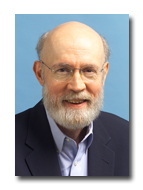
Episode #116 is a chat with Jim Womack, founder and former Chairman of the Lean Enterprise Institute, now their Senior Advisor and author of the new book Gemba Walks, available in paperback, Kindle format, iBooks, and other formats.
Here, we talk about the new book, how a gemba walk differs from “management by walking around,” some of his most memorable walks, progress in lean healthcare, and other topics.
For a link to the episode, refer people to www.leanblog.org/116.
We recorded two podcasts in the same sitting. Part two is Episode #118, with Jim's thoughts on recent developments with GM and Toyota, his reflections on the word “lean,” his thoughts on six sigma, and more.
For earlier episodes, visit the main Podcast page, which includes information on how to subscribe via RSS or via Apple Podcasts.
If you have feedback on the podcast, or any questions for me or my guests, you can email me at leanpodcast@gmail.com or you can call and leave a voicemail by calling the “Lean Line” at (817) 372-5682 or contact me via Skype id “mgraban”. Please give your location and your first name. Any comments (email or voicemail) might be used in follow ups to the podcast.
Automated Transcript
Announcer (2s):
Welcome to the Lean Blog podcast. Visit our website at www.leanblog.org. Now here's your host, Mark Graban.
Mark Graban (13s):
Hi, this is Mark Graban. Welcome to episode 116 of my podcast for March 22nd, 2011. My guest today is a returning guest and thankfully, a rather frequent guest over the last couple of years, Jim Womack, who is the founder and chairman of the Lean Enterprise Institute. He's now in the role of senior advisor to the Institute with John Shook, taking over as ceo. We're gonna be talking today about Jim's most recent book published by LEI called “Gemba Walks.” It's a compilation of his 100 email newsletters over the last 10 years or so, and they've been edited a bit. They've been reframed re-sequenced, grouped in the themes with some additional commentary and new essays.
Mark Graban (57s):
It, it makes for a really nice little book that you can hopefully pick up and take a look at. So we're gonna be talking about the book. We're gonna be talking about Gemba walks, what they are, how they differ from management by walking around. We're gonna be talking about some of Jim's most memorable Gemba walks. We'll talk about lean healthcare, all sorts about the topics. And this is actually the first of two parts where Jim will come back. We've actually recorded it part two of a podcast where we talk about the automotive industry. Six Sigma and other topics will be coming back out in a couple of weeks, so you can check for that. And all past episodes, you can subscribe leanpodcast.org.
Mark Graban (1m 39s):
Jim, thanks for joining us and taking time to talk today on the podcast.
Jim Womack (1m 43s):
Well, thank you.
Mark Graban (1m 45s):
So we're gonna talk today about your most recent book published by LEI, Gemba Walks, and I was wondering if you could tell the story behind publication of the book and, and what's been added to the essays or e letters, you know, that were previously published.
Jim Womack (2m 2s):
I started this last fall because I was gonna step down as head of LEI. It was a bit of a house cleaning activity. I had turned out exactly a hundred of these e -etters that had been sent between fall of 2001 and the end of 2010. And I thought for the record, just bundle 'em up, get a copying machine and you know, get them, give them a place to live on the shelf. As I got into it, I realized that this was really the record of thinking about what's happened to lean in the now 15 years since the Lean Thinking book that Dan Jones and I did was published. And it was really a lot here. And in addition, it fit nicely into some themes and if you took each of the essays and then having reflected on them through half of them away because they were just of the moment and took the other 50, ran them through a reman remanufacturing operation to get, get them fixed.
