
This is LeanBlog Podcast episode #42 with Dr.C. Martin Hinckley, of the firm Assured Quality. He is the author of the book Make No Mistake!: An Outcome-Based Approach to Mistake-Proofing, available through Productivity Press. We'll talk about his book and approaches for teaching people how to develop mistake proofing in processes.
For earlier episodes, visit the main Podcast page, which includes information on how to subscribe via RSS or via Apple Podcasts.
LeanBlog Podcast #42 Key Points & Links
- Some mistake proofing examples from Dr. Hinckley's site
- Upcoming webinar on mistake proofing on May 15 (via http://www.visualworkplace.com/)
If you have feedback on the podcast, or any questions for me or my guests, you can email me at leanpodcast@gmail.com or you can call and leave a voicemail by calling the “Lean Line” at (817) 372-5682 or contact me via Skype id “mgraban”. Please give your location and your first name. Any comments (email or voicemail) might be used in follow ups to the podcast.
Please scroll down (or click) to post a comment. Connect with me on LinkedIn.
Let’s work together to build a culture of continuous improvement and psychological safety. If you're a leader looking to create lasting change—not just projects—I help organizations:
- Engage people at all levels in sustainable improvement
- Shift from fear of mistakes to learning from them
- Apply Lean thinking in practical, people-centered ways
Interested in coaching or a keynote talk? Let’s start a conversation.
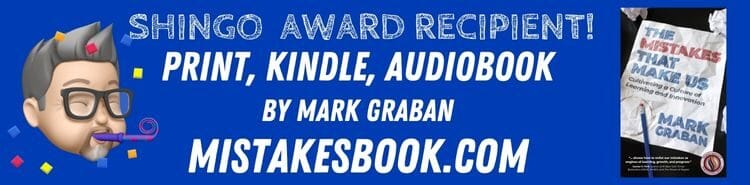
Is pokayoke all about preventing errors from happening in the first place or does it also include techniques to prevent errors from causing damages, such as rubberizing a wrench so if it slips it wont scratch or dent something, or a pan to catch accidental spills etc
I would classify rubberizing a wrench or spill pans as a part of the 6th S in the “5S Family”: Safety
Dave i though safety was protecting humans, that what most people think of, do lean people generalize it to also protecting parts or places from accidents too?
to Mike — I asked Dr. Hinckley to respond.. but my take is your examples would be a type of error proofing, something that lessens the impact of an error. Preventing the error from happening altogether would be ideal, but this isn’t always possible.
To Dave’s point… I wouldn’t call this “6S” since it’s not necessarily a safety example (a rubberized wrench would still hurt if it landed on your head) and I personally dislike taking “safety” onto 5S… just because it starts with S.
Safety is important, it’s critical. It should be a priority in everything, not just cutely tacked onto 5S, I think.
I got the safety piece from prevention of spills, people slipping, = safety.
Perhaps a more appropriate S in this case would be “shine”.
I find myself disagreeing that rubberizing and pans fit into the mistake proofing realm. In my mind, mistake proofing removes variance in a process so that quality improves.
Preparing for a mistake (rubber and pans in this example) is not poke-yoke (IMHO) because it is dealing with a mistake, a variance that has already occurred. Therefore, the action of dealing with the problem must be put into another lean philosophy bucket such as cleanliness or safety.
A better example of poke-yoke (IMHO) in these examples would be to make it so that the wrench won’t fall, and making it so that the spills won’t occur.
Fun stuff, thanks for reading my thoughts. =)
Dave – I agree with you that a spill pan is not the BEST error proofing. But sometimes you have to be practical. I’d define error proofing as anything that prevents a problem from occurring (physical defect or a process defect).
In medicine — if they’re trying to put a breathing tube down a patient’s airpipe, sometimes they’ll go down the foodpipe (pardon my non-technical terms). You can’t prevent this, at least with current technology. So they made the error easily detectable with a squeeze bulb. If the bulb doesn’t whistle, they know they’re in the foodpipe and they can try again.
I’d call that error proofing — it makes the error easily detectable so it can be reversed.
hmmm, I’d compare the whistle to an Andon light instead of a poke-yoke fixture.
The whistle is an indication that something went wrong and action is required. Poke-Yoke makes sure nothing goes wrong. I have a hard time deviating from the strictest definition when the subject of removing variances comes up.
You can call me a lean-fascist now, or “Lord Kanban”, as I am popularly known. =)
That’s the neat thing about lean to me, the answer is probably somewhere in the middle. We are only limited by imagination, and are by no means done growing.
Poka-yoke, or mistake-proofing must achieve at least one of four functions to be effective:
1. The product or process must be simplified to eliminate the opportunity for an error,
2. The error must be controlled or prevented,
3. The process must be shutdown, or
4. There must be a warning that the process is not adequately controlled.
Rubberizing a wrench so that it won’t scratch or dent an object is a form of mistake-proofing since it controls or prevents scratches or damage. However, there may be better control methods. To Illustrate, in some applications it may be possible to control the motion of the wrench, or it may be necessary to put a protective barrier between the wrench and the product. The latter solution can be very important if dropping the tool can damage the product or cause other safety problems. There is one case where a dropped tool caused the detonation of a rocket. Tools are now strapped to workers so that the drop distance is limited in such applications, but the attachment of the tool to the worker may not be mistake-proofed. In the electronic industry, a tool that slips off the fastener may destroy a circuit board, requiring a more robust barrier than coating the tool.
The key point is that the mistake-proofing solution generally has to be adapted to the specific task, and there is not a single solution that provides a complete description of the form of mistake-proofing required. Note, however, that each of these solutions (protective coatings, attachment of tools to the worker, and physical barriers between products and tools) all are based on the same principle – a barrier is placed between the tool and the product for protection.
With respect to spills, a better solution than a pan to catch spills (such as a pan under a washing machine) is determining the cause of spills and preventing them. Most of us are not happy if our car leaks oil, and putting a pan down to catch oil spills is not the ideal. Thus, while the pan may be considered a form of mistake-proofing it would be a very weak solution. We need to raise the vision with respect to what can be accomplished with mistake-proofing.
Martin Hinckley
Awesome examples Dr Hinkley.
Right now im a painting contractor so im a little crazy about spills… I sometimes run paper from the front door to the room im working in. Also I put my open paint cans and lids on top of something or of to the side more out of the way and not in the middle of a room or middle of a walking path(less-common sense?)
I do have more pokeyoke ish examples. I usually remove shutters to paint houses. Doing that on an extension ladder can be a little tricky to do and its easy to drop screws now and then, often they fall into plants/bushes and cant be retrieved. So I started using a magnetic wristband to collect/hold them. Not only have i not dropped a single screw nail or bit since, but the process is now faster and easier.
Mike, I think you examples are awesome too! Great Job. I apologize for not responding sooner. I have been on travel.
There are three levels of Poka yoke depending upon what it allows & prevents.
Level 3: Detects a defect after it has been made before it reaches the next operation.
Level 2: Detects an error in the process of it occurring, before it result in a defect.
Level 1: Eliminate error at the source, before it occurs.
Although Level 1 is best & in that hierarchy, it is not always possible & practical to go for Level 1 so depending on situation you can choose other levels also.
From this point of view I think the Rubberizing a wrench may be Level 3 but can be better solutions (as Dr. Martin has mentioned) at Level 1 & if not possible at least Level 2