Hard times curtail Park Nicollet's ambition
Minnesota's Park Nicollet health system is often held up as one of the leading “lean healthcare” examples in the U.S. As I mentioned in my book, Lean Hospitals , the system claimed $7.5 million in savings from lean improvement events in 2004, reinvesting the savings back into patient care.
The linked article discusses current financial problems, including layoffs of 7% of their workforce. Initial questions that might come up might include:
- Were these layoffs because of Lean?
- Why didn't a Lean strategy help prevent the layoffs?
- Would things have been worse without Lean?
I have no idea – those are legitimate and honest questions, and I claim no inside knowledge. There are people asking, “Why didn't Lean save Toyota from a financial loss?” The world isn't that simple. Lean isn't a cure-all or silver bullet for a manufacturer or a hospital.
Some details do emerge from the Park Nicollet news story.
Park Nicollet Health Services is the Twin Cities' smallest hospital and clinic group.
But its ambitions were big.
During health care's boom years over the past decade, Park Nicollet invested heavily to compete with its far-bigger rivals, Allina and Fairview. It sent executives to Japan to learn Toyota's “Lean” production process, adopting productivity techniques that would later spread to the rest of health care. It installed not one but two electronic medical record systems, one after the other, and borrowed millions to build new specialty centers.
Then the recession hit, and hospital groups big and small saw their rosy business projections fall apart.
The article details how their small market share (about 6%) may give them structural disadvantages against two competitors who each have >20% share.
The CEO is given credit for being a strong proponent of Lean:
He also applied business ideas and technology to health care. Among them was the Toyota “Lean” method, which studies work processes to reduce waste and raise quality. Devotees say anything can be “Leaned” — from improving the flow of instruments in operating rooms to assigning pillows to each hospital room so a nurse doesn't have to walk down the hallway to fetch one.
Yes, anything CAN be “leaned,” but part of the question comes back to “are you ‘leaning' the right things?” Freeing up nursing time is, I agree, one of the most important things you can do in a hospital — for the benefit of patient care and the hospital itself.
Some complaints emerged:
Staff friction
The succession of changes wore down staff. Some believed they had become incidental to the work of caring for patients. “People are kind of tired of management fads,” said Kent Searl, a nurse in the intensive care unit who joined Methodist Hospital in 1992. “We were offering suggestions and getting pushback on safe staffing, yet being told to reduce the number of pens and pencils.”
I can see where this would be frustrating. If you're not addressing the core issues for the hospital, for patients, and staff – say, you're dabbling around the edges with a kanban system for pens at the nurse's station – people might see Lean as a distraction or a bit of foolishness.
If you're focusing on the right things, the important things, staff members won't feel this way.
That said, if staff members are always saying “we need more staff, we need more staff” and that is just an old habit (as opposed to being supported by data), then hospital administrators might be right in not approving the increases – and it might be true that current staffing levels are not “unsafe” (safety can be a staff excuse for forcing staff increases… if management says no, you accuse them of not caring about safety).
Either way, when conflicts like this come up, communication and leadership are key. Even if it is the right decision to NOT increase staff, you have to communicate “why” and gain buy-in with the staff. Otherwise, they might be resentful, and morale can/will suffer.
I hope things are going well with Lean at Park Nicollet. The news article, in keeping with the “things are going badly” theme of the article, may have just focused on the negative aspects of Lean. Are they still saving $7.5 million a year or more through their Lean events?? Maybe not, but maybe that just went unsaid in the article.
Please scroll down (or click) to post a comment. Connect with me on LinkedIn.
Let’s work together to build a culture of continuous improvement and psychological safety. If you're a leader looking to create lasting change—not just projects—I help organizations:
- Engage people at all levels in sustainable improvement
- Shift from fear of mistakes to learning from them
- Apply Lean thinking in practical, people-centered ways
Interested in coaching or a keynote talk? Let’s start a conversation.