Jim Womack (3m 1s):
Turns out you're never in retrospect as clear as a writer as you thought you were at the time you wrote. So that I would find myself puzzling over sentences I had written 10 years earlier saying, Hmm, wonder what I meant. So there's no attempt to add content to these essays, but sometimes to pick out some topical things that were no longer relevant, but also just to fix 'em so they're easier to read. But that was the least of it. Then I had to organize them. I thought chronology at first, and then I said, well, gosh, there's some clear themes here. I talk about purpose, I talk about process, I talk about people, talk about transformation, talk about diffusion, talk about management, talk a whole lot about management and leadership. So let me organize them by themes.
Jim Womack (3m 42s):
Let me write a little essay at the front of each theme. Let me stitch the essays together, having some language that gets you from one to the next. Let me introduce the collection. And then at the very end, a section called Hopeful Hansei. Let me talk about where the community goes from here. It's not where LAI goes from here, that's not really the point. But where the lean community goes, as John Shook comes on as a new leader and as I go into my senior advisor mode, which doesn't mean I've gone anywhere, but does mean that I will be doing some different things.
Mark Graban (4m 14s):
So you, you mentioned that senior advisor role. What, what does that entail? I mean, people are, I'm sure, curious what you're researching or what you're working on right now.
Jim Womack (4m 22s):
Well, perhaps, perhaps they should send in their suggestions. What I've been doing at LEI for years and years was acting as the sort of editorial director. And I didn't write much material at all for L e I. In fact, this is the only book that you really call a book that I've done for L ei. I had done the workbook with Dan Jones seeing the whole, but I've for years tried to get books out and not just books, but other kinds of teaching material workbooks. And we've done some videos and some in the old days, some VSM software. So that's a role that still needs somebody to do. And it turns out that might be one of my skills. So I'm working on a half a dozen new products right now, not as the author, not even as the editor, but rather the advisor, the publisher's right hand, to try to figure out what form to give them.
Jim Womack (5m 11s):
Doing a lot of talking now at non-profit activities, the AMEs and SMEs and other types of activities that I've always done. But now I can do a little bit more energetically. Before it was just with my tongue hanging out, now I've got time to stay and talk to people. Always interested to know what people out in the lean community are doing, what the next challenges are. And then of course, because writing is addictive, writing is a drug that has no high, there is no rush, but it's completely addictive. Of course, I have to start working on the next project and that one is still under wraps, but there's always a next project.
Jim Womack (5m 51s):
So I'm working on that and otherwise it turns out you don't need that much more to fill your time.
Mark Graban (5m 59s):
Well, so back to Gemba Walks the book, and I, I think Gemba Gemba walk is probably a familiar term to listeners, but it might be worth recapping how a gemba walk a as you've done them, as you've seen other leaders do it, how that's different than quote unquote management by walking around as used to be kind of trendy.
Jim Womack (6m 20s):
Right. Well, Tom Peters came up with management by walking around, I think as so many things that Tom Peters came up with. It sort of came and went. The idea, there seemed to be that the senior management ought of be talking directly to customers, directly suppliers, and directly to the shop floor, into the engineer at the screen to find out what was really going on, to get new ideas, to deal with the frozen middle of those managers in the middle that were clogging everything up and interfering with the desire of just regular folks down at the bottom of the organization to get the job done. I never could see myself how that was gonna make much difference beyond the hour or two hours or day that it took the senior manager to walk because there was really no mechanism for it to lead anywhere.
Jim Womack (7m 6s):
What I've had in mind with Gemba walks for years is really very different. Look at an organization, pick a couple of their value creating activities, what we call value streams. It's easiest of course to do that in the fulfillment area, which is from order through delivery. And you know, when I say fulfillment, well, I mean production. Whether it's a good or a service that you come, some customer says I want it, you start with the first step in the process of delivering it, which might be raw material or data or something depending on what kind of activity you're talking about and follow all the way through with what happens. But you can do the same thing in product development activity. You can do the same thing in aftermarket after the product is handed to the customer.
