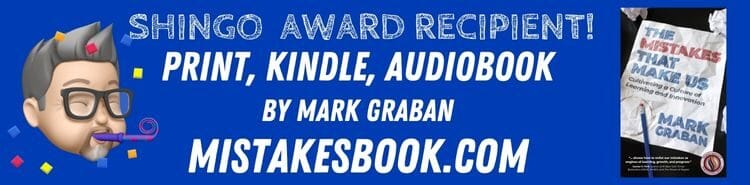
Very interesting interview, I had never heard of the term Single dandori or Single Minute Exchange of Die (SMED). This is a topic i will bring to my class and see if my Professors have heard of it. I can definitely sees its implementation in lean manufacturing.
Thanks for reading and for commenting, Joshua. I’d guess Karl knows the SMED acronym and concept. But, he might be like me, where I didn’t know the phrase “single dandori” before this podcast and I didn’t know the golf handicap origins. I did know that “single minute” referred to a single-digit number of minutes, which is not really a standard way of talking, as Shingo-san pointed out.
Hello Mark,
I think it’s great what Hideki Matsuyama did for his people and putting them on the map. Just like Josh said, I had never heard of SMED before and found it interesting. It’s definitely an important aspect of time-saving and something I would like to learn more about. Thank you for the post!
Thanks for reading and commenting, Jason. I hope you’ll check out the famed Shingo book some time:
A Study of the Toyota Production System: From an Industrial Engineering Viewpoint
https://amzn.to/32CnF08
Or his later book that takes a deeper dive:
A Revolution in Manufacturing: The SMED System
https://amzn.to/3v9B4t0