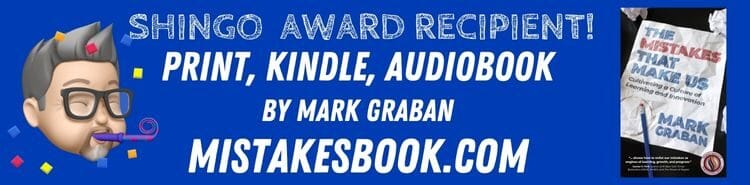
I think the “Lean” methods employed by Toyota have presumed some amount of growth. If you just reduce waste, thereby freeing up time for people you have just moved the waste to a new category of muda (motion to waiting for instance) UNLESS you can occupy those people with new value creating tasks. I think maybe the hospital this case and Toyota (in North America anyway) might have both been overly optimistic in adding new capacity (new factories in Toyota’s case and sattelite clinics in the hospital’s case). If you can’t sell the new capacity then you don’t get all the benefits of waste reduction. The Toyota methods have been employed quite well and have delivered excellent business and financial results (especially using cash accounting metrics instead of the accrual accounting methods which are more popular on this side of the Pacific) because of Toyota’s steady growth. This growth held up well until the current economic contraction which is a historic recession, i.e. it is not a normal cyclical cool down, it is driven by real reduction in demand not strategic overproduction (we’re not just idling capacity to burn off inventory, we actually have decreased demand right now). I think before the hospital dumps the TPS they should use this time to further refine their processes and keep as many people occupied in this (learning how to solve problems) as they financially can in the short term understanding that this will negatively impact their short term financial statements. They will be better positioned when demand comes back to take advantage of the effeiciencies gained from implementing TPS. This assumes that they are doing it right.
Lots of food for thought, Mark. Park Nicollet’s situation is a great illustration that Lean provides no guarantees. Their small market share and financial cushion were exposed by investment losses in the last year.
No doubt some improvement did occur in the past several years as a result of the lean effort, but I would bet that no real alteration has yet occurred in the management culture. The management seems to still operate from the “cost cut your way to prosperity” model and as Bruce says above, they don’t seem to have yet grasped the idea of reinvestment of freed up resources (time) in new value-added activities.
Furthermore, reading between the lines, the lean effort does not seem connected to the clinical staff, where they hold the wheel (of responsibility), take ownership of problems and lead the hospital on a course of improvement that simultaneously upgrades care and decreases costs. It’s clear that something is not right in the Lean transformation when a veteran ICU nurse grows “tired of management fads” and physicians are required to work harder (more patients per day) instead of smarter.
All this having been said, I agree with you that things are not going badly at the hospital as they hunker down and conserve their financial capacity. I wonder what might happen if they chose this time of crisis as an opportunity to do something new that had real upside potential?
/Dr. Pete
I participated in a factory kaizen event with some Park Nicollet people a few months ago. They were a great bunch of folks. I hope things turn for the better for them.
I do see the pitfalls of launching growth initiatives at the same time as the Lean journey. Improvement is always overburdening staff if the existing waste is just replaced by the growth. The notion of building in improvement capactiy for staff ends up being way down the road and will limp along your progress.
The statement ‘The succession of changes wore down staff’ in lean speak seems like an oxymoron. It implies changes were ‘imposed’ on staff as distinct from staff identifying the root causes of problems and implementing ‘their’ solutions.
The similarities between this story and Toyota’s recent experiences are a stark reminder that day-day operational excellence alone is not the only factor in the equation. These two organisations are (currently) very efficient at delivering something few people (customer) value – they have tripped over the first principle of lean – go ask what the custmer values not what you think they value.
Tom
I don’t think people should be shocked that a Lean company stumbles or even fails unless they think Lean is a suitable substitute for every best practice management across the board. I think many Lean advocates have a pretty narrow view of management. It is equally presumptuous to assume than only Lean companies can succeed which in fact some lean advocates would have us believe.
Growing is important for lean to work long term.
This is true because the significant improvements in productivity that lean produces(3-5% at Thedacare) eventually lead to redeployment. If there is no new growth redeployment is very difficult.This doesn’t happen in healthcare organizations for years because turnover is high in the industry(8-15%) but eventually the improved efficiency catches up.
The other point is that business strategy and lean are two different things.Strategy is based on market place conditions and an assessment of products and customers. Lean is the philosophy and methodology to operationalize the strategy. I can safely speculate that Park Nicolet would be doing much worse if it wasn’t for it’s lean operations. They are a great organization and will weather this economic downturn coming back stronger.This may require a strategic direction change but their commitment to lean will be critical to their long term operational and financial success.
Mark, your comments about employees seeing the management of pens and pencils as “out of synch” with what they believe are more pressing concerns is right on the money but perhaps not strong enough. The good name of “Lean” takes a hit when action plans and continuous improvement projects are not driven from the “bottom up”. Misapplication of the proven approach makes it easy for detractors to blame “Lean” principles and methods for landing projects on the list that don’t seem to make sense. Of course, in reality, it’s how “Lean” is being applied causing the problem.
When too much damage of this sort occurs, it ultimately blocks effective communication. Instead of “Lean” being an important “short-hand term” interpreted by all stake holders as equivalent to “a better way”; the term now represents principles and methods producing a mixed bag of benefits and problems. Under these circumstances, as Leadership continues to use the term thinking they are still communicating “a better way”, in reality, many listeners are interpreting “Lean” in a less positive way – buy-in begins to suffer as a result. This type of communication problem can seriously hinder any plan to maximize the benefits of deploying “Lean”.