Jim Womack (7m 51s):
It needs to be supported usually through its useful life. What happens when people try to do that? So pick a product family to make it boundable and start at the beginning and go to the end. And as you do that, you are saying, what's really happening here? Because all people who are honest know that in organizations, even in pretty lean organizations, what is actually happening is often not what's supposed to be happening. The difference, by the way, with a lean organization is that everything is visual and visible and there are countermeasures being put in place as things happen in the way they're not supposed to. Whereas in a lot of organizations, you're supposed to keep problems out of sight.
Jim Womack (8m 32s):
And then of course you have all kinds of irregular ways to do things that are not documented because the documented way don't work. So as you're walking along on Gemba Walk, what I wanna do is always talk to the people who are doing the actual work, look at what's actually happening right now, ask about the purpose of that activity. It is amazing how confusing, how confused people get about their purpose. Look at, at each step in the process, and then as you talk with the people, you begin to see whether they are engaged or not, whether they have a way to deal with the problems in their lives or not, whether they are being trained in a way that will make them more and more able to create a better process or not.
Jim Womack (9m 14s):
And whether there is, as that happens, a process of creating the next generation of process managers or not. Unfortunately, in today's world, in most processes where I take a walk, the the knot part is stronger than the doing it part. A lot of earnest intent people saying they wanna do things in a better way, but then you look at what's actually happening and there's no stability, it's really out of control. There's confusion about purpose, the ability to countermeasure things. By the way, I've tried to break myself of saying solving problems. I just say countermeasure them. You don't see much of that going on effectively.
Jim Womack (9m 53s):
So by the time you get to the end, you can be pretty sure, and this is based on many years of experience, that what you've seen is probably indicative of what's going on throughout the entire organization. You don't have to go look at everything if you look hard at one thing, starting at the bottom with the work and then back off to see what the managers are doing, and then look at the purpose from the customer standpoint and look at how engaged the people are. You just learn an enormous amount about an organization's ability to create value. And it seems to me like every senior manager ought to be able to do this. Every mid-level manager ought to be able to do this, and every frontline manager would have need to take a walk fairly frequently to see exactly how things are going.
Jim Womack (10m 41s):
That's how it would seem to me. That's not always how it's
Mark Graban (10m 45s):
Now reflecting back on these different Gemba walks you've done personally in these value streams you've walked, were there any that were, you know, you know, surprising in a, you know, a delightful way or any that were just sort of, you know, that stand out as being, you know, sort of a, a strange and unusual value stream to be looking at?
Jim Womack (11m 4s):
Well, certainly in terms of strange and unusual, I was looking at the sort of remains of a value stream when I went out to Highland Park, which is the Henry Ford plant that really made modern production possible. All of it was really pioneered at Highland Park between 1908 and 1914. That's in the hopeless town of Highland Park, Michigan. And I don't say that to offend any residents because I think at this point there hardly are any residents, actually the most striking example in the US of industrial failure. But between 19 eight and 1915, it was the most creative site, probably in the history of industry in terms of rethinking product development, rethinking production, rethinking supplier relations.
Jim Womack (11m 48s):
And so I went, gosh, I guess for the first time about 10 years ago, went out to take a a look and it's like the neutron bomb building. The building is still there, it's standing. It's a, an amazing building, really the first truly modern factory. And it's empty and it has a few records stored in it and some old pieces of cars for various reasons stored in it. But otherwise, it just sits there in an empty town with one employee sitting down at the front door reading the newspaper. And if you can figure out how to get in, which takes a lot of work, it is amazing to think that this is where the assembly line was first perfected. It's where cellular manufacturing, because Henry really was doing things themselves, even had a crude pool system, and it was all right there and it worked brilliantly made Henry the Royals, excuse me, the world's richest man, the most successful company, and then most of us just forgot about it.
