I'm an invited participant in LinkedIn's “Influencer” program, where I can essentially write articles/posts that LinkedIn users can subscribe to. I currently have over 41,000 followers there, which gives me an opportunity to spread messages about Lean, Kaizen, and leadership to a broader audience. I am posting there about twice a month.
Here is my most recent piece – click on the title or image… and the full text is now included below, here in this post…
No Time for Improvement? Bah! Make Time for Improvement!
When I talk with organizations about employee engagement and continuous improvement, leaders often complain that they don't have time for improvement. Or, they say their employees are too busy to participate and managers are too busy to get involved.
So we get stuck in classic Catch 22: we know things are broken but because things are broken, we don't have time to fix our processes and systems. Sometimes, not having time for improvement leads to a vicious cycle where things get worse, meaning we have even less time for improvement… and the cycle continues.
The “we don't have time” statement often goes completely unchallenged. We can't just give up on improvement. I always like to challenge organizations to have “lack of time” be the first problem statement that they have to solve in their continuous improvement work.
Do we really not have time?
Sometimes, we learn the “lack of time” is more of a perception than a reality. Even in the busiest of organizations, there are bound to be slow periods during a day, week, or year when improvement can be done. It's important to have a system in place that has ideas teed up and ready to go when time becomes available (whether that's a bulletin board or an electronic system). That way, you're not caught flat-footed with nothing to work on.
Some organizations, especially in healthcare, throw away time that's available for improvement by sending nurses or other staff home early when patient volumes are low. If you're sending staff home early and also saying “we don't have time for improvement,” a more accurate statement would be “we're choosing not to utilize time for improvement.”
Don't view improvement work as “non-productive” time
Since workplace improvements benefits customers (or patients), staff, and the organization itself, leaders should be willing to pay staff for so-called “non-productive work” (time not spent being a nurse or not assembling cars).
Many hospitals are held hostage by their daily productivity targets, often expressed in “hours per patient” or some such number. One hospital leader complained “our daily productivity target is the thing that gets in the way of us ever improving our daily productivity.” They were expected to hit that target each and every day. There was no wiggle room to have higher labor cost on day if that would lead to lower labor cost later on. Leaders need to take a long-term view – spending a little bit on labor here to get improvement in the future.
There was a recent news story about a State of Louisiana “online suggestion box” system that I predict is doomed to failure. One reason is that workers were specifically told that they could NOT submit suggestions while they are on the clock. You can't make this stuff up! What a ridiculous policy.You WANT workers using work time to figure out how to improve the workplace… not just doing work.
Toyota is willing to pay for time spent on improvement
Toyota takes a very progressive and long-term view on kaizen and employee engagement. They say every employee (EVERY!) has two jobs: First, to do their work and, second, to improve their work.
When I recently visited the Toyota plant in San Antonio, they said employees will get paid overtime, before or after their shift, to work on improvements that their managers have approved. Toyota is spending a little bit, but think of what they are gaining in terms of improved quality, productivity, and employee morale.
Toyota isn't being nice or philanthropic by allowing time for improvement – they are doing what's in their best interest as a company.
Managers need to make time too
Even if we help create time for employees, managers might still complain they don't have time. Well, make time! If something's important, you make time for it. Saying, “I don't have time” is playing the victim. A more accurate statement is, “I choose to not make time.”
Managers can try to reduce the amount of time spent in meetings and other activities that really don't help improve the organization. Many healthcare organizations, following the lead of ThedaCare, are establishing two-hour long “no meeting zones” in the morning to free up time for managers to get out of their offices and conference rooms to work on improvement with their employees.
Either you can… or you can't
Where there's a will, there's a way. Don't just give lip service to wanting to improve or wanting to have a culture of continuous improvement. Find time. Make time. As Henry Ford said, “Whether you think you can, or you think you can't–you're right.” If you think you can't improve and that you don't have time, then you're right. You have the choice, however, to MAKE time for improvement.
Please scroll down (or click) to post a comment. Connect with me on LinkedIn.
Let’s work together to build a culture of continuous improvement and psychological safety. If you're a leader looking to create lasting change—not just projects—I help organizations:
- Engage people at all levels in sustainable improvement
- Shift from fear of mistakes to learning from them
- Apply Lean thinking in practical, people-centered ways
Interested in coaching or a keynote talk? Let’s start a conversation.
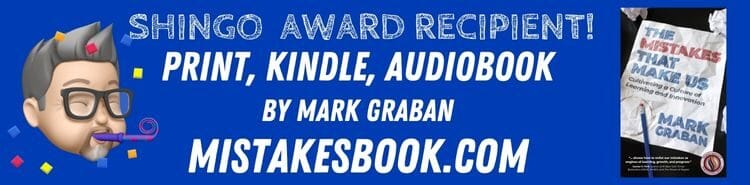