Has anyone thought that maybe “lean” doesn’t work in a service industry. It’s easy to assign duties and make processes more efficient when you’re on a line but when it comes to patients and other people-related services Lean does not fit. There are far too many changing and unknown variables when it comes to treating people than when building a car. Running around with stop watches on a nursing floor and putting up charts about flow and such do not encourage “buy-in”. Nurses and doctors are there to serve the patients. They do not view patients as part of an assembly line. They are real and don’t fit into a specific brand. The complaints aren’t that “we need more staff”. It’s “we’re trying to do our jobs but Lean is getting in the way of my job”. When you take physcians and nurses away from their duties so that they can learn Lean you take away what that person has studied for and what a hospital needs, to care for the patients. To most people in the health care profession Lean is just another money maker/gimic for a person who wrote a book or for popularity with other CEOs. There have been many before and there will be many more.
The sincere comment from “anonymous” above raises a valid concern – and I am sure the commenter is not alone. Similar reactions have occurred in many places before and often with a legitimate point-of-view as their basis. So here is a major concern of mine:
“Will “Lean” rush into the healthcare industry with the same successful, but frequentlly problematic, approach used in manufacturing, or will lessons learned from implementing Lean in other industries advance implementation practitioners forward as they cross over into healthcare?”
Lean is about adding or strengthening value, not taking it away. Assuming the commenter has first hand experience with the implementation of "Lean" in the helathcare industry, and the comments expressed represent important stakeholder groups like physicians and nurses accurately, then something has gone wrong. These groups should be driving "Lean" forward because they see "Lean" as good. These groups should recognize “Lean” as a way to get more of what they want and less of what they don’t want.
Implementing “Lean” in compliance with such a positive standard is possible and it is not difficult, it just takes the right process and a desire to make it work.
To comment on anonymous and Craig above: if the lean implementation really does pull doctors and nurses and nurses away from patients and cause them to run around with stopwatches and put up value stream maps on the walls then it isn't being done right. Mark G, the host of this blog, calls some implmentation LAME (lean as misguidedly executed). Reducing time with patient (some of which but probably not all is value added time) wouldn't be a rational objective in a well executed lean implementation. I would gues that when it came to time, the early part of the implementation would examine the time NOT spent on patient care and find out how to reduce that time (thereby increasing the ratio of value added time to non-value added time). That might mean stop doing things that don't add value and make the necessary no-patient things easier and faster (like making sure that nurses don't spend a lot of time looking for sphygmomanometers when they could actually be using one on a patient instead of walking around asking people if they have a spare sphygmomanometer).
I would think that a lot of error reduction and poka-yoking would be a big part of the early implementation as well. Most people receive this part well because in the lean methods this really comes down to respecting the inherent limitations of human performance — be the humans, line workers or RNs — and people generally like it when you repsect their humanity. In past methods we have we just say "They should just be able to {insert something that sounds easy but is really hard when you have to do it a bunch of time in a crazy ruch and disorganized environment}". I like to call that "shoulding on people." I would hope that anonymous would give another sensei a chance – one that has a lean philosophy and not a lame one. The concerns of Craig and anonymous are certainly valid but the experience doesn't match what lean really is. Somebody has given lean a bad name by taking people away from the very important work of patient care and made them run around with stop watches. Stop watches aren't a big part of lean. Sometimes you need them to get a rough estimate of cycle time in repeating discrete manufacturing proces or to measure basic work content or motion time maybe in quick changeover activities they are needed sometimes too, but I have benn doing lean activities for 7 years and I have spent precious little time with a stopwatch in my hand (thankfully) – it should not be a big part of you lean journey.
I do disagree with anonymous that service industries (including healthcare) aren't good fits for lean. I have done a lot of stuff in product development, marketing, IT, and HR admin and it fits quite well. I would think that health care would fit well as well (I have no direct experience). It is a mix of cognitive creative work and procedural work like most service industries. You just have to be able to elevate the paradigms of the TPS up the ladder of abstraction a little bit and you will find that the methods and philosophies of lean apply well in most situations. It might look a little different but value added time exists, non-value added time exists, errors happen, compexity exists in all types of work. Lean will improve those things.
Thanks for carrying my mantle, Bruce! Appreciate the thoughtful comments.
I will probably write a separate blog post sometime about this discussion.
If Lean is being done properly, it is a HUGE benefit to the nurses. It shouldn't be an annoyance or hindrance. I've seen nurses and techs come and give big hugs to lean implementation team members because lean improvements were making their work EASIER, allowing them to provide BETTER patient care.
Nurses should DEMAND lean thinking in their hospitals.
To the anonymous commenter, if you've come back at all, please email me and I'll send you a free book if you want.