Jim Womack (12m 46s):
And so it's the, the brilliant process that time forgot. And just to go through there, it's not often, I feel I'm absolutely, you know, at one with history, but there it was, this sort of felt like I was, had gone back century and here I could see the creation. So that's one interesting thing, very sort of sad thing to see what happened. I had lots of others, the ones that are most haunting are in healthcare that you do go into operating rooms and you go into all kinds of places where you see people working incredibly hard in very difficult conditions, right at the edge of science in many cases with processes completely outta control and with a striking lack of effective management and literally holding people's lives in their hands.
Jim Womack (13m 37s):
And when I do that, I must say, I always feel pretty humble that those of us who came out of a manufacturing background, you know, car parts and people are not the same thing in terms of the responsibility you feel as you're standing there.
Mark Graban (13m 54s):
Now, I, I know you've walked the gemba many times with, with our, our friend John Tucson up there at Theta Care, and in, in the book one of your epilogues or you know, additional content around an e-letter about Theta Care. You say you wrote that we're still in the early days of lean healthcare. So I was wondering if you could share some, you know, additional reflections on if these are early days. Where, where do you think this is headed? You know, compared to maybe a similar phase in manufacturing's adoption of lean thinking.
3 (14m 23s):
We'll be right back after this special offer from Conexus. Are you struggling to keep your employees engaged and motivated? Having engaged employees can be a challenge, but it's crucial for the success of any organization. That's why Kinex has created a free ebook. The Savvy Leaders Guide to Employee Engagement. It's packed with practical tips and strategies to help you boost employee engagement and drive results. So if you're ready to start making a positive change in your workplace, go to conexus.com/engage to download your copy of the ebook today. And now back to the episode. We'll be right back after this.
3 (15m 3s):
Are you trying but struggling to write your first book? I have a guy who will help Mike Ulmer, he's been a guest with me on my favorite mistake podcast. He will interview you, look at other books in your category and lay out a precise plan for you to follow to create your book. Using Mike's custom blueprint and some innovative tools, you can create a version of your book in a matter of hours to start on your author journey call or text Mike right now at 1 8 4 4, I write two. That's the letter I write as in writing a book two, the number 2 1 8 44. I write two.
Jim Womack (15m 42s):
Yeah. Well first of all, care is less early than a lot of other folks. Sure. So I admire what they've been able to do. The things that strike against you in healthcare are that while our kind of image of it is science, scientific medicine, it actually is sort of the most craft focused business there is the, you see doctors doing things because they're teacher, you know, Larry or Biff or Sally back when they were a resident, taught 'em to do it that way. And then you'll see a doctor doing the exact, treating the exact same condition at the patient in the next bed and doing something totally different.
Jim Womack (16m 24s):
And then you say, well docs, why are you doing this in a different way? And they both will tell you they were trained by the best sensei, as we would say in Lean, but the best master doctor that there ever was. And so they do it the way they were taught. And then you say, well Judy, you have any outcomes data? And it's like, you've just said something really awful because it turns out mostly they don't. So that's quite striking to get started. How can you have repeatability when you don't even know what the results are? How can you have a method that really is just basically unwritten craft that is called science and scientific medicine, and then a management system in healthcare that really is just very disconnected from the actual value being created.
Jim Womack (17m 14s):
And it's not surprising that if you think of the doctors as the most skilled people in the organization, and they're the touch labor, they're at the very bottom in terms of where the value is created. They're creating it, but they also think they should be managing it from the top. And I understand how they would feel that way, but it turns out that it's hard to be both the touch labor just looking at one point your particular activity without any reference to how the whole process works. And without any either desire to manage from the top or any patients for those patients, how you, you understand it a different way that any, any willingness to work with the managers that are trying to manage it.
Jim Womack (17m 55s):
So then you get the nurses, bless 'em, who are the only folks in the system who think about process, who they've gotta get the patient through the system, but they've never been given any training in how to do that. They're just doing it the way they learn from whoever did it before them. And they get no respect for it. And then these days you have managers that are MBAs and have been told you gotta cut cost. And of course the first thing that comes to mind is to sweat assets, which is to say, let's get everything more highly scheduled and get people to work harder because they have no feel for the gimbal. They really don't know much about how you actually create value right at the bedside. So you have this crazy management system of senior managers who don't really know how you create value of the people who most directly are creating value, who don't wanna be part of management, and then the poor nurses in the middle who are trying to square the circle.
