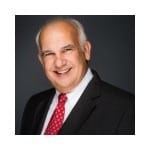
LeanBlog Podcast #16 is the first part of two with Jim Baran, the Owner of Value Stream Leadership, a leading recruiting firm that specializes in Lean talent. I've known Jim for a few years now and he's helped me and some colleagues in the past. He's a great recruiter who really takes some interest in you and your career. If you're looking to make a career change or if you're looking for lean talent, I can personally recommend him.
In our discussion, we talk about the state of the job market for folks with lean experience and what helps a lean candidate stand out in the marketplace. If you enjoy this podcast, I hope you'll check out the rest of the series by visiting the LeanBlog podcast main page.
Show Notes and Approximate Time, Episode #16
- 1:30 About Jim, his background with lean, about his firm
- 2:50 What does it mean, “retained search firm”?
- 4:40 Jim's firm defines lean as “Toyota Way leadership” — Toyota Production System AND the Toyota Product Development System
- 5:00 How is the job market for lean talent, generally speaking?
- 6:30 People “used to hire forktruck operators out of Toyota” because they thought they knew the secret sauce
- 7:40 Jim Womack's email about the end of “the lean tool age”
- 8:00 How do you consider someone's individual or local lean accomplishments versus a good candidate having been in a prototypical lean company?
- 9:30 What are Jim's 5 profiles for excellent lean candidates?
- 10:30 Been in the Toyota Product Development System market very heavily lately, the talent with experience there has been slim
- 12:30 The market for lean in services areas
- 16:00 What about recruitment for executive level positions?
- 21:45 Harder to find people who can use lean to drive growth or revenue rather than only reducing costs/waste
If you have feedback on the podcast, or any questions for me or my guests, you can email me at leanpodcast@gmail.com or you can call and leave a voicemail by calling the “Lean Line” at (817) 372-5682 or contact me via Skype id “mgraban”. Please give your location and your first name. Any comments (email or voicemail) might be used in follow ups to the podcast.
Visit the main LeanBlog Podcast page with all previous episodes.
Please scroll down (or click) to post a comment. Connect with me on LinkedIn.
Let’s work together to build a culture of continuous improvement and psychological safety. If you're a leader looking to create lasting change—not just projects—I help organizations:
- Engage people at all levels in sustainable improvement
- Shift from fear of mistakes to learning from them
- Apply Lean thinking in practical, people-centered ways
Interested in coaching or a keynote talk? Let’s start a conversation.
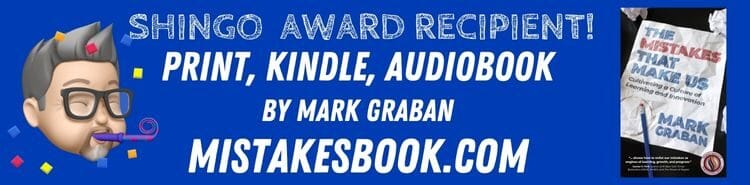
Hats off to Mark for coordinating another great interview! One of the things that I picked in the interview was Jim’s comment that he searches for ‘Set Base Design’ skills in his recruit for lean professionals. This was the first time I heard of this methodology, so I did a Google search and found an ASTM article written in 1996 by Sobek & Ward entitled “Principles from Toyota’s Set-Based Concurrent Engineering Process”
Is anyone familiar with this product development methodology, and if so, do you have experience in applying it in your organization? I would be curious to learn some of the details on how this system improves the product design cycle, especially in a culture that is accustomed to designing products in a “Point-Based Serial Engineering” manner.
If you want to learn more about set-based design, there is a good chunk of the book Product Development for the Lean Enterprise by Kennedy. It outlines the work of the late Al Ward who did research on lean product development.
I’m not sure why a company would call out set-based design as a specific need in a hire. Many companies do this but don’t have a name for it, but also without the serious learning context that Toyota brings into it. It’s an excellent tool for planning product development roadmaps in my experiences.