Mark
I may be joining a team focused on efficiencies and cost control in a hospital food service program. How would you (or others reading this) advise me on approaching both the hospital and other members on the team. I believe successful change will ultimately come from the staff employed in the facility and building a culture that enables that type of growth will show results.
Steve- good luck to you, no easy answers, but I'll try:
1) Make sure the staff is involved (that lean isn't being "done to them.")
2) Make sure purpose of lean is clear (to improve customer service, quality, cost).
3) Make sure there's no risk of lean leading to layoffs, alleviate this fear and commit.
4) Have the team members be involved in defining the problem. Identify waste WITH them first hand at the gemba.
5) Make sure the team is involved in the countermeasures and solutions. They need to own the change.
6) This won't happen in a week. Sometimes you need to go slow to go fast.
I am a civil servant who works in one of the many Benefit Delivery Centre (BDC) in England where LEAN has been implemented. From the start it has brought nothing of value that a qualified manager should not or should not be doing anyway & it has not done any visibly good or made my or others work easier. The only people who implement it are the usual sycophants, known as LEAN champions whose only motivation is personal & come across like St Paul after his conversion on the road to damascus when they speak of LEAN. I cannot believe that nurses would hug LEAN reps in the way described. It sounds like something out of a communist propaganda pamphlet!
Salvatore – thanks for your comment. You can choose not to believe me if you want. And it wasn’t a nurse hugging a “lean rep” it was a nurse hugging a peer co-worker. We were teaching the nurses and techs how to improve their own work…
Sounds like you are a victim of what we call, on this blog. L.A.M.E., or Lean as Misguidedly Executed. If you just have sycophants running doing nothing that benefits the staff or the patients, that’s not Lean, or at least it’s not effective Lean. I’ve read a lot from John Seddon about how Lean has been so badly misapplied in the British civil service… but where I disagree with John is that he completely discounts Lean… I criticize Lean done badly and still have hope that it is being done well more often than not.
For more: http://leanblog.org/lame
As a physician at Park Nicollet I have recently been reviewing all the earlier hype about the benefits of “lean”. Now, 2 years after Wessner’s forced exit nothing more is heard about it. I wonder how much it cost to send a dozen persons to Japan (along with all the other silly expenses involved with lean implementation). I never saw any change in my practice. I think there was a major case of self-aggrandizement going on. Nothing actually ever improved. Of course the administrators gave themselves nice raises while the rest of us took a 5% salary cut. There is the unfortunate tendency for administrators to want to administrate — that is, to do something to show that they are actually performing a service worthy of their bloated salaries. This usually leads to foolish ventures such as lean. I have suggested that we pay our administrators and then ask them to stay home and not do any administrating. I think the rest of us would all be better off.
“Leaders” giving themselves raises while cutting the pay of workers is abysmal behavior, whether it’s American Airlines (as has happened there) or a hospital, if that’s indeed true at Park Nicollet.
I’d disagree, though, that Lean is “foolish” if you look at the physician-driven improvements in quality and patient safety, access, and cost that so many hospitals and health systems are seeing around the world.
I’m not familiar with the specific drivers of Dr. Levitt’s concerns, but from a Lean standpoint, I can say that Park Nicollet’s quality and operational leaders have learned much about our Lean work over the past 9+ years.
Have we made mistakes along the way? Of course we have. Have we learned from them? Absolutely. Some of the most important things we’ve learned relate to the “culture of change,” and we continue to learn and bring that new knowledge to our improvement work, every day.
We “practice” Lean just as our physicians practice medicine, applying the scientific method of Plan-Do-Check-Act to everything we do. We’re not only committed to learning from our missteps, but also building upon the things we’ve done well up to this point – and they are many.
One key thing we’ve learned along the way is that our improvement efforts need to be increasingly focused on processes that directly benefit our physicians. We’ve made several adjustments to our quality model and approach to help make this so, and we must continue to do so going forward.
“Lean Thinking” is but one element of our improvement model, but it’s critical if we expect to successfully transition from volume to value-based care. We must also continue to learn from our mistakes. Our quality approach and reputation will be critical in the ACO world, and they are among the many strength that we’ll be bringing to our soon-to-be partnership with HealthPartners!
Having used LEAN in both medical and aerospace and military settings, I have learned that it is ALL about the Leadership. LEAN works when the leaders engage in serving the organization rather than themselves. It is totally useless as long as leaders are protecting their turfs or empires. One can be the best Lean facilitator or partner in the world, but if the leader is in it for themself, all is lost!
There is one major misstatement in my earlier comments about the Lean implemenation at Park Nicollet. I stated that the physician took a 5% pay cut in 2009 and that is not correct. They actually received a pay raise — my raise was approximately 10% in 2009 over 2008.