Jim Womack (18m 44s):
So no wonder this is a very difficult area to make progress, but hey, let's look at the bright side that this patient healthcare is very sick. Fortunately the patient knows it's very sick and knows also that things are gonna get a whole lot worse now as governments, not just in the US but in most countries run outta money. So there is, I think for the first time, what I'm seeing is the widespread acceptance of the fact that things are really going to change. Now, by the way, that doesn't mean they're gonna get better because if you don't do something about the management system and trying to get the processes to work well then the only way out of the current cost deal is denial of care, rationing, price controls, whatever the, the default is a pretty ugly one.
Jim Womack (19m 33s):
So therefore the people who've really got their head in the game are saying, well, wait a minute, maybe we have to rethink everything from the top here. And in particular how we actually create value in healthcare. So without that willingness to do that, I would say this situation is hopeless. Instead, I will say the situation is fraught with potential, with positive potential, but we don't yet know how effective the lean thinkers are gonna be in trying to find a way to get better outcomes for the patient, better quality experience for both patient and staff with less cost, with less time. We just don't know how effective we're gonna be.
Jim Womack (20m 13s):
But I will say that our lean thinking is really probably the only drug left in the arsenal between what we got right now that's not sustainable and a sort of grim scene where it's basically just decon and taking things out, denying saying no, and making the experience of both staff and patients worse.
Mark Graban (20m 33s):
Now one thing you said that really resonated at the Lean Transformation Summit recently, you made a comment that CEOs should not start a lean program, but rather, you know, be the first to change their own thinking. So I, I mean, do do, do you, it seemed like that would apply to healthcare just as well. Is it? What across the industries, can, can you you share, you know, a few more thoughts on that theme?
Jim Womack (20m 55s):
Sure. Well, gosh, I just shutter all over when I hear about a program, somebody calls me up, I just got call from an airline, said they're gonna have a lean program. I said, thank you very much, goodbye. Because the history of programs is that they are done by staff people on a budget with some clear stretch goals, which probably will be met if you put up goals like that and you have no idea what's really going on at the top. Well, it's likely that people, you know, well-intentioned people in the middle or toward the bottom on the staff side, we'll find some way to make it look like you're making some progress. But what everyone will really know is that even if progress is made, it's not sustainable because there's a mismatch between process thinking implemented by an outside consultant or an inside team and what real managers do every day.
Jim Womack (21m 46s):
So this battle is one or lost, this war is water or lost on whether we can change the behavior of senior managers, middle managers, you know, junior managers. But I say the most effective thing is for the senior managers to go out, take a walk, look at how their organization actually creates value before they start talking about programs and stretch goals and ask what it is they do that most senior managers when they do go out, think that their job is to solve problems, which is completely impossible because they don't know anything and they're way, way away from the problems. And then failing that they think their job is to shout and scream and to make threats and to demand, you know, amazing feats with again, out knowing how the system works or what would really have to change to make this possible.
Jim Womack (22m 38s):
So the world would be a better place if every senior manager had some ability just to go take a look at reality, to understand it and to understand how there is often a misfit between the need to the process. Remembering that processes run horizontally across organizations to the customer to create value and the vertical, which is the way all organizations are put together. So there's that disconnect. It's just right there. It's the most fundamental issue in management is how to think horizontally in an inherently vertical organization. And that requires a lot of change in the way that managers think, but also forget the thinking. What they do doing is what's really important, not thinking.
Mark Graban (23m 19s):
Well Jim, thanks for taking time to talk about the new book Gemba Walks and, and for expanding on, you know, some of the themes around Gemba walks in general and, and some of the stories and and cons, concepts that are there in the book. I really appreciate you taking time to do that.
Jim Womack (23m 34s):
Sure. Look, I hate this final thing. I'm not through walking, you were asking what I'm gonna do. Well, I need to be an editorial director and I need to help with some other things around ei. But what I love to do most and what I think is probably the most useful is to continue to go see things. So I expect to be walking, I set a goal for myself of, I kind of like to visit an organization a week. And here in the first 10 weeks of 2011, I've done that. So that's when you ask what I really wanna do and what I'm gonna be doing. I'm gonna be out walking and I hope I see lots of members of the lean community out walking as well. And maybe we can walk together and get to a better destination.
Mark Graban (24m 18s):
Now I, is there a lean bat signal of sorts that people can shine up into the sky if they'd like you to come walk their Gemba with, well,
Jim Womack (24m 26s):
I hadn't been looking for those, but a batt signals, wow. I'm gonna have to go Google bat signals. But yeah, look, if anyone calls LEI, we can talk. This is not consulting business, this is an educational business. Just sort of teach by example, get some people together, go take a look. What you always find at the end of a walk is that your baby is really ugly. And by the way, it's not anybody's fault. The problem is that the process horizontally and the organization vertically are not aligned. And so then the question as I leave is, what do you plan to do about that? Because you could do something about it, and if you do, you will get a much better result.
Jim Womack (25m 8s):
If you don't, best of luck, you'll probably just go from program to program. So I'm available if anybody wants to take a walk, my favorite thing to do, just give a shout and we'll see what we find.
Mark Graban (25m 21s):
Okay. Well thanks a lot, Jim.
Jim Womack (25m 23s):
Sure. Bye now.
Announcer (25m 25s):
Thanks for listening. This has been the Lean Blog podcast. For lean news and commentary updated daily, visit www.leanblog.org. If you have any questions or comments about this podcast, email Mark at leanpodcast@gmail.com.
Please scroll down (or click) to post a comment. Connect with me on LinkedIn.
Let’s work together to build a culture of continuous improvement and psychological safety. If you're a leader looking to create lasting change—not just projects—I help organizations:
- Engage people at all levels in sustainable improvement
- Shift from fear of mistakes to learning from them
- Apply Lean thinking in practical, people-centered ways
Interested in coaching or a keynote talk? Let’s start a conversation.
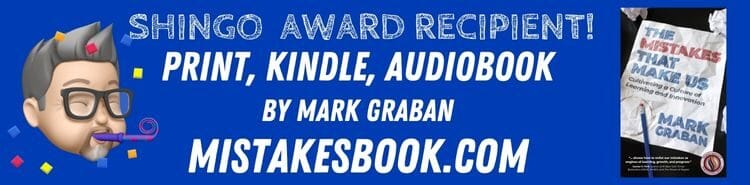
Mike Lombard has a blog post with some highlights:
http://hospitalkaizen.blogspot.com/2011/03/top-3-insights-from-jim-womack-on-lean.html
Very good interview. The analysis of the health care situation is excellent, though somewhat depressing. I do think there are a couple of quivers, in addition to lean, that can produce results.
For one, there are some system wide changes (outside/above the level of any one organization) that could improve things. The current system has some extremely bad systemic issues that lean thinking could help with, but also they could be improved without lean thinking (partially because they are so bad there are lots of ways to improve).
Secondly, Clayton Christensen’s ideas on disruptive innovation have huge applicability to health care, in my opinion. http://management.curiouscatblog.net/2009/02/19/applying-disruptive-thinking-to-the-healthcare-crisis/
You can also read this summary of the interview by the LEI’s Chet Marchwinski:
http://www.lean.org/common/display/?o=1786
[…] Jim Womack, lean blog podcast #116 – Great, as you would expect. Includes a great explanation of the problems that have made adopting lean ideas in medicine, which somewhat counter-intuitively includes the reluctance to use the scientific method/pdsa to examine results. […]